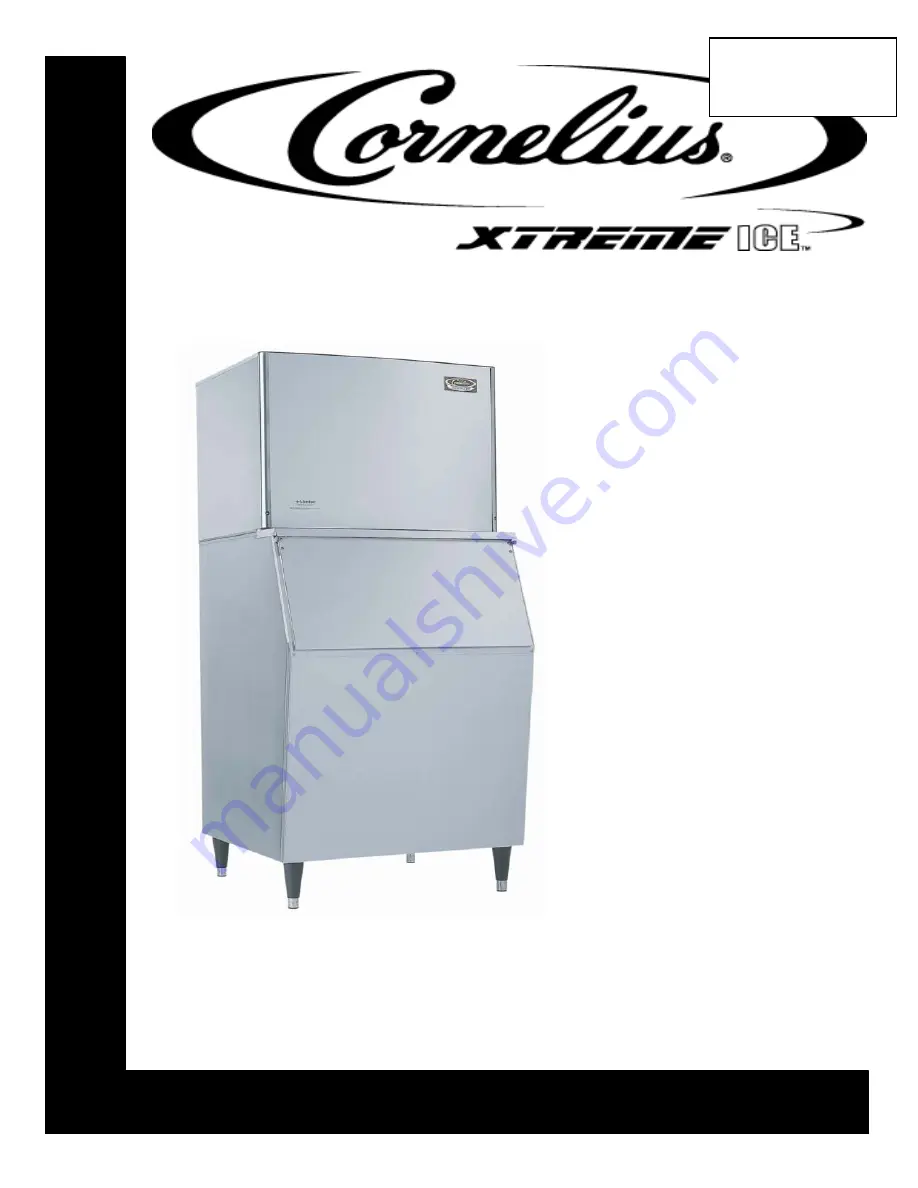
Service / Training Manual
Revision Date: October 17, 2005
Release Date: November 26, 2001
Publication Number: TP00952
Revision: F
www.cornelius.com
Distributed By:
Commercial Refrigeration Service, Inc.
WWW.CorneliusParts.COM
WWW.IceCubes.NET
(866) 423-6253
(623) 869-8881
for model numbers
beginning with
XAC, XWC, or XRC