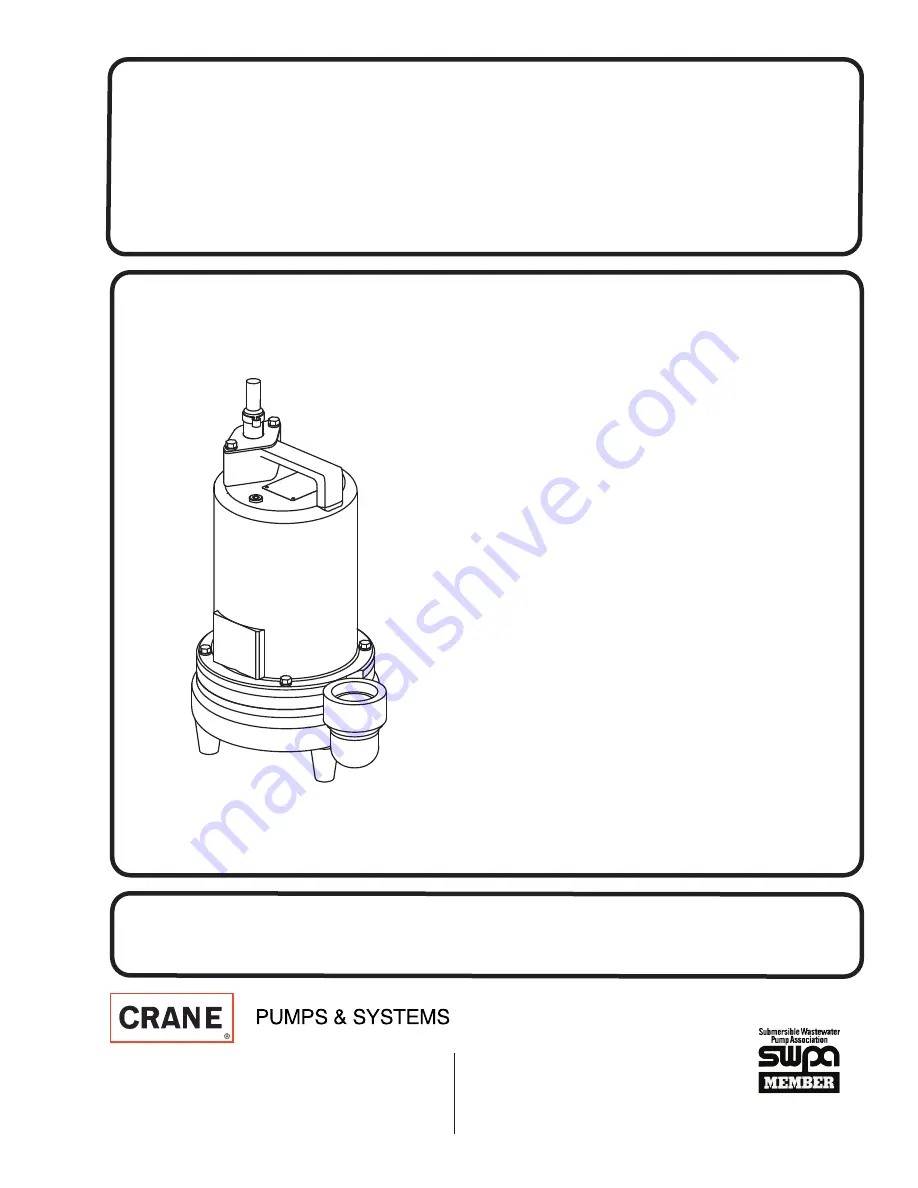
A Crane Co. Company
BARNES
BARNES
®
INSTALLATION and OPERATION MANUAL
Submersible Effluent Pumps
IMPORTANT!
Read all instructions in this manual before operating pump.
As a result of Crane Pumps & Systems, Inc., constant product improvement program,
product changes may occur. As such Crane Pumps & Systems reserves the right to
change product without prior written notification.
420 Third Street
83 West Drive, Bramton
Piqua, Ohio 45356
Ontario, Canada L6T 2J6
Phone: (937) 778-8947
Phone: (905) 457-6223
Fax: (937) 773-7157
Fax: (905) 457-2650
www.cranepumps.com
Form No. 106991-Rev. U
Series: EH-HT
0.5 & 1.5 HP, 3450 RPM, 60 Hz.
High Temperature