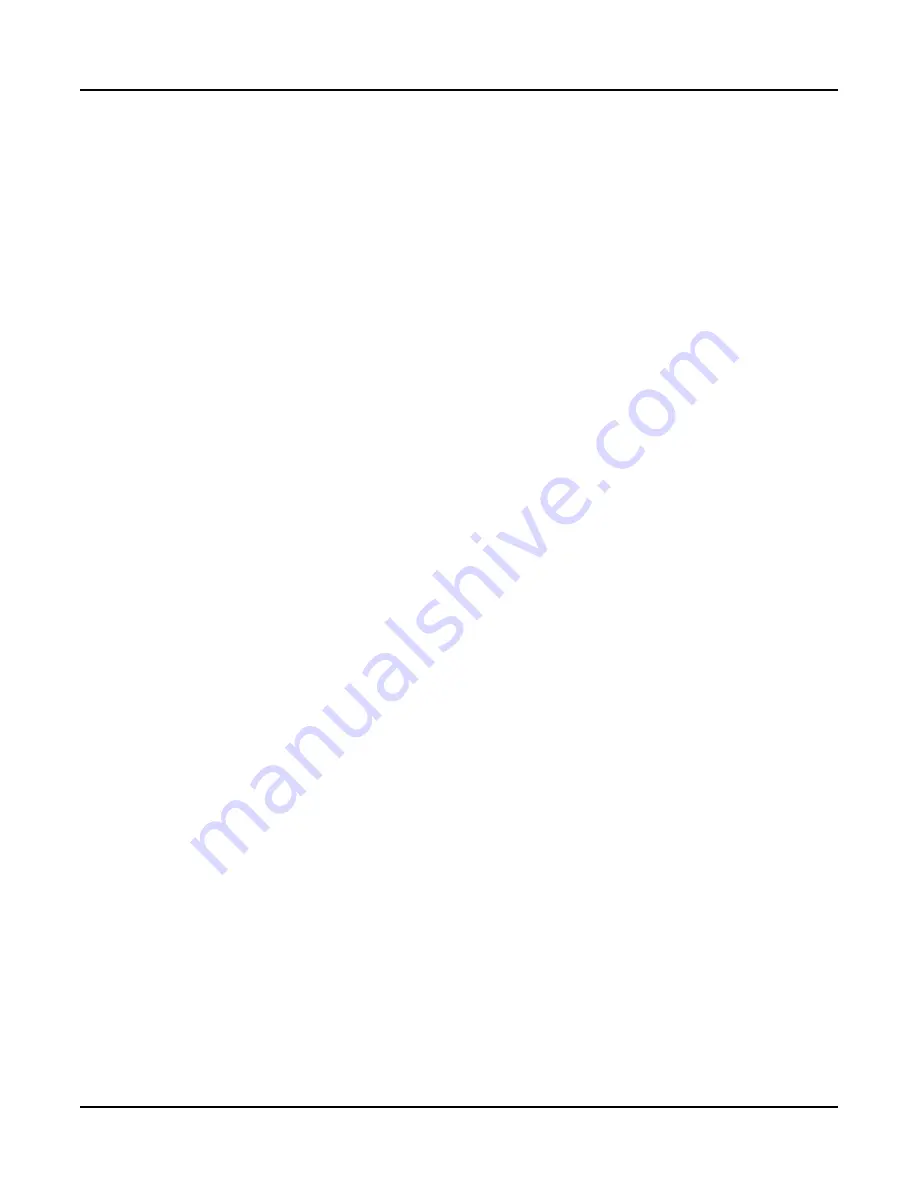
Chapter 5 — Starting and Operating Instructions
Part No. 750-184
5-9
150 SSU. The actual temperature of the oil at the burner
should be determined by flame appearance and good
combustion based on a stack analysis.
Close the manual by-pass valve after the temperature rise on the
fuel oil controller thermometer is noted. Be certain that hot oil is
moving through the controller. The orifice gate valve must also be
closed. If the temperature drops, open the orifice gate valve until a
rise is noted, then close it.
Once the correct setting of the heater thermostats has been
established, set the low oil temperature switch at the point
approximately 30
°
F lower than the normal burning temperature. If
the system is equipped with a high oil temperature switch, it should
be set to open at 20 -30
°
F higher than normal burning temperature.
Note: The maximum oil temperature allowed in the system is
250°F.
Starting
- When all the conditions covered above and in Sections A,
B, C and D are assured, the burner is ready for firing.
G. FIRING PREPARATIONS FOR GAS (SERIES 200-
400-700)
• Prior to initial starting, check the linkage attached to the gas
butterfly valve to assure that movement is free from binding.
• Verify the presence and availability of gas. On a new installation,
representatives of the gas utility should be present when gas first
flows into the system to supervise purging of the new gas line,
unless they have already done so.
• Determine that the pilot is operating properly, as outlined in
Section C, Chapter 5.
• Determine that sufficient pressure exists at the entrance to the
gas train by installing a test gauge downstream of the regulator.
