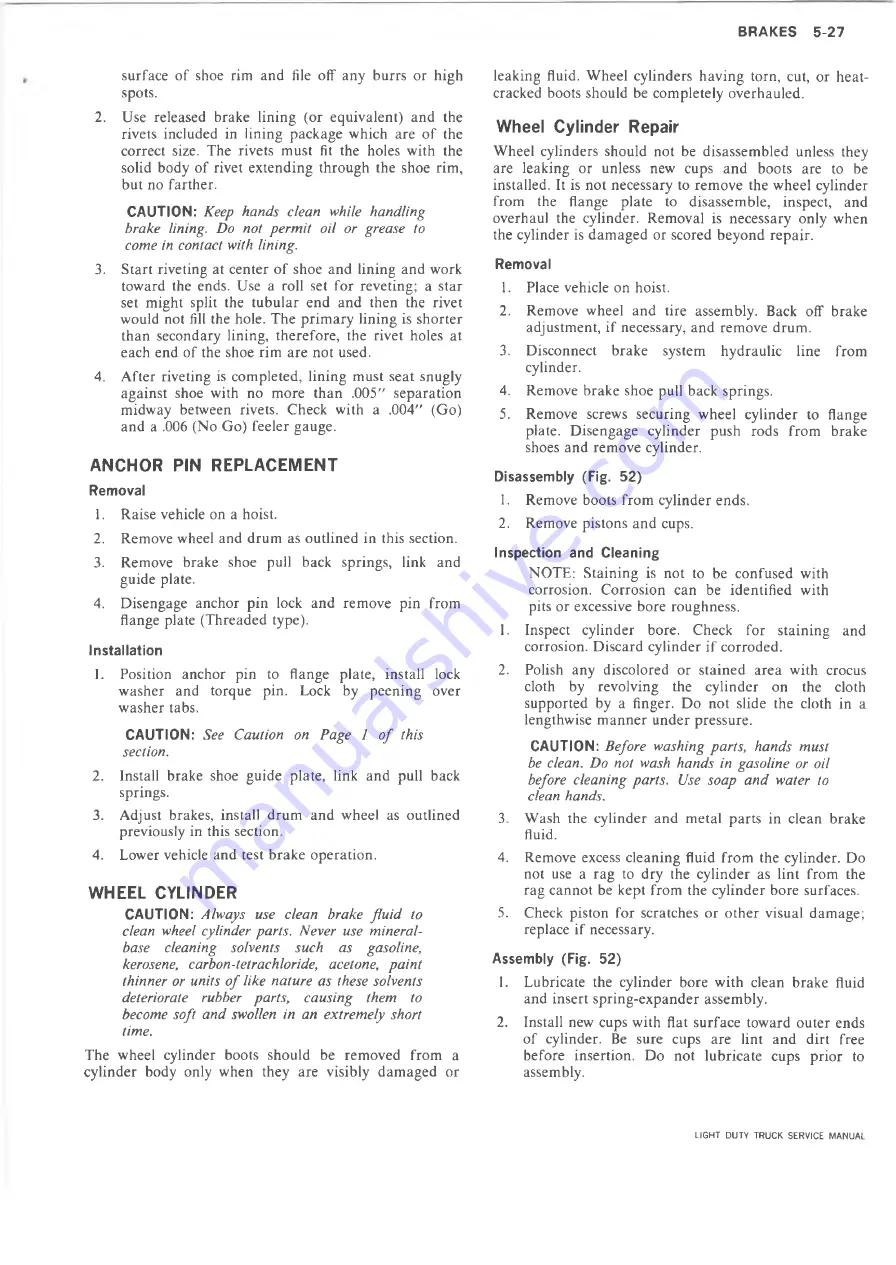
BRAKES
5 -2 7
surface of shoe rim and file off any burrs or high
spots.
2. Use released brake lining (or equivalent) and the
rivets included in lining package which are of the
correct size. The rivets must fit the holes with the
solid body of rivet extending through the shoe rim,
but no farther.
CAUTION:
Keep hands clean while handling
brake lining. Do not permit oil or grease to
come in contact with lining.
3. Start riveting at center of shoe and lining and work
toward the ends. Use a roll set for reveting; a star
set might split the tubular end and then the rivet
would not fill the hole. The primary lining is shorter
than secondary lining, therefore, the rivet holes at
each end of the shoe rim are not used.
