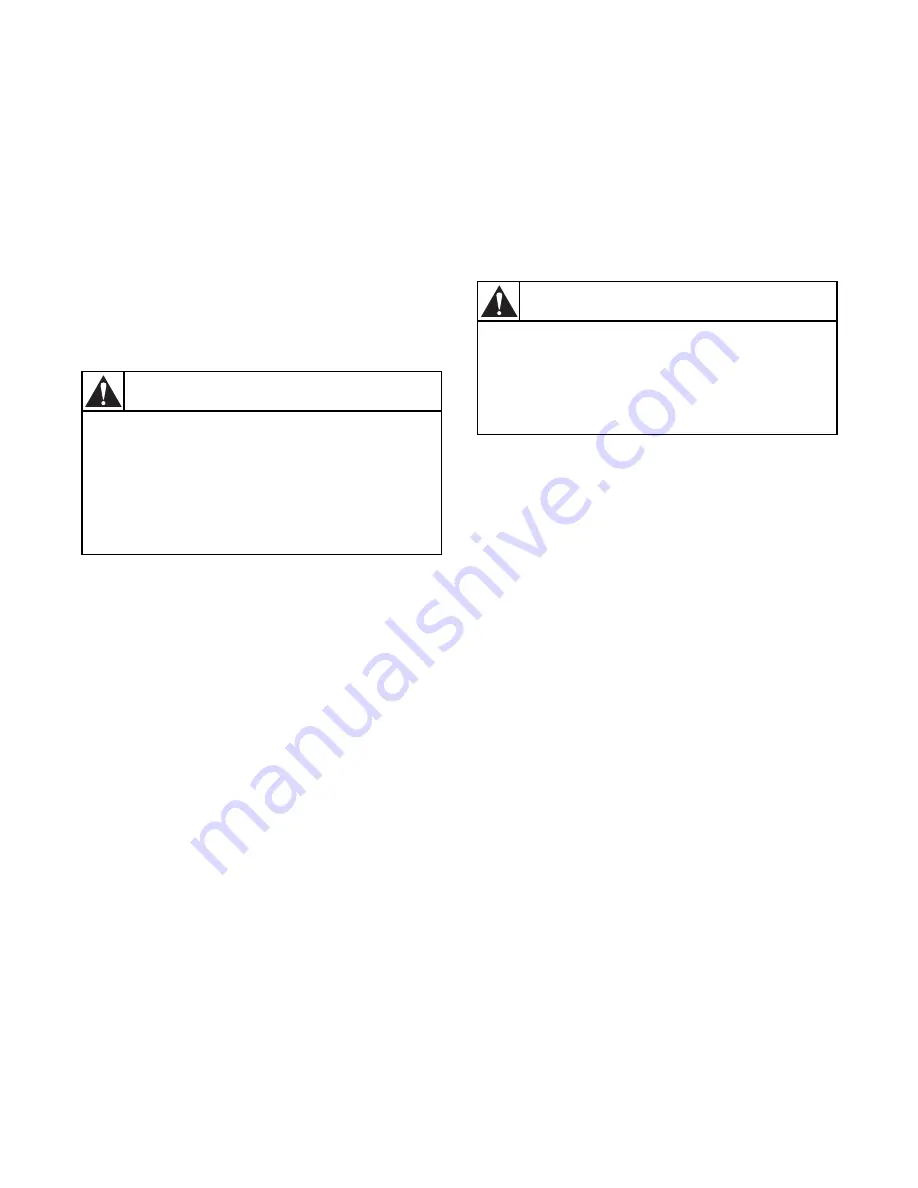
© Copyright, Alliance Laundry Systems LLC – DO NOT COPY or TRANSMIT
Maintenance
25
AJ0975
Cleaning Air Filter
Air filters remove foreign matter and condensate from
supply air as it passes through filter. The frequency at
which the filter baffle plate and filter element should
be cleaned depends upon the amount of condensate
and foreign matter in the supply air. The condensate
level should not raise above the baffle. That is a sign of
a faulty auto-drain which would need to be cleaned,
replaced or repaired.
Erratic regulator operations or loss of regulation is
almost always due to dirt.
The following steps outline the procedure for cleaning
the air filter.
1. Close and lock air service shut-off valve.
2. Remove filter bowl. Use a strap wrench if
required. Disassemble regulator, making notes as
a guide for reassembly.
3. Clean parts with household soap and blow out
body with compressed air.
IMPORTANT: DO NOT use cleansing agents such
as acetone, benzene, carbon tetrachloride, gasoline,
toluene, etc., which are damaging to the plastic
sight glass.
4. Reassemble per your notes. Make sure o-ring is
in position on the filter bowl. Tighten bowl to
filter body. Tighten slightly more than hand tight.
5. Open air service shut-off valve.
Maintenance kits available. Refer to parts manual for
numbers.
Cleaning Steam Strainer
Strainer removes foreign matter from steam. The
frequency at which the strainer must be cleaned is
dependent upon the amount of foreign matter
suspended in the steam. It is recommended that the
strainer screen be removed and checked for cleanliness
after 2 weeks or 80 hours of operation. If little or no
foreign matter has collected on the screen, time
between inspections can be increased accordingly.
Cleaning Customer-Furnished Steam
Traps
Some steam traps are provided with internal steam
strainers. These strainers should be cleaned.
All repairable traps should be opened at least once a
year to visually check operating mechanisms.
Remove sediment and dirt from trap body. The
mechanism may require cleaning by immersing in
appropriate cleaning fluid.
NOTE: Check instructions provided with trap or
with trap manufacturer for appropriate cleaning
fluids.
To avoid possible serious injury ALWAYS
close air supply line shut-off valve AND
lock out air service BEFORE:
• opening filter drain cock
• removing filter bowl
• filling oil bowl
W380
WARNING
To avoid possible serious injury when
cleaning or repairing traps or strainers:
• Shut off AND lock out ALL steam
service to press.
• Let heated surfaces cool.
W381
WARNING