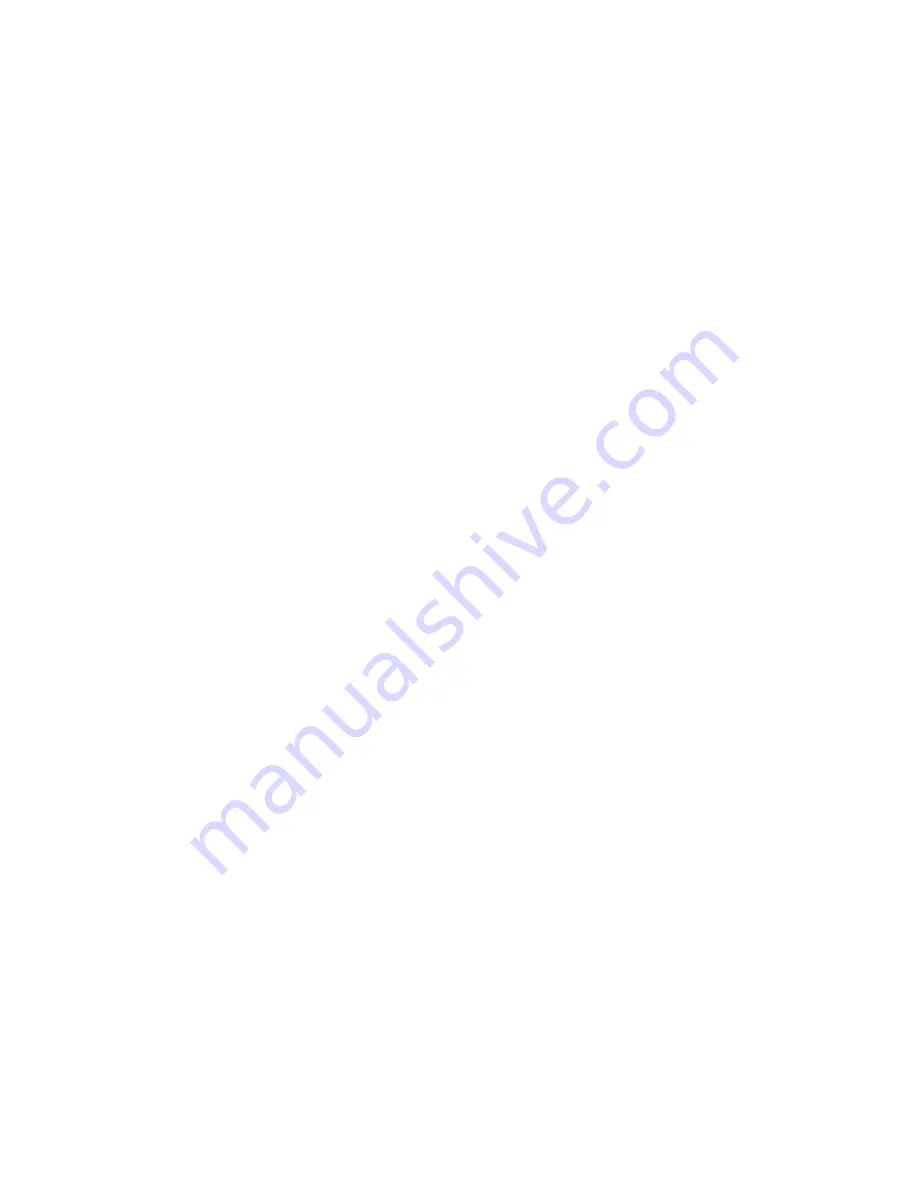
Chapter 2
Profire V Burner
2-26
750-177
Safety shutdown caused by ignition or flame failure will actuate a red indicator light and energize an audible
alarm (if so equipped). If the programmer has a non-recycling interlock circuit, any interruption in this circuit
during the pre-purge or firing cycle will cause a safety shutdown. This type of shutdown requires manual reset
of the programming control and must be corrected before operation can be resumed.
G. Adjustments
While each burner is tested at the factory for correct operation before shipment, variable conditions such as
burning characteristics of the fuel used and operating load conditions may require further adjustment after
installation to assure maximum operating efficiency.
Prior to placing the boiler into initial service, a complete inspection should be made of all controls, connecting
piping, wiring, and all fastenings such as nuts, bolts, and setscrews to be sure that no damage or
misadjustments occurred during shipment and installation.
A combustion efficiency analysis made during the initial startup will help to determine what additional
adjustments are required in a particular installation.
COMBUSTION ADJUSTMENT ON OIL AND GAS
Flame appearance alone is not sufficient to judge combustion efficiency, although it may help in making
preliminary settings.
The proper settings of air-fuel ratios must be determined by flue gas analysis. Combustion gas analysis
indicates the air to fuel ratio and the degree of complete combustion. Instruments are available to measure
carbon dioxide (CO
2
), oxygen (O
2
), and carbon monoxide (CO). At no time should CO
2
measurements alone
be used to indicate proper excess air levels. Only O
2
measurement can definitively show whether sufficient air
has been provided for combustion.
STACK TEMPERATURE
Net stack temperature is obtained by subtracting the ambient temperature from the flue gas temperature. A
high net stack temperature indicates wasted heat. Stack temperature should be as low as possible without
causing flue gas condensation.
Stack heat loss can be reduced by decreasing either the temperature or the volume of the flue gas, or both.
Flue gas temperature is reduced by improving heat transfer or by reducing excess combustion air. A certain
amount of excess air is necessary to complete combustion. More efficient burners require minimum excess air.
SMOKE MEASUREMENT
Smoke measurements can be made using a variety of different methods. The standards will vary somewhat
according to the equipment used, and instructions accompanying the instrument should be followed.
Smoky combustion can result from:
• improper air delivery
• insufficient draft
• improper fuel viscosity
• improper fuel-air ratio
• excessive air leaks in the combustion chamber
• improper fuel oil temperature
Summary of Contents for FLX 1000
Page 12: ...Chapter 1 General Description 1 6 750 177...
Page 68: ...Chapter 2 Profire V Burner 2 56 750 177...
Page 90: ...Chapter 4 Sequence of Operation 4 10 750 177...
Page 104: ...Chapter 5 Adjustment Procedures 5 14 750 177...
Page 110: ...Chapter 6 Troubleshooting 6 6 750 177...
Page 122: ...8 2 750 177 Figure 8 1 Typical Hot Water Flextube Casing...
Page 124: ...8 4 750 177 Figure 8 2 Typical Low Pressure Steam Flextube Casing...
Page 126: ...8 6 750 177 Figure 8 3 Typical High Pressure Steam Flextube Casing...
Page 128: ...Parts Chapter 8 8 8 750 177 Steam Pressure Controls...
Page 129: ...Chapter 8 Parts 750 177 8 9 Water Level Controls...
Page 130: ...Parts Chapter 8 8 10 750 177 Water Level Controls continued...
Page 131: ...Chapter 8 Parts 750 177 8 11 Water Column Main and Aux 15 Steam...
Page 132: ...Parts Chapter 8 8 12 750 177 Water Column Main and Aux 150 Steam...
Page 133: ...Chapter 8 Parts 750 177 8 13 Safety Valves...
Page 134: ...Parts Chapter 8 8 14 750 177...
Page 135: ......
Page 136: ...e mail info cleaverbrooks com Web Address http www cleaverbrooks com...