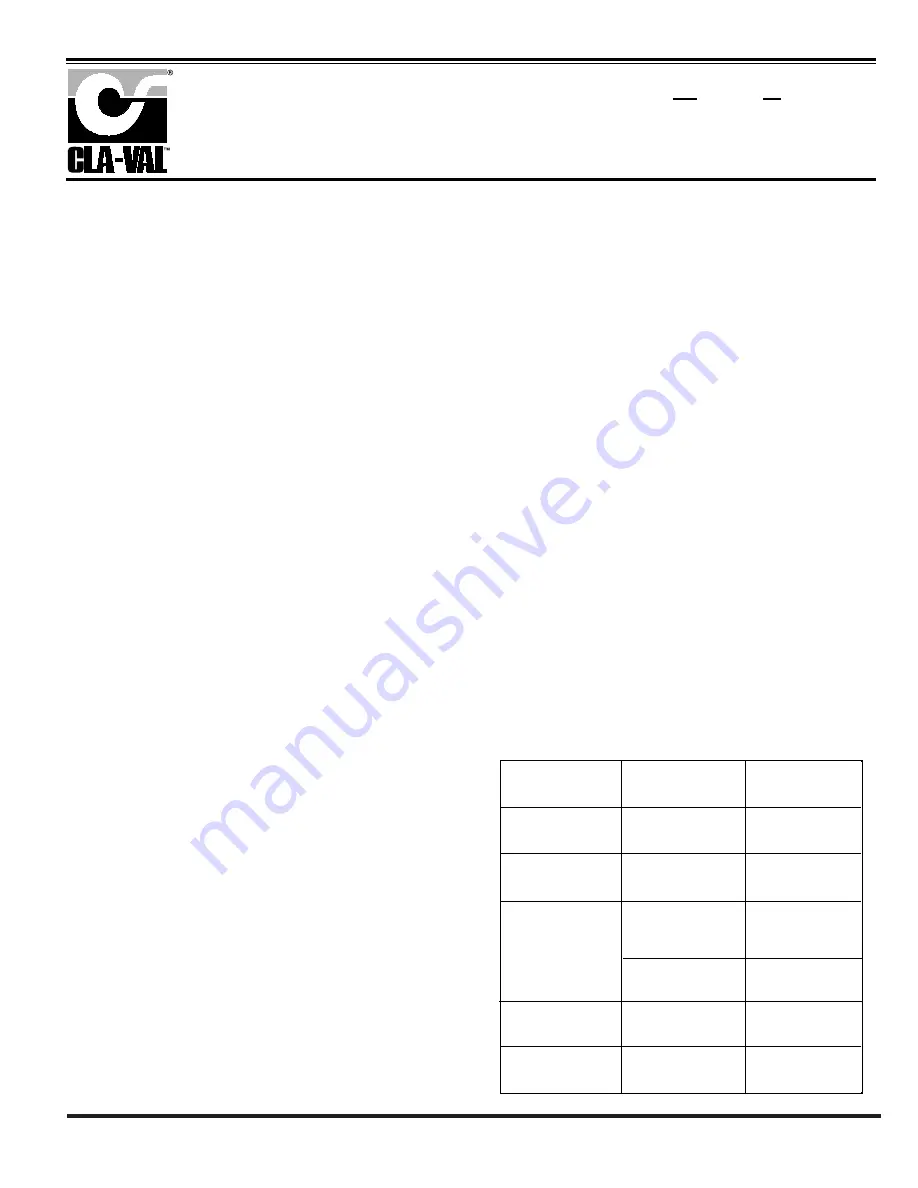
DESCRIPTION
The CRL Pressure Relief Control is a direct acting, spring loaded,
diaphragm type relief valve. It may be used as a self-contained valve or as
a pilot control for a Cla-Val Main valve. It opens and closes within very
close pressure limits.
INSTALLATION
The CRL Pressure Relief Control may be installed in any position. The
control body (7) has one inlet and one outlet port with a side pipe plug (24)
at each port. These plugs are used for control connections or gauge appli-
cations. The inlet in the power unit body (6) is the sensing line port. A flow
arrow is marked on the body casting.
OPERATION
The CRL Pressure Relief Control is normally held closed by the force of the
compression spring above the diaphragm; control pressure is applied
under the diaphragm.
When the controlling pressure exceeds the spring setting, the disc is lifted
off its seat, permitting flow through the control.
When controlling pressure drops below spring setting, the spring returns
the control to its normally closed position.
ADJUSTMENT PROCEDURE
The CRL Pressure Relief Control can be adjusted to provide a relief setting
at any point within the range found on the nameplate.
