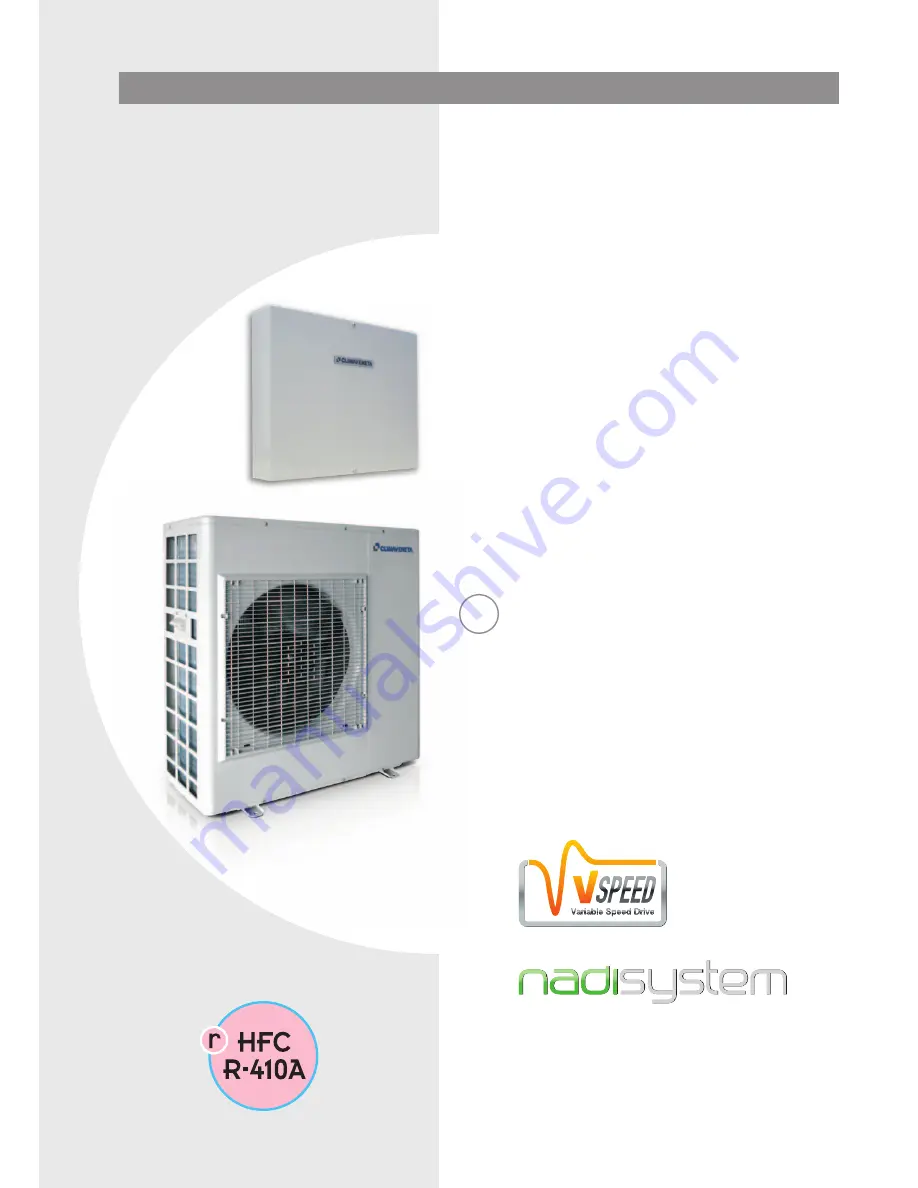
INSTALLATION - USER - MAINTENANCE MANUAL
i-KI MTD air/water heat pump, heating
only, with DC inverter-driven
compressors, domestic hot water
production, axial-flow fans and hydronic
unit for outdoor installation
i-KIR MTD reverse-cycle air/water heat
pump with DC inverter-driven
compressors, domestic hot water
production, axial-flow fans and hydronic
unit for outdoor installation
EN
i-KI MTD / i-EM2
i-KIR MTD / i-EMR2
0011m ÷ 0061m
Summary of Contents for i-EM2
Page 69: ......