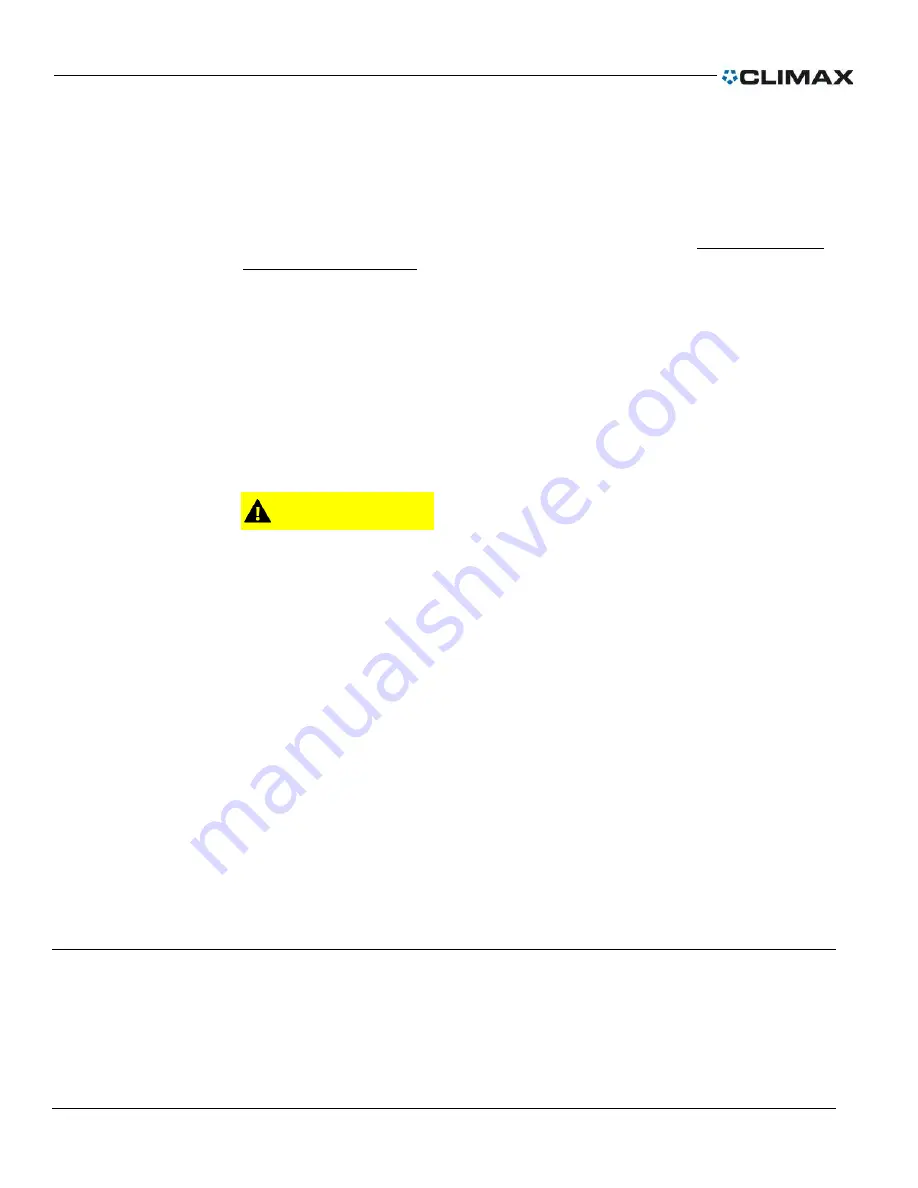
P/N: 57017, Rev. 3
Page 23
8.
Center the bar by evenly adjusting the jacking screws then tighten the hex-head
cap screws.
9.
Slide the bar and bearing support into the work piece.
10.
Using a dial indicator and the jacking screws, center the bar inside the work
piece. Tighten the jacking screw against the inside of the bore. Do not exceed 22
ft-lbs (30 Nm) of torque.
11.
If mounting the RDU between the bearing supports, do so now. See Section 3.6
on page 24 for instructions.
12.
If mounting another ID-mount bearing, repeat the above steps.
3.4.1
If mounting an end-mount bearing
Do the following to set up an end-mount bearing support assembly:
1.
Re-check the bar for center by sweeping a dial indicator inside the bore.
2.
Adjust the jacking screws, if necessary.