Pressure adjustment is made by turning the adjustment screw (9) to vary
the spring pressure on the diaphragm. Turning the adjustment screw clock-
wise increases the pressure required to open the valve. Counterclockwise
decreases the pressure required to open the valve.
When pressure adjustments are complete the jam nut (10) should be tight-
ened and the protective cap (1) replaced. If there is a problem of tamper-
ing, lock wire holes have been provided in cap and cover. Wire the cap to
cover and secure with lead seal.
DISASSEMBLY
The CRL Pressure Relief Control does not need to be removed from the
line for disassembly. Make sure that pressure shut down is accompanied
prior to disassembly. If the CRL is removed from the line for disassembly
be sure to use a soft jawed vise to hold body during work.
Refer to Parts List Drawing for Item Numbers.
1.
Remove cap (1), loosen jam nut (10) and turn adjusting
screw counterclockwise until spring tension is relieved.
2.
Remove the eight screws (4) holding the cover (3) and
powerunit body (6). Hold the cover and powerunit together
and place on a suitable work surface.
See NOTE under REASSEMBLY.
3.
Remove the cover (3) from powerunit body (6). The spring
(12) and two spring guides (11).
4.
Remove nut (13) from stem (19) and slide off the belleville washer
(14), the upper diaphragm washer (15) and the diaphragm (16).
5.
Pull the stem (19) with the disc retainer assembly (21) through the
bottom of powerunit. The lower diaphragm washer (17) will slide off
of stem top.
6.
Remove jam nut (23) and disc retainer assembly (21) from stem.
Use soft jawed pliers or vise to hold stem. The polished surface of
stem must not be scored or scratched.
7. The seat (22) need not be removed unless it is damaged. If removal
is necessary use proper size socket wrench and turn counterclockwise.
Note: Some models have an integral seat in the body (7).
INSPECTION
Inspect all parts for damage, or evidence of cross threading. Check
diaphragm and disc retainer assembly for tears, abrasions or other dam-
age. Check all metal parts for damage, corrosion or excessive wear.
REPAIR AND REPLACEMENT
Minor nicks and scratches may be polished out using 400 grit wet or dry
sandpaper fine emery or crocus cloth. Replace all O-rings and any dam-
aged parts.
When ordering replacement parts, be sure to specify parts list item num-
ber and all nameplate data.
REASSEMBLY
In general, reassembly is the reverse of disassembly. However, the fol-
lowing steps should be observed:
1. Lubricate the O-Ring (18) with a small amount of a good grade of
waterproof grease, (Dow Corning 44 medium grade or equal).
Use grease sparingly and install O-ring in powerunit body (6).
2. Install stem (19) in powerunit body (6). Use a rotating motion with
minimum pressure to let stem pass through O-ring.
Do Not Cut O-Ring.
3. Install O-ring (5) at top of stem (19). Place lower diaphragm
washer (17) on the stem with the serrated side up. Position
diaphragm (16), upper diaphragm washer (15), with serration down,
and belleville washer (14) with concave side down.
4. Position powerunit body (6) as shown on parts list drawing (top view).
5. Continue reassembly as outlined in disassembly steps 1 through 3.
Pressure Relief Control
CRL
Note:
Item (4) Screw will have a quantity of 8 for the 0-75 and 20-200psi
design and a quantity of 4 for the 100-300psi design. Item (25) Screw is
used on the 100-300psi design only. Install item (25), before item (4) for
preload of item (12) spring.
SYMPTOM
PROBABLE CAUSE
REMEDY
Fails to open.
Controlling pressure
too low.
Back off adjusting
screw until valve
opens.
Fails to open with
spring compression
removed.
Mechanical obstruc-
tion, corrosion, scale
build-up on stem.
Disassemble,
locate,and remove
obstruction, scale.
Leakage from cover
vent hole when con-
trolling pressure is
applied.
Diaphragm Damage
Disassembly replace
damaged
diaphragm.
Fails to close with
spring compressed.
Mechanical obstruc-
tion.
Disassemble, locate
and remove
obstruction.
Fails to close.
No spring compres-
sion.
Re-set pressure
adjustment.
Loose diaphragm
assembly.
Tighten upper
diaphragm washer.
MODEL
INSTALLATION / OPERATION / MAINTENANCE
CLA
-
VAL
Copyright Cla-Val 2005 Printed in USA Specifications subject to change without notice.
P.O. Box 1325
•
Newport Beach, CA 92659-0325
•
Phone: 949-722-4800
•
Fax: 949-548-5441
•
E-mail: [email protected]
•
Website cla-val.com
©
N-CRL (R-8/05)