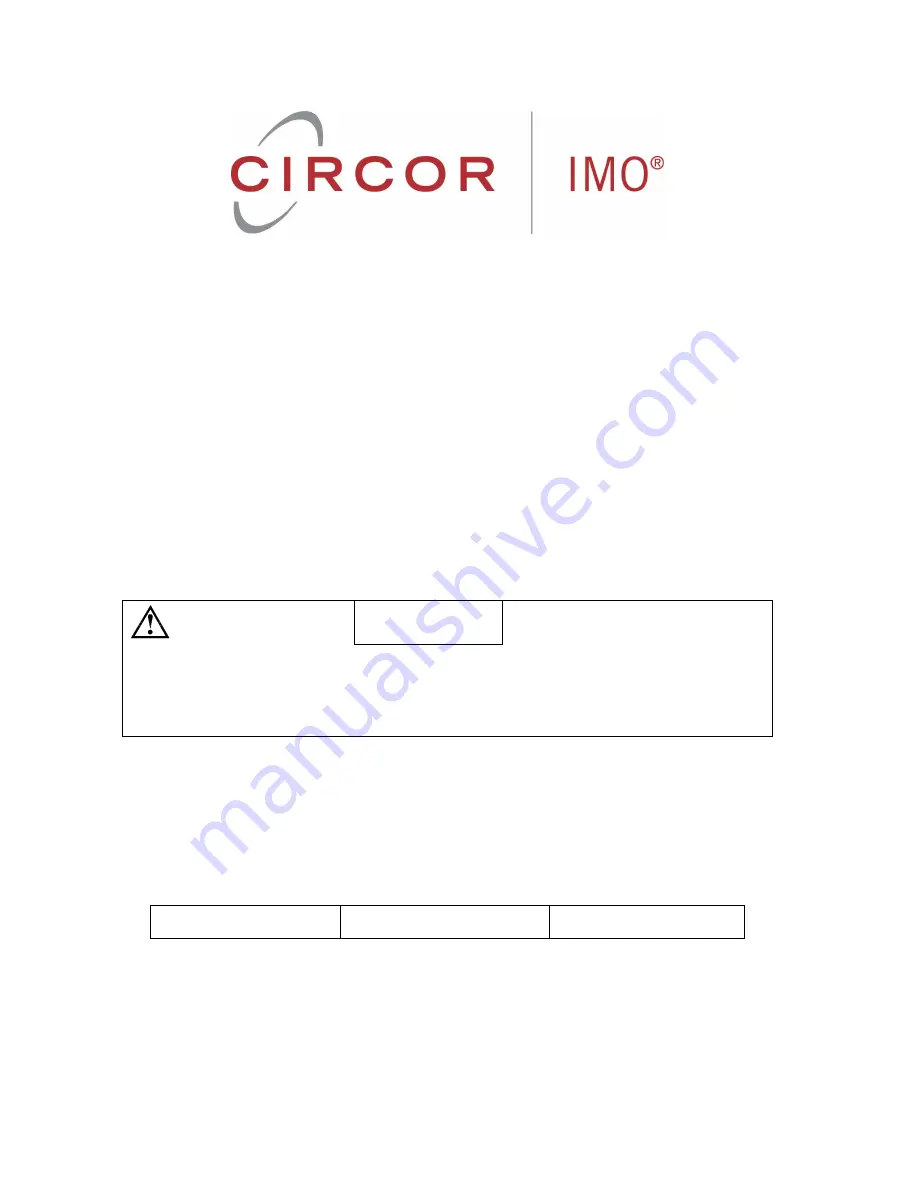
PRODUCT SERVICE MANUAL
FOR
CIG Lip Seal Double Pumps
WARNING
The Imo General Installation Operation, Maintenance, and
Troubleshooting Manual, (No. SRM00046), as well as all other component
manuals supplied with these type units should be read thoroughly prior
to pump installation, start-up, operation, maintenance or troubleshooting.
SRM00049
REV. 04 (20-0051) February
2020