CAUTION
Bearings placed too far apart allow the bar to deform, reducing
bore precision. To keep the bar from deflecting, do not space the
bearing supports more than 5 feet (1.5 m) apart.
3.4.2
Clamping the bearing assembly to the bar
Do the following to clamp the bearing assembly to the bar:
1.
Remove the screws holding the lock plate.
2.
Slide the lock plate away from the lock nut.
3.
Rotate the lock nut using both hands until it is snug. This is the zero reference
point.
4.
Mark or note the angular position of the lock nut.
5.
Use the offset spanner wrench in the tool kit to rotate the lock nut approximately
1.25
—
1.5 additional turns.
6.
Reapply the lock plate. If necessary, additionally tighten the lock nut until a slot
in the lock plate is aligned with the retaining screw holes.
7.
Reinstall the retaining screws.
3.5
Preload bearing kit
The preload bearing kit is only used on bearing assemblies using the bearing
cartridge P/N 23570. It is appropriate in those applications demanding greater
machine stability, especially facing operations. The kit contains a pair of 3.5" (89
mm) hinged clamp collars, one standard and the other with tensioning screws. This
kit can be used in either the vertical or horizontal positions.
Summary of Contents for BB6100
Page 1: ...PN 57017 May 2019 Revision 3 BB6100 BORING BAR OPERATING MANUAL ORIGINAL INSTRUCTIONS ...
Page 2: ......
Page 4: ...Page B BB6100 Operating Manual CLIMAX WORLDWIDE LOCATIONS ...
Page 15: ...P N 57017 Rev 3 Page 9 2 3 Specifications and Dimensions ...
Page 16: ...Page 10 BB6100 Operating Manual ...
Page 17: ...P N 57017 Rev 3 Page 11 ...
Page 18: ...Page 12 BB6100 Operating Manual ...
Page 19: ...P N 57017 Rev 3 Page 13 ...
Page 20: ...Page 14 BB6100 Operating Manual 2 4 Axial Feed Assembly ...
Page 43: ...P N 57017 Rev 3 Page 37 ...
Page 50: ...Page 44 BB6100 Operating Manual This page is intentionally left blank ...
Page 64: ...Page 58 BB6100 Operating Manual FIGURE 13 ID MOUNT BEARING ASSEMBLY P N 54355 ...
Page 65: ...P N 57017 Rev 3 Page 59 FIGURE 14 SPIDER BEARING ASSEMBLY END SUPPORT P N 53710 ...
Page 67: ...P N 57017 Rev 3 Page 61 FIGURE 16 4 ARM END MOUNT BEARING ASSEMBLY P N 22091 ...
Page 68: ...Page 62 BB6100 Operating Manual FIGURE 17 BORING BAR CHART ASSEMBLY P N 71618 ...
Page 69: ...P N 57017 Rev 3 Page 63 FIGURE 18 BORING BAR CHART ASSEMBLY PARTS LIST P N 71618 ...
Page 70: ...Page 64 BB6100 Operating Manual FIGURE 19 MECHANICAL AXIAL FEED UNIT ASSEMBLY P N 23299 ...
Page 71: ...P N 57017 Rev 3 Page 65 FIGURE 20 MECHANICAL AXIAL FEED UNIT ASSEMBLY PARTS LIST P N 23299 ...
Page 72: ...Page 66 BB6100 Operating Manual FIGURE 21 ELECTRIC AXIAL FEED ASSEMBLY P N 41062 ...
Page 73: ...P N 57017 Rev 3 Page 67 FIGURE 22 ELECTRIC AXIAL FEED ASSEMBLY PARTS LIST P N 41062 ...
Page 74: ...Page 68 BB6100 Operating Manual FIGURE 23 ELECTRIC AXIAL FEED ASSEMBLY P N 86681 ...
Page 75: ...P N 57017 Rev 3 Page 69 FIGURE 24 MECHANICAL FEED ASSEMBLY FOR ELECTRIC AXIAL FEED P N 41064 ...
Page 77: ...P N 57017 Rev 3 Page 71 FIGURE 26 ROTATIONAL DRIVE ASSEMBLY P N 22221 ...
Page 78: ...Page 72 BB6100 Operating Manual FIGURE 27 ROTATIONAL DRIVE ASSEMBLY PARTS LIST P N 22221 ...
Page 79: ...P N 57017 Rev 3 Page 73 FIGURE 28 FACING HEAD CHART ASSEMBLY P N 75682 ...
