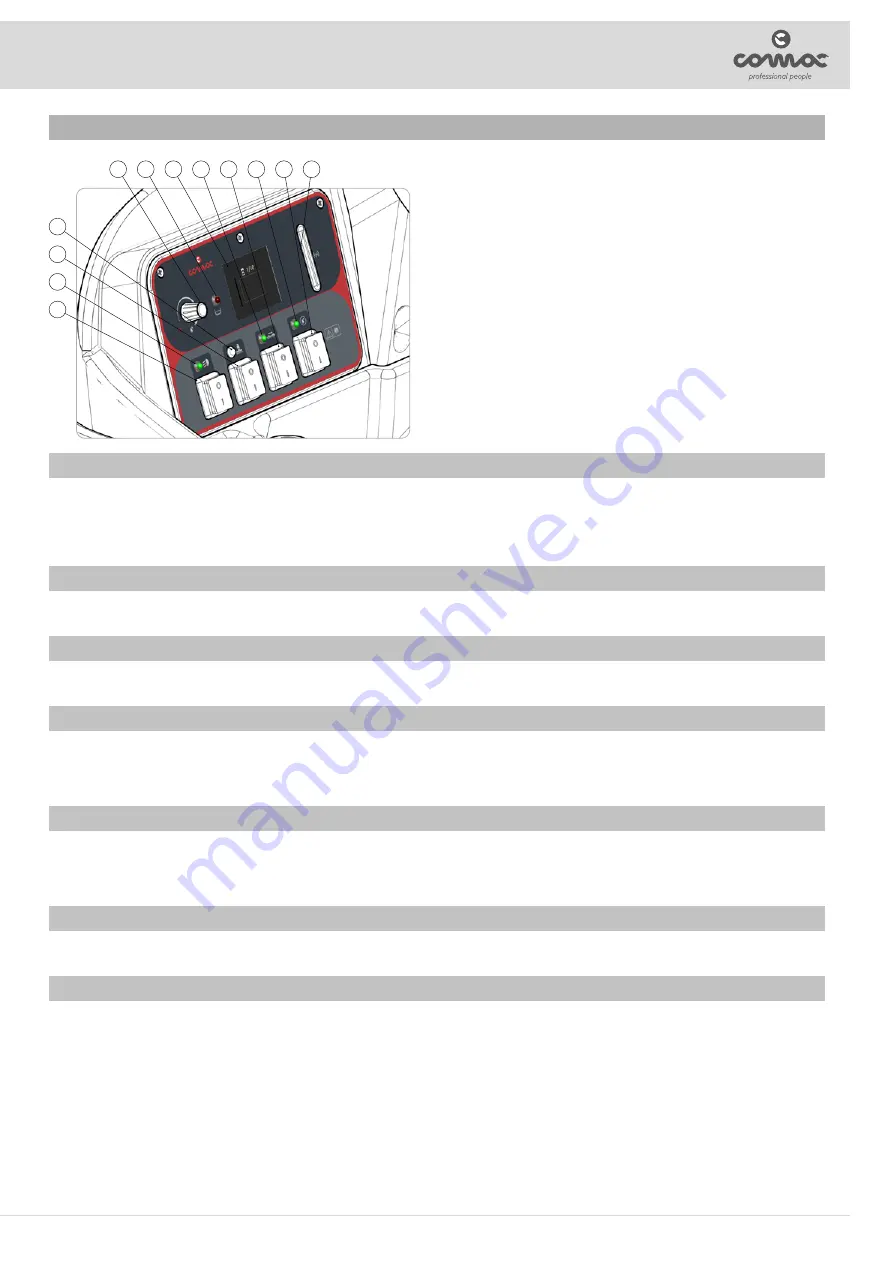
ESSENTIAL VERSION CONTROL PANEL COMPONENTS
The control panel components on the Essential version are as follows:
1.
Detergent solution flow adjustment knob.
2. Red indicator light signalling detergent solution level low.
3. Control display.
4. Green indicator light signalling activation of brush head body lateral
movement.
5. Command switch for brush head body lateral movement.
6. Green indicator light signalling activation of recycling system
7. Recycling system command switch.
8.
Badge slot (valid for versions with automatic fleet management
system).
9. Working headlights command switch.
10. Green indicator light signalling activation of working headlights.
11. Command switch for activation of brush head body extra pressure
function.
12. Green indicator light signalling activation of brush head body extra
pressure function.
1
9
11
10
12
2
3
4
6
5
7
8
PURPOSE AND CONTENT OF THE MANUAL
The aim of this manual is to provide customers with all the information needed to use the machine in the safest, most appropriate and most
autonomous way. This includes information concerning technical aspects, safety, operation, downtime, maintenance, spare parts and scrapping.
The operators and qualified technicians must carefully read the instructions in this manual before carrying out any operations on the machine. If in
doubt about the correct interpretation of instructions, contact your nearest Customer Service Centre to obtain the necessary clarifications.
TARGET GROUP
This manual is written both for operators and for qualified machine maintenance technicians. Operators must not perform operations that should
be carried out by qualified technicians. The manufacturer is not liable for damages resulting from failure to comply with this veto.
STORING THE USE AND MAINTENANCE MANUAL
The Use and Maintenance Manual must be stored in its special pouch close to the machine, protected from liquids and anything else that could
compromise its legibility.
ON CONSIGNMENT OF THE MACHINE
When the machine is consigned to the customer, an immediate check must be performed to ensure all the material mentioned in the shipping
documents has been received, and also to check the machine has not suffered damage during transportation. If this is the case, the carrier must
ascertain the extent of the damage at once, informing our customer service office. It is only by prompt action of this type that the missing material
can be obtained, and compensation for damage successfully claimed.
INTRODUCTORY COMMENT
Any floor scrubbing machine can only work properly and effectively if used correctly and kept in full working order by performing the maintenance
operations described in the attached documentation. We therefore suggest you read this instruction booklet carefully and read it again whenever
difficulties arise while using the machine. If necessary, remember that our assistance service (organised in collaboration with our dealers) is
always available for advice or direct intervention.
IDENTIFICATION DATA
For technical assistance or to request replacement parts, always give the model, the version and the serial number (written on the relevant plate).
TECHNICAL DESCRIPTION
The
C85 2018 BS NSC
is a floor scrubbing machine that can handle a wide variety of floors and types of dirt with the mechanical action of two
cylindrical brushes and the chemical action of a water-detergent solution. As it advances, it collects the dirt removed and the detergent solution not
absorbed by the floor.
The machine must only be used for this purpose
.
7