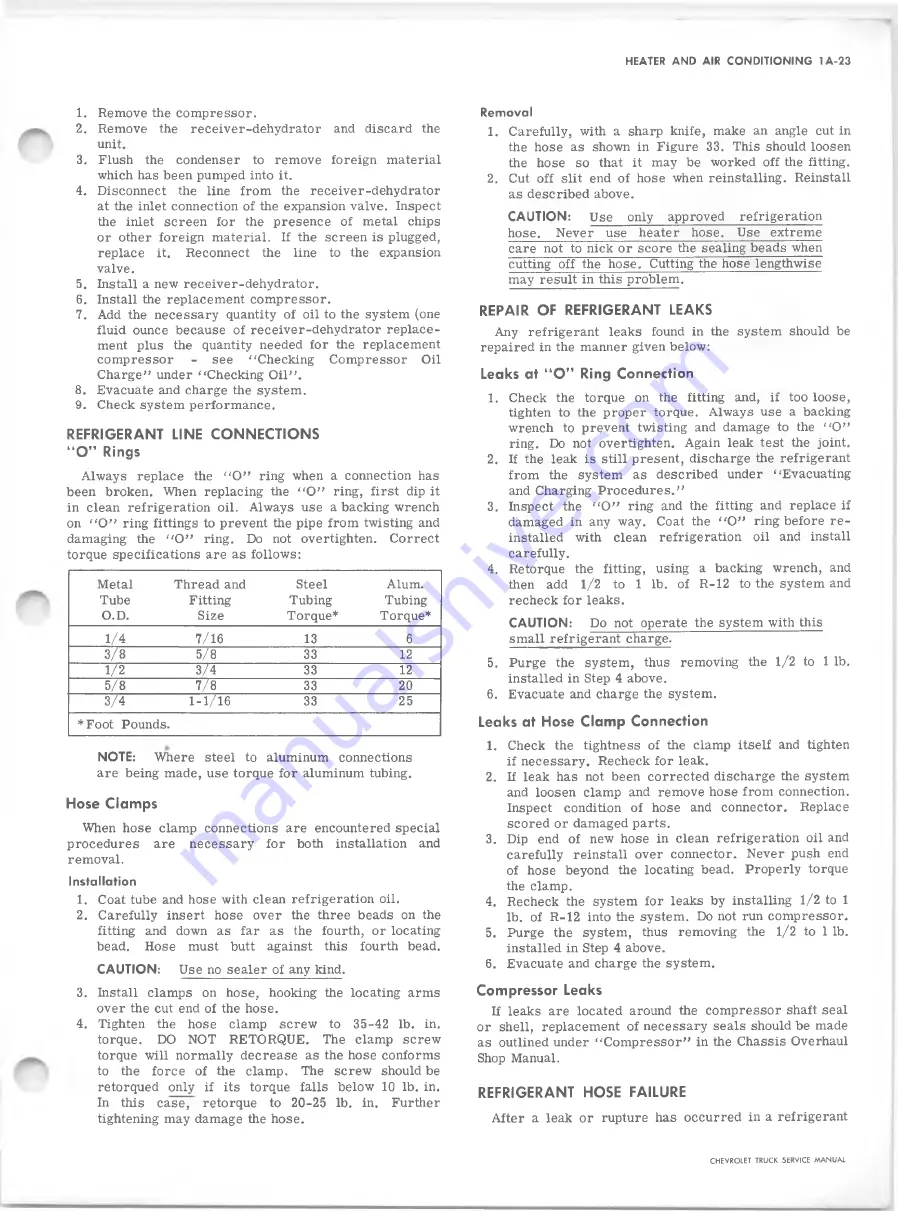
HEATER AND AIR CONDITIONING 1A-23
1. Remove the compressor.
2. Remove the receiver-dehydrator and discard the
unit.
3. Flush the condenser to remove foreign material
which has been pumped into it.
4. Disconnect the line from the receiver-dehydrator
at the inlet connection of the expansion valve. Inspect
the inlet screen for the presence of metal chips
or other foreign material. If the screen is plugged,
replace it.
Reconnect the line to the expansion
valve.
5. Install a new receiver-dehydrator.
6. Install the replacement compressor.
7. Add the necessary quantity of oil to the system (one
fluid ounce because of receiver-dehydrator replace
ment plus the quantity needed for the replacement
compressor
- see
“ Checking Compressor Oil
Charge” under “ Checking Oil” .
8. Evacuate and charge the system.
9. Check system performance.
REFRIGERANT LINE CONNECTIONS
“ O ” Rings
Always replace the “ O” ring when a connection has
been broken. When replacing the “ O” ring, first dip it
in clean refrigeration oil. Always use a backing wrench
on “ O” ring fittings to prevent the pipe from twisting and
damaging the “ O” ring. Do not overtighten. Correct
torque specifications are as follows:
Metal
Tube
O.D.
Thread and
Fitting
Size
Steel
Tubing
Torque*
Alum.
Tubing
Torque*
1/4
7/16
13
6
3/8
5/8
33
12
1/2
3/4
33
12
5/8
7/8
33
20
3/4
1-1/16
33
25
*Foot Pounds.
