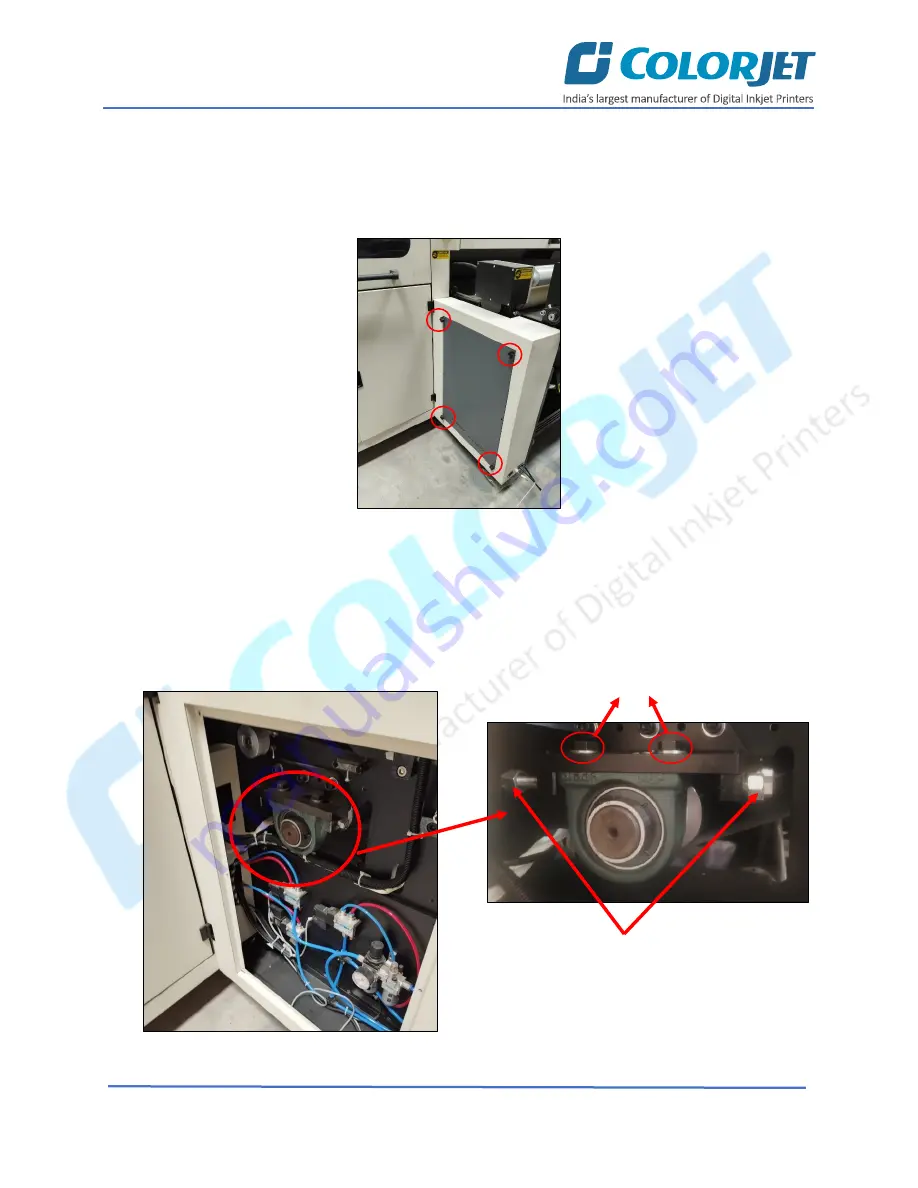
Page
62
of
73
VastraJet K2
BELT SHIFTING PROCED URE
Follow these steps to control belt shifting:
Step 1:
Remove all the selected knobs to open the side cover available on the left side from the back of the machine,
as shown below:
Fig 80: Removing the Side Cover
Step 2:
Loose both the screws available on the top of the belt adjustment handle.
Note:
While performing the belt shifting control process, user needs patience and carefully observe the shifting.
Step 3:
Tight or loose the belt adjustment side screws to adjust the belt shifting as per requirements, as shown
below:
Fig 81: Displaying the Belt Shifting Control Screw
Step 1
Step 2