• The gas pressure regulator must be adjusted to the proper
pressure level. Since the regulator is generally supplied by others,
adjustment should proceed according to instructions supplied by
its manufacturer.
It is necessary for the operator to know the burner requirements in
gas quantity and pressure. The information can generally be found
on the Dimension Diagram (DD) supplied by Cleaver-Brooks for the
specific installation. Should the information not be readily available,
consult the Cleaver-Brooks Service Department giving the boiler
serial number. Chapter 6 contains additional information along with
standard gas flow and pressure requirements.
• If the burner is a combination fuel model, set the gas/oil switch
to “gas.” Withdraw the oil burner gun and latch it in its rearward
position.
• On initial start-up, it is recommended that the main gas shutoff
cock remains closed until the programmer has cycled through
prepurge and pilot sequences. When the
fuel light
on the control
panel comes on, observe the action of the motorized gas valve
stem to determine that it opens when energized. As soon as it is
confirmed, turn the burner switch “OFF” and let programmer
finish its cycle. Check that the gas valve has closed. Again, turn
Summary of Contents for CB Ohio Special 100 HP
Page 2: ...ii ...
Page 8: ...viii ...
Page 42: ...Chapter 2 Burner Operation and Control 2 22 Part No 750 184 ...
Page 116: ...Chapter 6 Adjustment Procedures 6 28 Part No 750 184 ...
Page 126: ...Chapter 8 Inspection and Maintenance 8 6 Part No 750 184 ...
Page 153: ...Chapter 9 Parts Part No 750 184 9 3 Insulated Front Head Model CB LE ...
Page 154: ...Chapter 9 Parts 9 4 Part No 750 184 Insulated Front Head Interior Model CB LE ...
Page 155: ...Chapter 9 Parts Part No 750 184 9 5 Insulated Inner Door Model CB OS ...
Page 156: ...Chapter 9 Parts 9 6 Part No 750 184 Insulated Rear Head CB LE ...
Page 157: ...Chapter 9 Parts Part No 750 184 9 7 Insulated Rear Head CB LE ...
Page 158: ...Chapter 9 Parts 9 8 Part No 750 184 Insulated Rear Head CB OS ...
Page 159: ...Chapter 9 Parts Part No 750 184 9 9 Dry Oven Model CB LE ...
Page 161: ...Chapter 9 Parts Part No 750 184 9 11 Motor Impeller Model CB LE ...
Page 162: ...Chapter 9 Parts 9 12 Part No 750 184 Front Head Linkage ...
Page 170: ...Chapter 9 Parts 9 20 Part No 750 184 Control Cabinet Hawk ICS ...
Page 171: ...Chapter 9 Parts Part No 750 184 9 21 Control Panel Standard ...
Page 172: ...Chapter 9 Parts 9 22 Part No 750 184 Entrance Box ...
Page 173: ...Chapter 9 Parts Part No 750 184 9 23 Front Head Electrical CB LE ...
Page 174: ...Chapter 9 Parts 9 24 Part No 750 184 Front Head Electrical CB LE ...
Page 175: ...Chapter 9 Parts Part No 750 184 9 25 Front Head Electrical CB OS ...
Page 176: ...Chapter 9 Parts 9 26 Part No 750 184 Front Head Electrical CB OS ...
Page 179: ...Chapter 9 Parts Part No 750 184 9 29 Heavy Oil Piping 60 Steam CB LE ...
Page 180: ...Chapter 9 Parts 9 30 Part No 750 184 Heavy Oil Piping 60 Steam CB LE SEE TABLE NEXT PAGE ...
Page 181: ...Chapter 9 Parts Part No 750 184 9 31 Common Oil Parts Heavy Oil ...
Page 182: ...Chapter 9 Parts 9 32 Part No 750 184 Side Mounted Air Compressor Piping ...
Page 183: ...Chapter 9 Parts Part No 750 184 9 33 Air Compressor Piping CB OS ...
Page 185: ...Chapter 9 Parts Part No 750 184 9 35 Light Oil Piping ...
Page 186: ...Chapter 9 Parts 9 36 Part No 750 184 Light Oil Air Piping Front Head ...
Page 187: ...Chapter 9 Parts Part No 750 184 9 37 Light Oil Air Piping Front Head PAGE 9 31 ...
Page 191: ...Chapter 9 Parts Part No 750 184 9 41 Gas Train 125 150 HP ...
Page 193: ...Chapter 9 Parts Part No 750 184 9 43 Gas Train 200 HP ...
Page 195: ...Chapter 9 Parts Part No 750 184 9 45 Steam Pressure Controls ...
Page 196: ...Chapter 9 Parts 9 46 Part No 750 184 Hot Water Temperature Controls ...
Page 197: ...Chapter 9 Parts Part No 750 184 9 47 Water Column ...
Page 198: ...Chapter 9 Parts 9 48 Part No 750 184 Water Column ...
Page 199: ...Chapter 9 Parts Part No 750 184 9 49 Fireside Gaskets CB LE ...
Page 200: ...Chapter 9 Parts 9 50 Part No 750 184 Fireside Gaskets CB OS ...