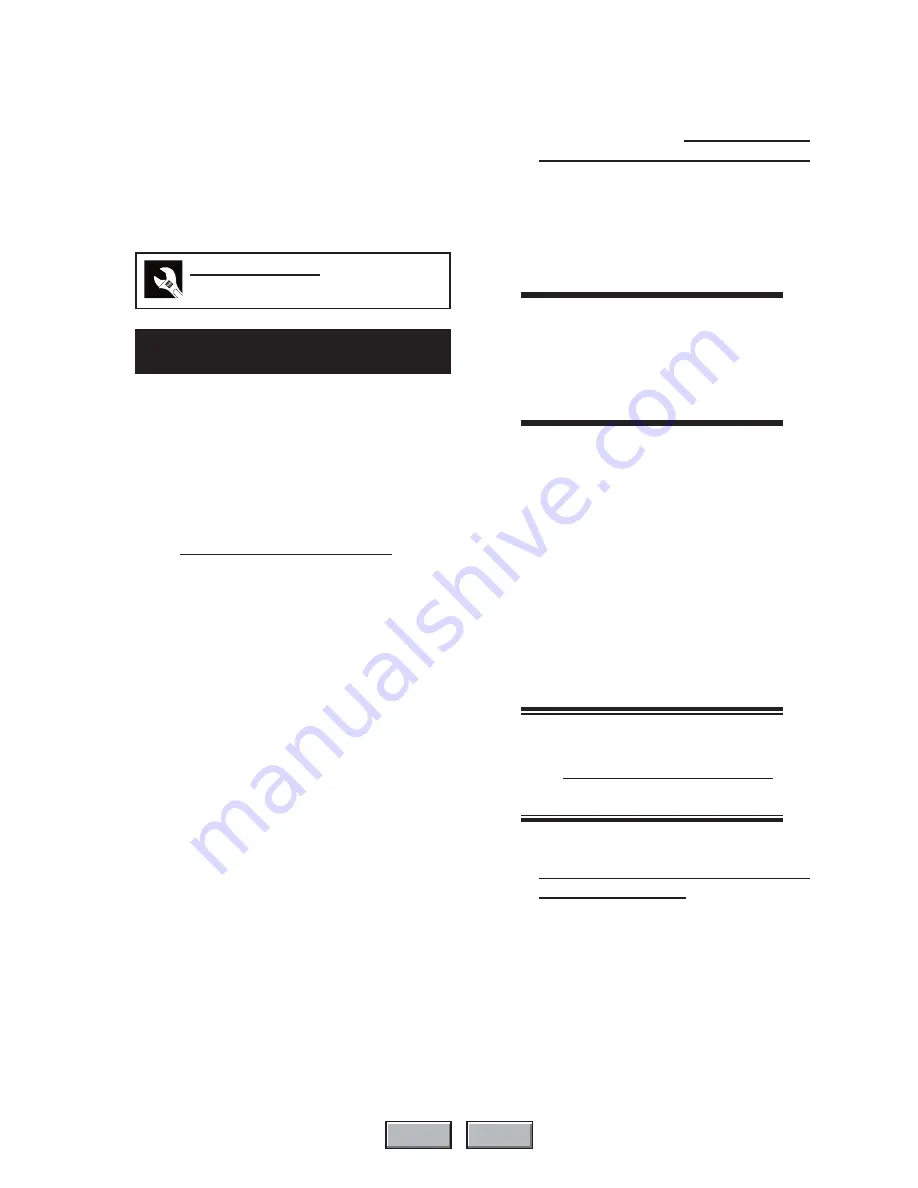
King Edge Vac
Repair
7-29
Replacing Broken or Missing Ribbons
Ribbons that break should be replaced
immediately. To avoid excessive stress on only
one new, slightly shorter ribbon, the entire set of
ribbons should be replaced. At a minimum, it is
recommended that ribbons be replaced in pairs.
Required Tools
3/8”, 9/16”, 3/4” wrenches, pliers
Perform only when the unit is OFF
with power disconnected.