4. After riveting is completed, lining must seat snugly
against shoe with no more than .005" separation
midway between rivets. Check with a .004" (Go)
and a .006 (No Go) feeler gauge.
ANCHOR PIN REPLACEMENT
Removal
1. Raise vehicle on a hoist.
2. Remove wheel and drum as outlined in this section.
3. Remove brake shoe pull back springs, link and
guide plate.
4. Disengage anchor pin lock and remove pin from
flange plate (Threaded type).
Installation
1. Position anchor pin to flange plate, install lock
washer and torque pin. Lock by peening over
washer tabs.
CAUTION:
See Caution on Page 1 of this
section.
2. Install brake shoe guide plate, link and pull back
springs.
3. Adjust brakes, install drum and wheel as outlined
previously in this section.
4. Lower vehicle and test brake operation.
WHEEL CYLINDER
CAUTION:
Always use clean brake fluid to
clean wheel cylinder parts. Never use mineral-
base cleaning solvents such as gasoline,
kerosene, carbon-tetrachloride, acetone, paint
thinner or units of like nature as these solvents
deteriorate rubber parts, causing them to
become soft and swollen in an extremely short
time.
The wheel cylinder boots should be removed from a
cylinder body only when they are visibly damaged or
leaking fluid. Wheel cylinders having torn, cut, or heat-
cracked boots should be completely overhauled.
Wheel Cylinder Repair
Wheel cylinders should not be disassembled unless they
are leaking or unless new cups and boots are to be
installed. It is not necessary to remove the wheel cylinder
from the flange plate to disassemble, inspect, and
overhaul the cylinder. Removal is necessary only when
the cylinder is damaged or scored beyond repair.
Removal
1. Place vehicle on hoist.
2. Remove wheel and tire assembly. Back off brake
adjustment, if necessary, and remove drum.
3. Disconnect brake system hydraulic line from
cylinder.
4. Remove brake shoe pull back springs.
5. Remove screws securing wheel cylinder to flange
plate. Disengage cylinder push rods from brake
shoes and remove cylinder.
Disassembly (Fig.
52)
1. Remove boots from cylinder ends.
2. Remove pistons and cups.
Inspection and Cleaning
NOTE: Staining is not to be confused with
corrosion. Corrosion can be identified with
pits or excessive bore roughness.
1. Inspect cylinder bore. Check for staining and
corrosion. Discard cylinder if corroded.
2. Polish any discolored or stained area with crocus
cloth by revolving the cylinder on the cloth
supported by a finger. Do not slide the cloth in a
lengthwise manner under pressure.
CAUTION:
Before washing parts, hands must
be clean. Do not wash hands in gasoline or oil
before cleaning parts. Use soap and water to
clean hands.
3. Wash the cylinder and metal parts in clean brake
fluid.
4. Remove excess cleaning fluid from the cylinder. Do
not use a rag to dry the cylinder as lint from the
rag cannot be kept from the cylinder bore surfaces.
5. Check piston for scratches or other visual damage;
replace if necessary.
Assembly (Fig.
52)
1. Lubricate the cylinder bore with clean brake fluid
and insert spring-expander assembly.
2. Install new cups with flat surface toward outer ends
of cylinder. Be sure cups are lint and dirt free
before insertion. Do not lubricate cups prior to
assembly.
LIGHT DUTY TRUCK SERVICE MANUAL
Summary of Contents for Light Duty Truck 1973
Page 1: ......
Page 4: ......
Page 6: ......
Page 53: ...HEATER AND AIR CONDITIONING 1A 27 LIGHT DUTY TRUCK SERVICE MANUAL...
Page 115: ...LIGHT DUTY TRUCK SERVICE M A N U A L HEATER AND AIR CONDITIONING 1A 89...
Page 123: ...BODY 1B 3 Fig 6 Typical 06 Van LIGHT DUTY TRUCK SERVICE MANUAL...
Page 149: ...BODY 1B 29 Fig 84 Body Mounting 06 Fig 85 Body Mounting 14 LIGHT DUTY TRUCK SERVICE MANUAL...
Page 171: ...LIGHT DUTY TRUCK SERVICE M A N U A L Fig 2 Frame Horizontal Checking Typical FRAME 2 3...
Page 173: ...LIGHT DUTY TRUCK SERVICE M A N U A L Fig 4 10 30 Series Truck Frame FRAME 2 5...
