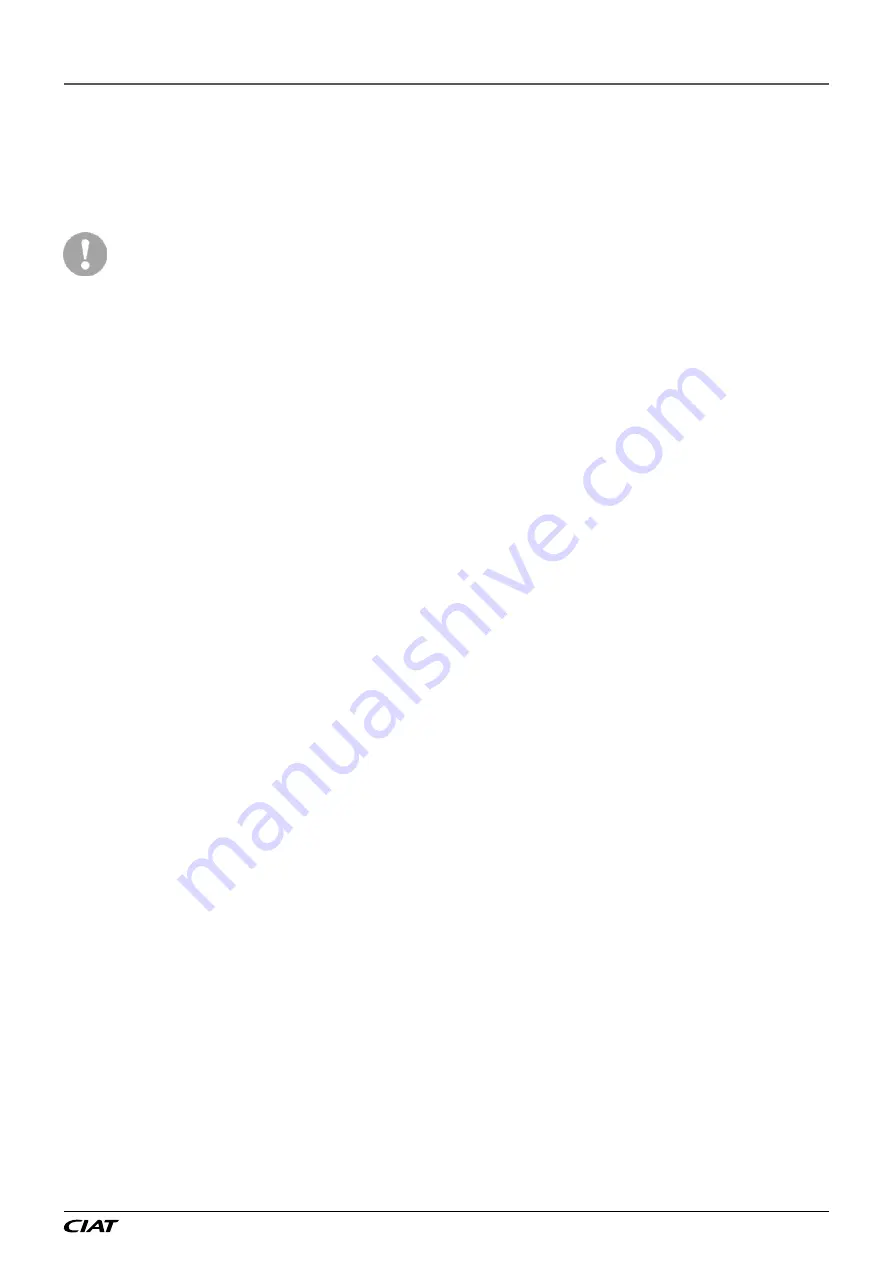
14 - STANDARD MAINTENANCE
The heat pumps must be maintained by professional technicians,
whilst routine checks can be carried out locally by specialised
technicians. See the standard EN 378-4.
All refrigerant charging, removal and draining operations
must be carried out by a qualified technician and with the
correct material for the unit. Any inappropriate handling can
lead to uncontrolled fluid or pressure leaks.
Before doing any work on the machine ensure that
the power is switched off. If a refrigerant circuit is
opened, it must be evacuated, recharged and tested
for leaks. Before any operation on a refrigerant
circuit, it is necessary to remove the complete
refrigerant charge from the unit with a refrigerant
charge recovery group.
