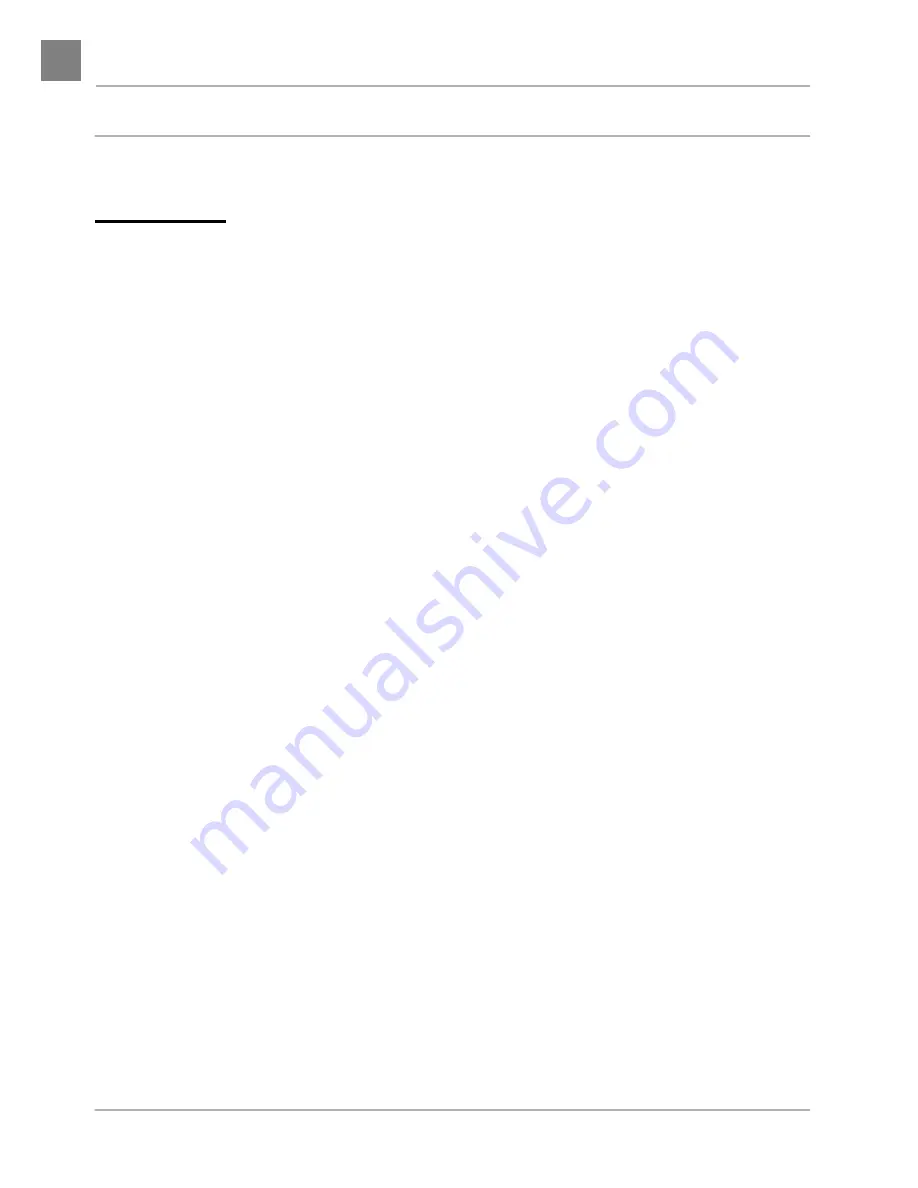
HYDRAULIC AND PARK BRAKE SYSTEMS
Brake Drum Installation
Page 6-14 2001 Pioneer 1200 Gasoline Vehicle Maintenance and Service Manual
6
BRAKE DRUM INSTALLATION
Read WARNING on page 6-1.
∆ WARNING
• If at any point in this procedure the hydraulic system is opened, the brakes must be bled after
the correct reinstallation of the brake components. Failure to bleed the brakes could result in
decreased braking performance due to air being trapped in the hydraulic system. Use only
DOT 5 brake fluid. See Bleeding the Hydraulic Brake System on page 6-29.
• Worn or damaged brake drums cannot be machined. Replace as necessary.
FRONT WHEEL BRAKE DRUM INSTALLATION
NOTE: Prior to installing the brake drum, inspect the brake lines, hoses, drums and brake cluster assem-
blies. See Brake System Inspection on page 6-2.
Clean any residual grease from the friction area of the brake drum prior to installing it.
1. Inspect the wheel bearings for damage or wear. Replace bearings and cups if necessary.
2. Clean the wheel bearings (5), making sure that there is no dirt or debris trapped in the rollers (Figure 6-
NOTE: Do not use compressed air to dry wheel bearings after cleaning.
3. Inspect the bearing cups (7) for wear or damage. If they are worn or pitted, remove the cups by inserting
a drift punch from the opposite end of the hub and tapping lightly around them (Figure 6-2, Page 6-7).
4. If bearing cups (7) were removed, press new cups in squarely against the shoulder in the hub (Figure
NOTE: Always install new cups (7) when new bearings (5) are installed (Figure 6-2, Page 6-7).
5. Inspect the surface of the spindle shaft where the seal (6) seats. It should be clean and smooth (Figure
6. Pack the wheel bearings (5) and lubricate the bearing cups (7) with Chassis Lube (EP NLGI Grade 2).
Make sure the grease is forced between the rollers (Figure 6-2, Page 6-7).
7. Install a new seal (6) and wheel bearing (5) into rear of hub (Figure 6-2, Page 6-7).
8. Lubricate spindle shaft with grease.
9. Carefully apply grease around seal (6) inner lip before installation. Do not allow grease to touch the
brake shoe linings or the brake shoe surface of the drum/hub.
10. Place the drum/hub (14) onto the spindle and brake cluster (Figure 6-1, Page 6-2). See following
NOTE.
NOTE: If drum installation is difficult:
The brake shoes may need to be adjusted vertically in the mounting slots.
Rotation of the brake shoe adjusters may be necessary to create additional clearance between the
brake shoes and the brake drum (Figure 6-3, Page 6-8). Use a hydraulic brake adjuster (CCI
102169401) to gently rotate the adjusters.
11. Fill cavity with grease.