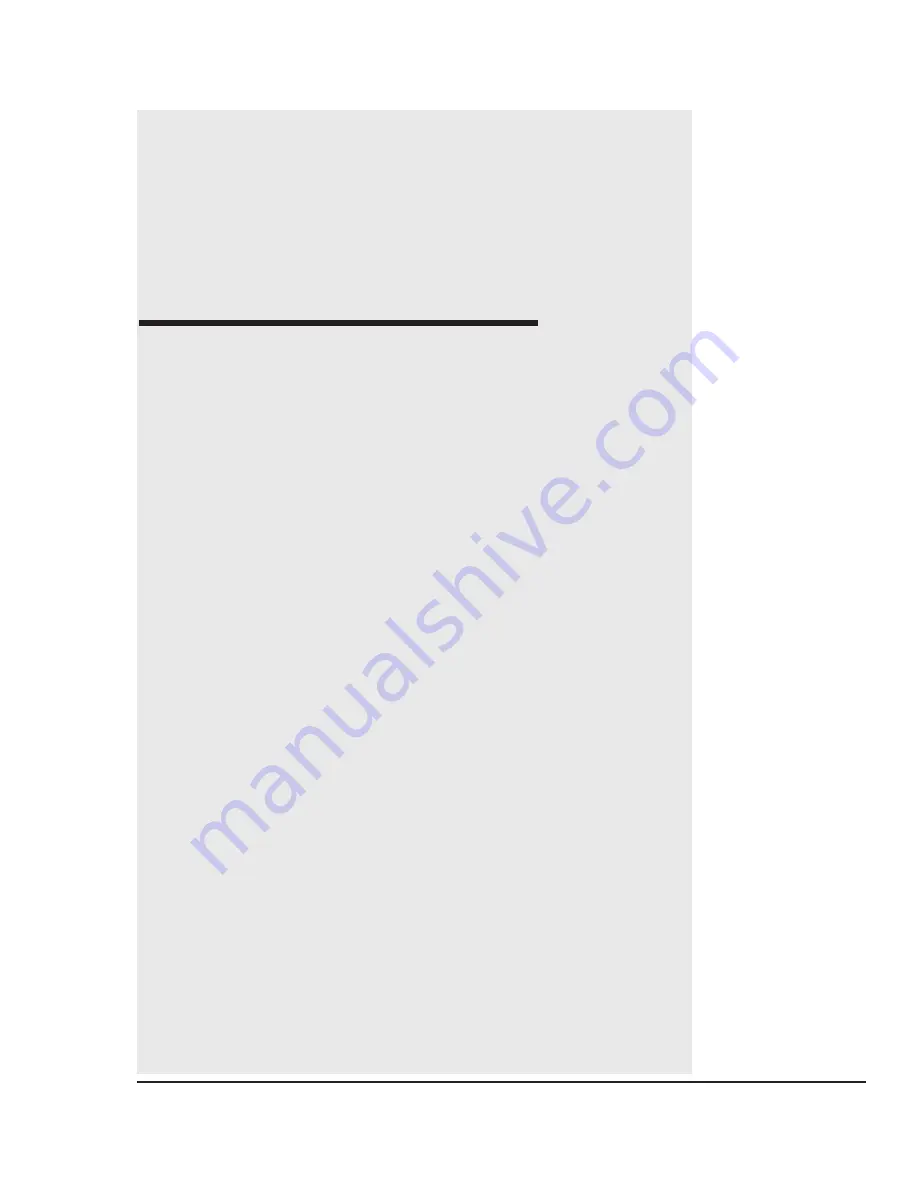
1-1
UGH015/0100
Thermolator TW-1 and TW-2
Purpose of the User Guide . . . .1-2
How the guide is organized . . . .1-2
Your responsibilities as a user .1-2
no one gets hurt . . . . . . . . . . .1-3
I
NTRODUCTION
Summary of Contents for Thermolater vacuTrac
Page 9: ...Figure 1...
Page 12: ......
Page 15: ......
Page 16: ......
Page 50: ......
Page 62: ......
Page 100: ......
Page 106: ......
Page 117: ...UGH015 0100 TW 1 230 460V WIRING DIAGRAM PD 5...
Page 119: ...UGH015 0100 TW 2 230 460V WIRING DIAGRAM PD 7 2...