Simple preventive maintenance will allow you to get the best
performance from your heat pump unit:
-
improved heating performance
-
reduced power consumption
-
prevention of accidental component failure
-
prevention of major time-consuming and costly interventions
-
protection of the environment
There are five maintenance levels for the heat pump units, as
defined by the AFNOR X60-010 standard.
14.1 - Level 1 maintenance
See note on the next page. Simple procedures, can be carried
out by the user on a weekly basis:
-
Visual inspection for oil traces (sign of a refrigerant leak),
-
Air heat exchanger (evaporator) cleaning - see chapter
‘Evaporator coil - level 1’,
-
Check for removed protection devices, and badly closed
doors/covers,
-
Check the unit alarm report when the unit does not work (see
Aquaciat Caléo™ TD Connect Touch control manual),
-
General visual inspection for any signs of deterioration,
-
Verify the charge in the sight-glass,
-
Check that the temperature difference between the heat
exchanger inlet and outlet is correct.
14.2 - Level 2 maintenance
This level requires specific know-how in the electrical, hydraulic
and mechanical fields. It is possible that these skills are available
locally: existence of a maintenance service, industrial site,
specialised subcontractor.
The frequency of this maintenance level can be monthly or
annually depending on the verification type.
In these conditions, the following maintenance operations are
recommended.
Carry out all level 1 operations, then:Electrical checks
-
At least once a year tighten the power circuit electrical screw
connections (see table with tightening torques).
-
Check and retighten all control/command screw connections,
if required (see table with tightening torques).
-
Remove the dust and clean the interior of the control boxes,
if required.
-
Check the status of the contactors and disconnect switches.
-
Check the presence and the condition of the electrical
protection devices.
-
Check the correct operation of all heaters.
-
Replace the fuses every 3 years or every 15000 hours (age-
hardening).
-
Check that no water has penetrated into the control box.
Mechanical checks
-
Check the tightening of the fan tower, fan, compressor and
control box fixing bolts.
Water circuit checks
-
Check the water connections.
-
Purge the water circuit (see chapter ‘Water flow control
procedure’).
-
Clean the water filter (see chapter ‘Water flow control
procedure’).
-
Check the operation of the flow switch.
-
Check the status of the thermal piping insulation.
-
Check the concentration of the anti-freeze protection solution
(ethylene glycol or polyethylene glycol).
Refrigerant circuit
-
Fully clean the air evaporators with a low-pressure jet and a
bio-degradable cleaner (counter-current cleaning - see
chapter ‘Evaporator coil - level 2).
-
Check the unit operating parameters and compare them with
previous values.
-
Carry out an oil contamination test. Replace the oil, if
necessary.
-
Check the operation of the high-pressure switches. Replace
them if there is a fault.
-
Check the fouling of the filter drier. Replace it if necessary.
-
Keep and maintain a maintenance sheet, attached to the unit.
All these operations require strict observation of adequate
safety measures: individual protection garments, compliance
with all industry regulations, compliance with applicable
local regulations and using common sense.
14.3 - Level 3 (or higher) maintenance
The maintenance at this level requires specific skills/approval/
tools and know-how and only the manufacturer, his representative
or authorised agent are permitted to carry out these operations.
These maintenance operations concern for example:
-
a major component replacement (compressor, condenser),
-
any intervention on the refrigerant circuit (handling refrigerant),
-
changing of parameters set at the factory (application change),
-
removal or dismantling of the unit,
-
any intervention due to a missed established maintenance
operation,
-
any intervention covered by the warranty.
To reduce waste, the refrigerant and the oil must be
transferred in accordance with applicable regulations, using
methods that limit refrigerant leaks and pressure drops and
with materials that are suitable for the products.
Any detected leaks must be repaired immediately.
The compressor oil that is recovered during maintenance
contains refrigerant and must be treated accordingly.
Refrigerant under pressure must not be purged to the open
air.
If a refrigerant circuit is opened, plug all openings, if the
operation takes up to one day, or for longer periods charge
the circuit with nitrogen.
NOTE: Any deviation or non-observation of these
maintenance criteria will render the guarantee conditions
for the unit nul and void, and the manufacturer, CIAT, will
no longer be held responsible.
EN-35 AQUACIAT
CALÉO™
TD