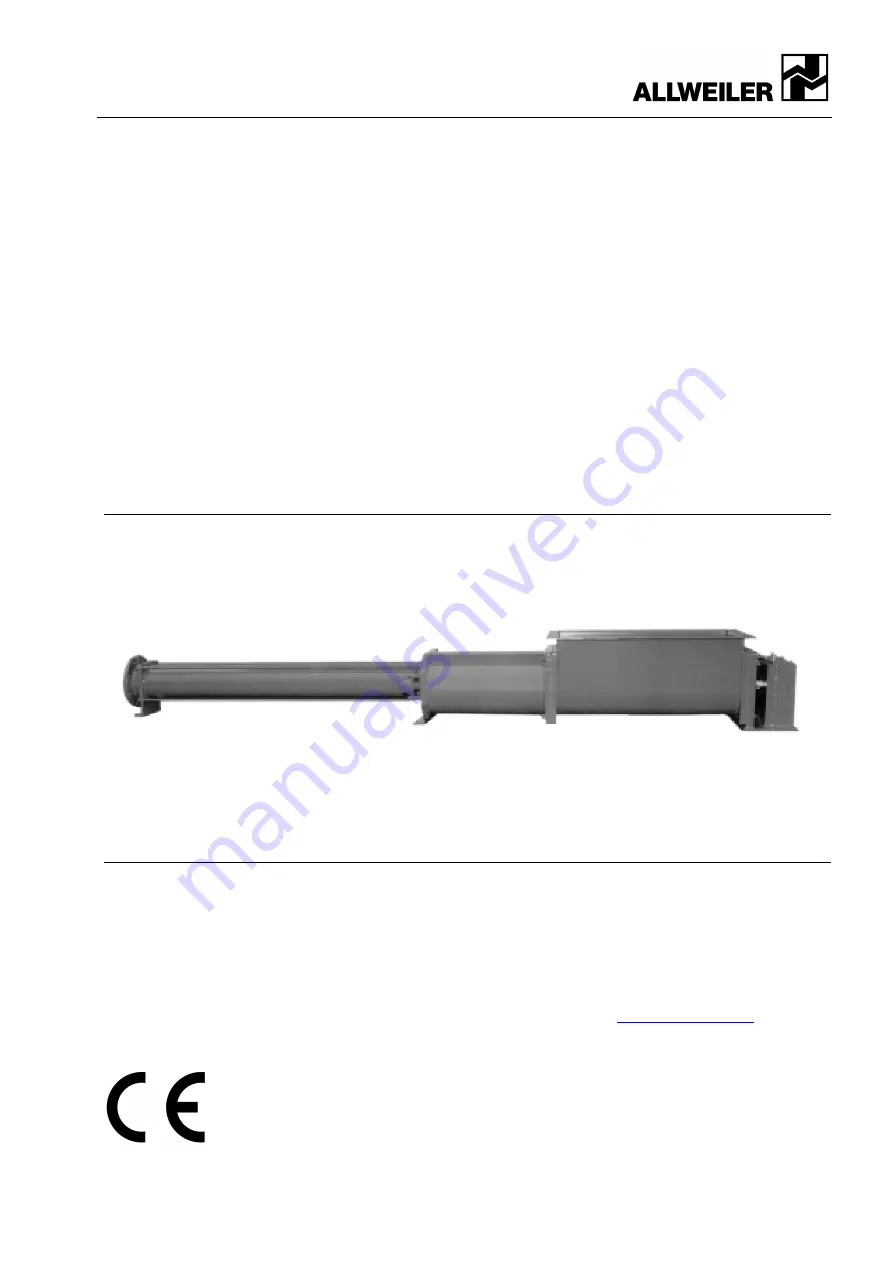
Progressing cavity pump
Operating and maintenance instructions
Series AE.N
with instructions for assembly and
disassembly
Construction Type RG
Retain the operating instructions for future use!
This is a translation of the original operating instruction.
Refer to the order-specific section of the documentation for operational data, dimensions and other additional
information.
Order No.:
Pump ID No.:
Machine No.:
Pump model:
Edition
BA-2011.04
ALLWEILER AG – Bottrop plant
Print No.
151 999
P.O. Box 200123
·
46223 Bottrop
VM-No.
760.0003 GB
Kirchhellener Ring 77-79
·
46244 Bottrop
Germany
Telephone: +49 (0) 2045-966-60
Fax:
+49 (0) 2045 966-679
E-mail:
Internet:
www.allweiler.com
Subject to technical changes!
Important note:
These operating instructions are supplemented with order-specific information.