Page 80: ...Page 74 BB6100 Operating Manual FIGURE 29 FACING HEAD CHART ASSEMBLY PARTS LIST P N 75682 ...
Page 81: ...P N 57017 Rev 3 Page 75 FIGURE 30 BORING FACING SLIDE ARM SET ASSEMBLY P N 81561 ...
Page 83: ...P N 57017 Rev 3 Page 77 FIGURE 32 BORING FACING TOOL ARM CHART ASSEMBLY P N 86638 ...
Page 85: ...P N 57017 Rev 3 Page 79 FIGURE 34 TOOL CARRIER ASSEMBLY P N 54224 ...
Page 86: ...Page 80 BB6100 Operating Manual FIGURE 35 ADJUSTABLE AXIAL NUT LEAD SCREW ASSEMBLY P N 54223 ...
Page 87: ...P N 57017 Rev 3 Page 81 FIGURE 36 BORING HEAD SOLID TOOLING P N 81246 ...
Page 89: ...P N 57017 Rev 3 Page 83 FIGURE 38 MICRO ADJUST BORING HEAD ASSEMBLY P N 79325 ...
Page 91: ...P N 57017 Rev 3 Page 85 FIGURE 40 BORING DIAMETER RANGE STACK UP BLOCKS ASSEMBLY P N 81249 ...
Page 93: ...P N 57017 Rev 3 Page 87 FIGURE 42 TOOL CARRIER ASSEMBLY P N 22377 ...
Page 94: ...Page 88 BB6100 Operating Manual FIGURE 43 TORQUE ARM ASSEMBLY P N 22604 ...
Page 95: ...P N 57017 Rev 3 Page 89 FIGURE 44 SCREW ASSEMBLY P N 55564 ...
Page 97: ...P N 57017 Rev 3 Page 91 8 SCHEMATICS ...
Page 98: ...Page 92 BB6100 Operating Manual This page intentionally left blank ...
Page 99: ...P N 57017 Rev 3 Page 93 FIGURE 45 ELECTRIC FEED CONTROLLER ASSEMBLY P N 42368 ...
Page 100: ...Page 94 BB6100 Operating Manual This page intentionally left blank ...
Page 101: ...P N 57017 Rev 3 Page 95 9 SDS ...
Page 102: ...Page 96 BB6100 Operating Manual ...
Page 103: ...P N 57017 Rev 3 Page 97 ...
Page 104: ...Page 98 BB6100 Operating Manual ...
Page 105: ...P N 57017 Rev 3 Page 99 ...
Page 106: ...Page 100 BB6100 Operating Manual ...
Page 107: ...P N 57017 Rev 3 Page 101 ...
Page 108: ...Page 102 BB6100 Operating Manual ...
Page 109: ...P N 57017 Rev 3 Page 103 ...
Page 110: ...Page 104 BB6100 Operating Manual ...
Page 111: ...P N 57017 Rev 3 Page 105 ...
Page 112: ...Page 106 BB6100 Operating Manual ...
Page 113: ...P N 57017 Rev 3 Page 107 ...
Page 114: ...Page 108 BB6100 Operating Manual ...
Page 115: ...P N 57017 Rev 3 Page 109 ...
Page 116: ...Page 110 BB6100 Operating Manual ...
Page 117: ...P N 57017 Rev 3 Page 111 ...
Page 118: ...Page 112 BB6100 Operating Manual ...
Page 119: ...P N 57017 Rev 3 Page 113 ...
Page 120: ...Page 114 BB6100 Operating Manual ...
Page 121: ...P N 57017 Rev 3 Page 115 ...
Page 122: ...Page 116 BB6100 Operating Manual ...
Page 123: ...P N 57017 Rev 3 Page 117 ...
Page 124: ...Page 118 BB6100 Operating Manual ...
Page 125: ...P N 57017 Rev 3 Page 119 ...
Page 126: ...Page 120 BB6100 Operating Manual ...
Page 127: ...P N 57017 Rev 3 Page 121 ...
Page 128: ...Page 122 BB6100 Operating Manual ...
Page 129: ...P N 57017 Rev 3 Page 123 ...
Page 130: ...Page 124 BB6100 Operating Manual ...
Page 131: ...P N 57017 Rev 3 Page 125 ...
Page 132: ...Page 126 BB6100 Operating Manual ...
Page 133: ...P N 57017 Rev 3 Page 127 ...
Page 134: ...Page 128 BB6100 Operating Manual ...
Page 135: ......
Page 136: ......