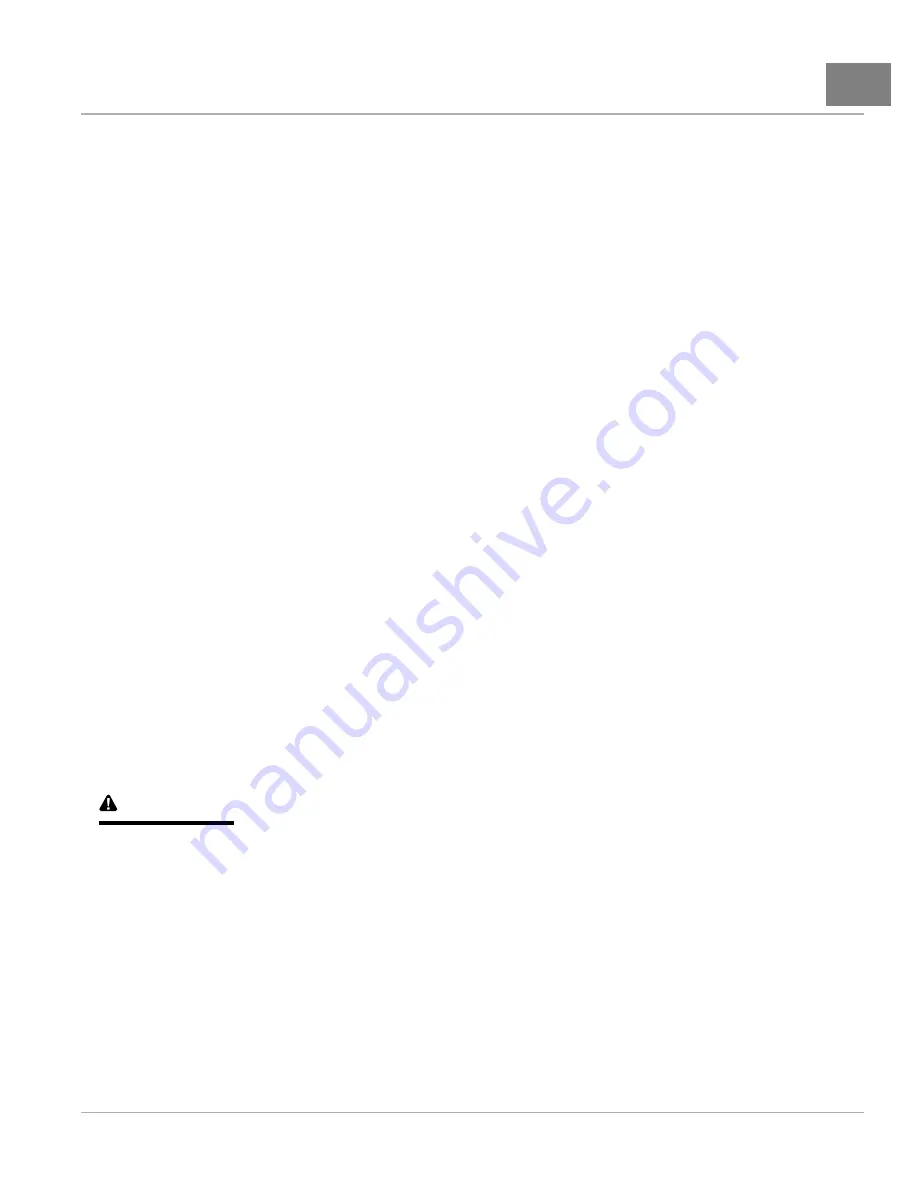
BATTERY CHARGER: FOR ERIC CHARGING
SYSTEM
Onboard Charger Repairs
31
5.
Disconnect DC charging harness (6) from onboard charger DC cord (7).
6.
Disconnect 14-pin plug (8) from onboard charger (4).
7.
Remove two torx screws (9) securing DC cord connector (7) to seat bottom (2). Retain insulator (10).
8.
Remove two torx screws (11) securing charger shield (12) to onboard charger (4).
9.
Remove four bolts (13) securing onboard charger (4) to seat bottom (2).
ONBOARD CHARGER INSTALLATION
1.
Using existing mounting holes, secure onboard charger (4) to seat bottom (2) with four bolts (13)
. Tighten bolts (13) to 53 in·lb (6 N·m).
2.
Secure charger shield (12) to charger with two torx screws (11). Tighten screws (11) to 39.8 in·lb (4.5 N·m).
3.
Using existing mounting holes, secure DC cord connector (7) and insulator (10) to seat bottom (2) with two
screws (9). Tighten screws (9) to 11 in·lb (1.25 N·m).
4.
Connect 14-pin plug (8) to onboard charger (4).
5.
Connect DC charging harness (6) to onboard charger DC cord (7).
6.
Ensure sleeve (5) is in place on charger’s AC socket and connect lead (3) from AC cord reel to onboard
charger (4).
7.
Lower rear-facing seat bottom (2).
8.
Place the Tow/Run switch in the TOW position and connect the batteries.
See Connecting the Batteries –
Electric Vehicles on page 1-4.
TERMINAL BLOCK COVER REMOVAL
1.
Disconnect AC cord from AC outlet.
2.
Disconnect DC cord (1) at connector mounted under seat
.
3.
Push in mounting tabs
to release cover (2) from terminal block (3).
TERMINAL BLOCK COVER INSTALLATION
WARNING
• The terminal block cover (2) on the DC terminal block (3) must be installed properly to comply with UL
code. This cover prevents water exposure and prevents a short across the DC terminals.
1.
Align cover (2) with terminal block (3) and push onto block until tabs lock into place
2014 Precedent
®
Golf Car Maintenance and Service Manual
Page 31-23
Summary of Contents for Precedent 2014
Page 2: ......
Page 4: ......
Page 24: ......
Page 28: ......
Page 38: ......
Page 66: ......
Page 104: ......
Page 116: ......
Page 152: ......
Page 234: ......
Page 252: ......
Page 264: ......
Page 298: ......
Page 332: ......
Page 394: ......
Page 412: ......
Page 438: ......
Page 444: ......
Page 508: ......
Page 534: ......
Page 543: ......
Page 544: ......
Page 545: ......
Page 547: ......
Page 548: ......