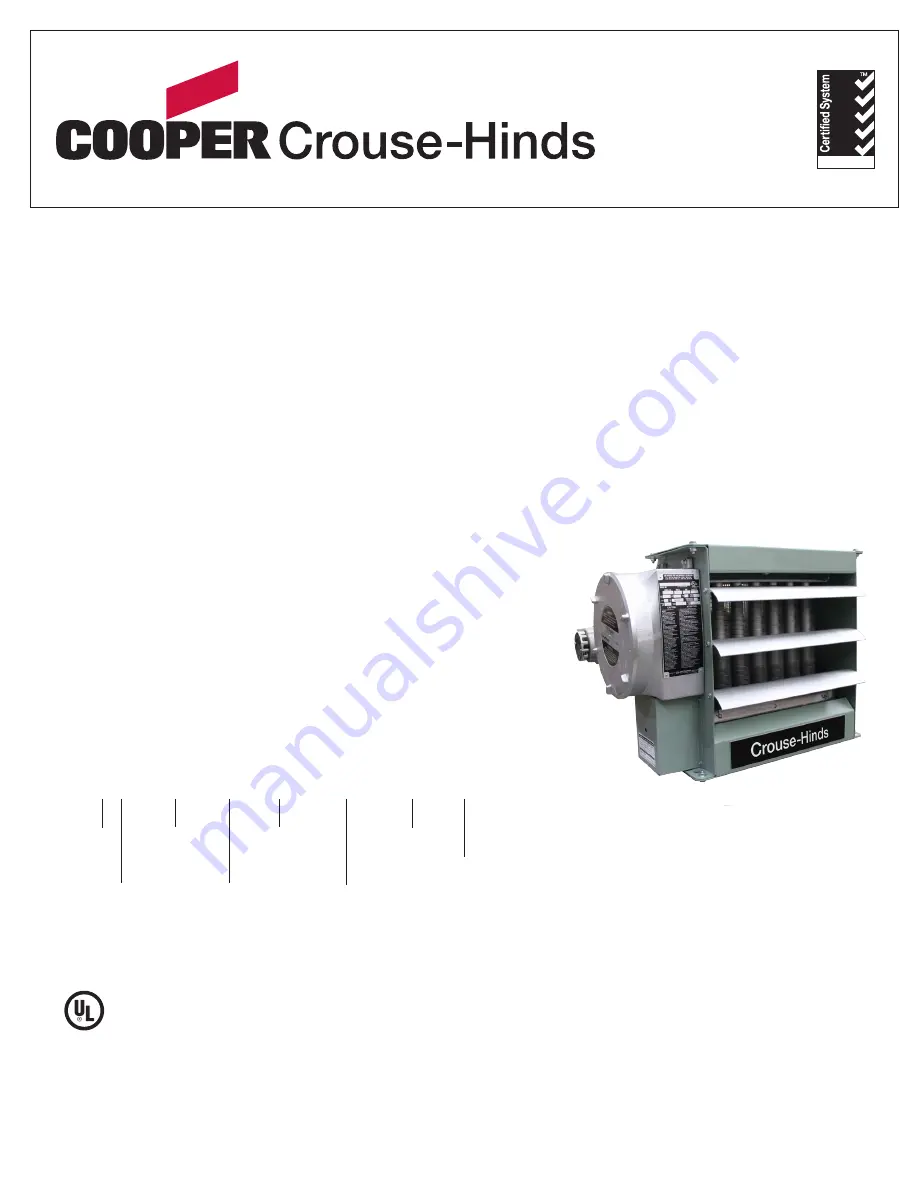
WARNING!
Read all important information notices on pages 3–5
ISO 9001
Part No. 115
92
.Rev.
3
.00 Issued June 2017 Printed in Canada
EXH5 Series
Installation, Parts, Service, and Maintenance Manual
approved Locations
The Electric Forced Air Heaters are cULus listed certified for the following locations:
Class I, Divisions 1 & 2, Groups C & D; Class II, Division 1, Groups E, F & G; Class II,
Division 2, Groups F & G; Class I, Zones 1 & 2, Groups IIA & IIB; Temperature Code
T3B 329˚F (165˚C)
For details of hazardous locations with potential for explosion, refer to the Canadian
Electrical Code, Part 1, Section 18 or National Electrical Code articles 500–516.
C
US
Listed
FX5 ‑ 480 3 60 ‑ 350 ‑ W ‑ T
Model
Series
5th Generation
Heater Voltage
208V, 240V,
480V, 600V
Phase
1, 3
Hertz
50, 60
Heater Kilowatts
Welded Core
T – XT-311 Thermostat with slim
junction box
XT-411 Thermostat with large
junction box
D – Built-in disconnect
P – Built-in pilot light
S – 3-way switch
Model Coding
H – Unit with high “off” de-energized
ambient temperatures
C – Heresite
®
coating
A – Stainless steel cabinet
U – Continuous fan
B – Low ambient option -58°F (-50°C)
L – Large junction box
EXH5
60
60 Hz Models only