Page 174: ...2 6 FRAME LIGHT DUTY TRUCK SERVICE MANUAL Fig 5 Underbody Reference Points G Van...
Page 185: ...FRONT SUSPENSION 3 11 Fig 16 Toe out on Turns LIGHT DUTY TRUCK SERVICE MANUAL...
Page 224: ......
Page 266: ......
Page 351: ...ENGINE 6 15 Fig ID Sectional View of Eight Cylinder Engine LIGHT DUTY TRUCK SERVICE MANUAL...
Page 375: ...EN G IN E 6 39 LIGHT DUTY TRUCK SERVICE MANUAL...
Page 376: ...6 4 0 ENGINE LIGHT DUTY TRUCK SERVICE MANUAL...
Page 377: ...ENG IN E 6 41 LIGHT DUTY TRUCK SERVICE MANUAL...
Page 378: ...LIGHT DUTY TRUCK SERVICE MANUAL Fig 37L K Series Engine Front Mount 6 42 ENG INE...
Page 400: ...6 6 4 ENG INE LIGHT DUTY TRUCK SERVICE MANUAL...
Page 401: ...ENG IN E 6 65 LIGHT DUTY TRUCK SERVICE MANUAL...
Page 402: ...6 6 6 ENGINE LIGHT DUTY TRUCK SERVICE MANUAL...
Page 403: ...E NG IN E 6 67 Fig 36V C Series Engine Mounts LIGHT DUTY TRUCK SERVICE MANUAL...
Page 410: ......
Page 423: ...EN G IN E C OOLING 6K 13 Fig 16 Overheating Chart LIGHT DUTY TRUCK SERVICE MANUAL...
Page 424: ...6 K 1 4 ENG INE COOLING Fig 17 Coolant Loss Chart LIGHT DUTY TRUCK SERVICE MANUAL...
Page 456: ...6M 32 ENGINE FUEL Fig K15 Accelerator Controls G Van L 6 LIGHT DUTY TRUCK SERVICE MANUAL...
Page 492: ......
Page 512: ...Fig 18e Vacuum Advance Diagram V8 Engine...
Page 516: ...6 T 2 4 E M IS S IO N CONTROL SYSTEMS LIGHT DUTY TRUCK SERVICE MANUAL...
Page 528: ......
Page 590: ......
Page 593: ...CLUTCHES MANUAL TRANSMISSIONS 7M 3 LIGHT DUTY TRUCK SERVICE MANUAL...
Page 598: ...7M 8 CLUTCHES MANUAL TRANSMISSIONS LIGHT DUTY TRUCK SERVICE MANUAL...
Page 642: ......
Page 654: ......
Page 743: ...FUEL TANKS AND EXHAUST 8 13 LIGHT DUTY TRUCK SERVICE MANUAL...
Page 744: ...8 14 FUEL TANKS AND EXHAUST LIGHT DUTY TRUCK SERVICE MANUAL...
Page 760: ...8 30 FUEL TANKS AND EXHAUST Fig 40 Exhaust Pipe P Models LIGHT DUTY TRUCK SERVICE MANUAL...
Page 761: ...FUEL TANKS AND EXHAUST 8 31 LIGHT DUTY TRUCK SERVICE MANUAL...
Page 763: ...FUEL TANKS AND EXHAUST 8 33 LIGHT DUTY TRUCK SERVICE MANUAL...
Page 766: ......
Page 832: ...LIGHT DUTY TRUCK SERVICE MANUAL Fig 106 Power Steering Pump Mounting Typical 9 66 STEERING...
Page 833: ...PUMP ASSEMBLY STEERING GEAR TYPICAL SMALL V8 TYPICAL LARGE V8 STEERING 9 67...
Page 861: ...STEERING 9 95 Fig 134 Power Steering Pump Leakage LIGHT DUTY TRUCK SERVICE MANUAL...
Page 864: ......
Page 876: ......
Page 886: ...11 10 CHASSIS SHEET METAL LIGHT DUTY TRUCK SERVICE MANUAL...
Page 891: ...ELECTRICAL BODY AND CHASSIS 12 5 LIGHT DUTY TRUCK SERVICE MANUAL...
Page 934: ......
Page 942: ......
Page 970: ......
Page 972: ......
Page 974: ......
Page 976: ...V...
Page 978: ......
Page 979: ......