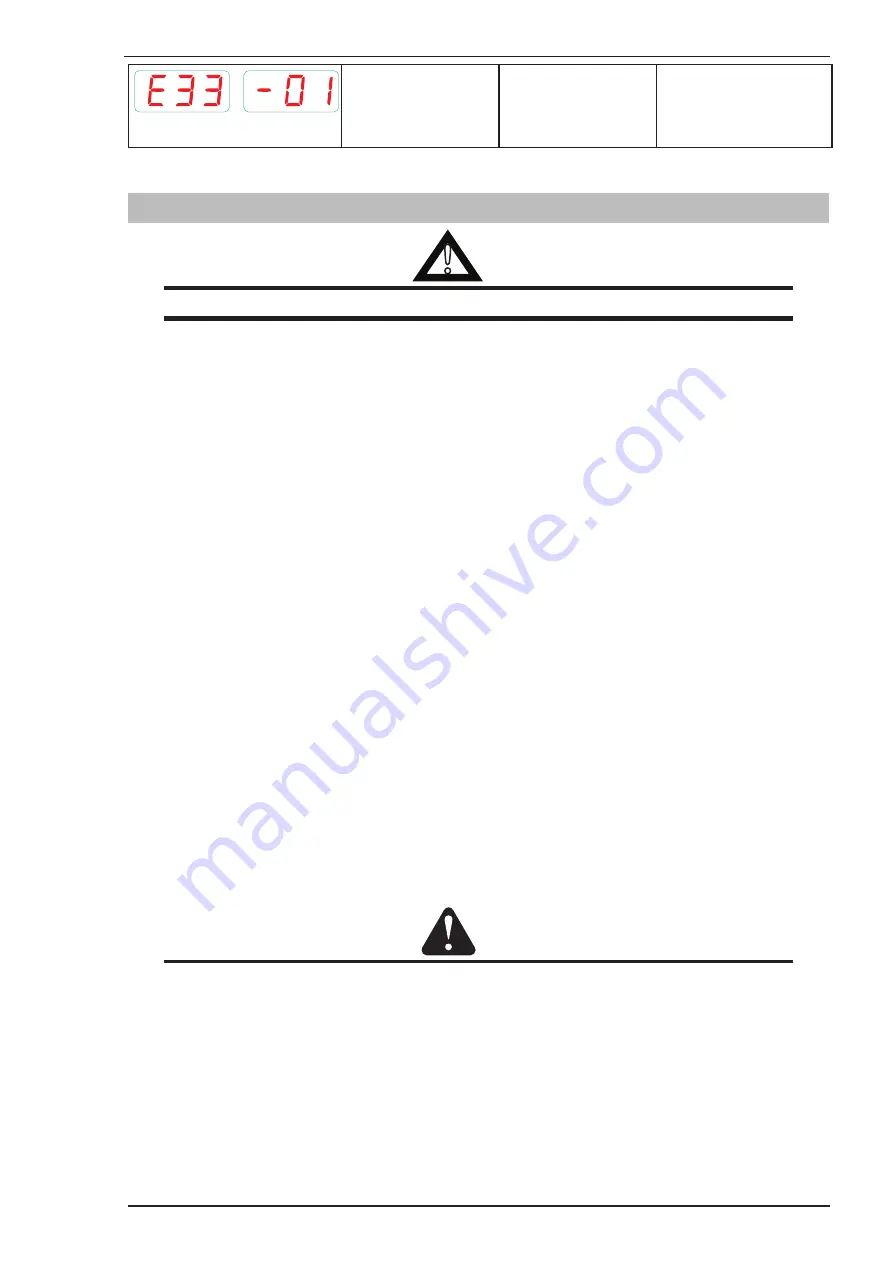
TRANSTIG 220AC/DC AND 300AC/DC POWER SOURCE
Manual 0-5293
3-35
INSTALLATION, OPERATION AND SETUP
Power Module
Power Module not
symmetrical
Have an Accredited
C I G W E L D S e r v i c e
Provider check the power
source
Table 3-12: Error Message
3.21 Shielding Gas Regulator Operating Instructions
!
WARNING
This equipment is designed for use with welding grade (Inert) shielding gases only.
Shielding Gas Regulator Safety
This regulator is designed to reduce and control high pressure gas from a cylinder or pipeline to the working
pressure required for the equipment using it.
If the equipment is improperly used, hazardous conditions are created that may cause accidents. It is the
users responsibility to prevent such conditions. Before handing or using the equipment, understand and
comply at all times with the safe practices prescribed in this instruction.
SPECIFIC PROCEDURES for the use of regulators are listed below.
1. NEVER subject the regulator to inlet pressure greater than its rated inlet pressure.
2. NEVER pressurize a regulator that has loose or damaged parts or is in a questionable condition. NEVER
loosen a connection or attempt to remove any part of a regulator until the gas pressure has been
relieved. Under pressure, gas can dangerously propel a loose part.
3. DO NOT remove the regulator from a cylinder without first closing the cylinder valve and releasing gas
in the regulator high and low pressure chambers.
4. DO NOT use the regulator as a control valve. When downstream equipment is not in use for extended
periods of time, shut off the gas at the cylinder valve and release the gas from the equipment.
5. OPEN the cylinder valve SLOWLY. Close after use.
User Responsibilities
This equipment will perform safely and reliable only when installed, operated and maintained, and repaired in
accordance with the instructions provided. Equipment must be checked periodically and repaired, replaced,
or reset as necessary for continued safe and reliable performance. Defective equipment should not be used.
Parts that are broken, missing, obviously worn, distorted, or contaminated should be replaced immediately.
The user of this equipment will generally have the sole responsibility for any malfunction, which results from
improper use, faulty maintenance, or by repair by anyone other than an accredited repairer.
CAUTION
Match regulator to cylinder. NEVER CONNECT a regulator designed for a particular gas or gases to
a cylinder containing any other gas.
Summary of Contents for A-12030
Page 6: ......