NOTE:
Where steel to aluminum connections
are being made, use torque for aluminum tubing.
Hose Clamps
When hose clamp connections are encountered special
procedures are necessary for both installation and
removal.
Installation
1. Coat tube and hose with clean refrigeration oil.
2. Carefully insert hose over the three beads on the
fitting and down as far as the fourth, or locating
bead. Hose must butt against this fourth bead.
CA U TIO N :
Use no sealer of any kind.
3. Install clamps on hose, hooking the locating arms
over the cut end of the hose.
4. Tighten the hose clamp screw to 35-42 lb. in.
torque. DO NOT RETORQUE. The clamp screw
torque will normally decrease as the hose conforms
to the force of the clamp. The screw should be
retorqued only if its torque falls below 10 lb. in.
In this case, retorque to 20-25 lb. in. Further
tightening may damage the hose.
Removal
1. Carefully, with a sharp knife, make an angle cut in
the hose as shown in Figure 33. This should loosen
the hose so that it may be worked off the fitting.
2. Cut off slit end of hose when reinstalling. Reinstall
as described above.
CA U TIO N :
Use only approved refrigeration
hose. Never use heater hose. Use extreme
care not to nick or score the sealing beads when
cutting off the hose. Cutting the hose lengthwislT
may result in this problem.
REPAIR OF REFRIGERANT LEAKS
Any refrigerant leaks found in the system should be
repaired in the manner given below:
Leaks at “ O ” Ring Connection
1. Check the torque on the fitting and, if too loose,
tighten to the proper torque. Always use a backing
wrench to prevent twisting and damage to the “ O”
ring. Do not overtighten. Again leak test the joint.
2. If the leak is still present, discharge the refrigerant
from the system as described under “ Evacuating
and Charging Procedures.”
3. Inspect the “ O” ring and the fitting and replace if
damaged in any way. Coat the “ O” ring before re
installed with clean refrigeration oil and install
carefully.
4. Retorque the fitting, using a backing wrench, and
then add 1/2 to 1 lb. of R-12 to the system and
recheck for leaks.
CA U TIO N :
Do not operate the system with this
small refrigerant charge.
5. Purge the system, thus removing the 1/2 to 1 lb.
installed in Step 4 above.
6. Evacuate and charge the system.
Leaks at Hose Clamp Connection
1. Check the tightness of the clamp itself and tighten
if necessary. Recheck for leak.
2. If leak has not been corrected discharge the system
and loosen clamp and remove hose from connection.
Inspect condition of hose and connector. Replace
scored or damaged parts.
3. Dip end of new hose in clean refrigeration oil and
carefully reinstall over connector. Never push end
of hose beyond the locating bead. Properly torque
the clamp.
4. Recheck the system for leaks by installing 1/2 to 1
lb. of R-12 into the system. Do not run compressor.
5. Purge the system, thus removing the 1/2 to 1 lb.
installed in Step 4 above.
6. Evacuate and charge the system.
Compressor Leaks
If leaks are located around the compressor shaft seal
or shell, replacement of necessary seals should be made
as outlined under “ Compressor” in the Chassis Overhaul
Shop Manual.
REFRIGERANT HOSE FAILURE
After a leak or rupture has occurred in a refrigerant
CHEVROLET TRUCK SERVICE MANUAL
Summary of Contents for 10 Series 1968
Page 1: ...ST 1 3 3 SB...
Page 3: ...w w...
Page 52: ...HEATER AND AIR CONDITIONING 1A 21 Fig 32 Charging Schematic CHEVROLET TRUCK SERVICE MANUAL...
Page 67: ......
Page 128: ...BODY IB 61 Fig 135 A uxiliary Seat CHEVROLET TRUCK SERVICE MANUAL...
Page 132: ...Fig 4 1 0 3 0 Series Truck Frame...
Page 133: ...Fig 5 4 0 6 0 Single A xle Truck Frame E x c Tilt Cab...
Page 135: ...Fig 7 4 0 6 0 Series Tilt Cab Truck Frames...
Page 139: ...w...
Page 169: ...fit w...
Page 233: ...I...
Page 248: ...BRAKES 5 15 TD 50 60 Fig 26 Parking Brake Cables T Models CHEVROLET TRUCK SERVICE MANUAL...
Page 347: ......
Page 389: ......
Page 393: ......
Page 411: ...ENGINE FUEL 6M 18 Fig 18A V 8 Typical CHEVROLET TRUCK SERVICE MANUAL...
Page 525: ......
Page 551: ......
Page 583: ...CHASSIS SHEET METAL 11 12 Fig 20 Designation and Name Plate CHEVROLET TRUCK SERVICE MANUAL...
Page 587: ...ELECTRICAL BODY AND CHASSIS 12 2 Fig 1 Fuse Panel CHEVROLET TRUCK SERVICE MANUAL...
Page 611: ...r ELECTRICAL BODY AND CHASSIS 12 26 9 CHEVROLET TRUCK SERVICE MANUAL...
Page 663: ......
Page 686: ...w...
Page 698: ...SPECIFICATIONS 12 ENGINE TORQUES CHEVROLET TRUCK SERVICE MANUAL...
Page 713: ...9...