Verify the replacement ribbons are the
correct size and of sufficient quantity for
completing the procedure. Refer to the
PARTS LIST
.
Turn power OFF at the main disconnect
switch.
Only if the front bypass ribbon set is to
be replaced:
Turn ON the compressed air supply
to the unit.
Locate the right pneumatic panel (Fig-
ure 7-33) just to the right of the center
of the machine.
On the bottom of this unit is the main
solenoid valve. Locate the override
screw on this valve (Figure 7-34).
Use a small screwdriver to push in
the lockout screw and turn it 1/4 turn
clockwise to lock it in the “in” position.
This allows compressed air to flow to
the pneumatic control solenoids.
On the right pneumatic panel, locate
the solenoid air valve for the front by-
pass conveyor (Figure 7-37) and locate
its lockout screw.
Use a small screwdriver to push in
the lockout screw and turn it 1/4 turn
clockwise to lock it in the “in” posi-
tion. The front bypass conveyor should
rise.
1.
2.
3.
a)
b)
c)
d)
e)
f)
Release tension on the appropriate rib-
bon set following the
Discharge/ByPass
Conveyors Ribbon Tension Adjustment
procedure earlier in this section.
Remove a ribbon from each end of the
unit and use one or both as replacement
ribbons. The end ribbons can then be re-
placed by a pair of new ribbons.
WARNING
Never turn on power while
pulling the ribbons through.
This is dangerous and
unnecessary.
Push the ribbon along its path under the
doffer roll and around the drive and idler
rolls. For discharge and rear bypass rib-
bons, make sure the 1/2 right twist is main-
tained on the underside of their respective
conveyors (Figure 7-40).
Bring the ends of the ribbon together and
connect them with a new pin.
Repeat Steps 5 to 7 to replace additional
ribbons. Stagger the positions of the lacing
clips to give the flatwork a smooth flow.
NOTE:
If the remaining ribbons
are being replaced, refer to
the
Replacing Worn Ribbons
procedure.
Adjust ribbon tension following the
Discharge/ByPass Conveyors Ribbon
Tension Adjustment
procedure earlier
in this section.
If the front bypass ribbon set was replaced,
lower the conveyor by reversing Step 3.
4.
5.
6.
7.
8.
9.
10.
TOC
INDEX
Summary of Contents for King Edge VAc
Page 12: ......
Page 40: ......
Page 54: ......
Page 78: ......
Page 250: ...3038 015e King Edge VAC PL 32 This page intentionally left blank TOC INDEX PL TOC...
Page 262: ...SC 2 460V Motor Circuit SC TOC TOC INDEX...
Page 264: ...SC 4 208 230V Motor Circuit SC TOC TOC INDEX...
Page 266: ...SC 6 Control Power Communications SC TOC TOC INDEX...
Page 268: ...SC 8 Controller Inputs SC TOC TOC INDEX...
Page 270: ...SC 10 Control Outputs SC TOC TOC INDEX...
Page 273: ...King Edge Vac 3210 437b SC 13 This page intentionally left blank SC TOC TOC INDEX...
Page 274: ...SC 14 Prefeeder Control Circuit SC TOC TOC INDEX...
Page 276: ...3210 437b King Edge Vac SC 16 This page intentionally left blank SC TOC TOC INDEX...
Page 277: ...SC 17 24 VAC Control Circuit SC TOC TOC INDEX...
Page 278: ...SC 18 Interlock Circuit system E stop SC TOC TOC INDEX...
Page 279: ...SC 19 Pneumatic Diagram SC TOC TOC INDEX...
Page 280: ...SC 20 Prefeeder Electrical Panel SC TOC TOC INDEX...
Page 282: ...SC 22 Disconnect Panel SC TOC TOC INDEX...
Page 284: ...SC 24 Main Eletrical Panel SC TOC TOC INDEX...
Page 285: ......
Page 286: ......
Page 287: ......
Page 288: ......
Page 290: ......
Page 292: ......
Page 302: ......