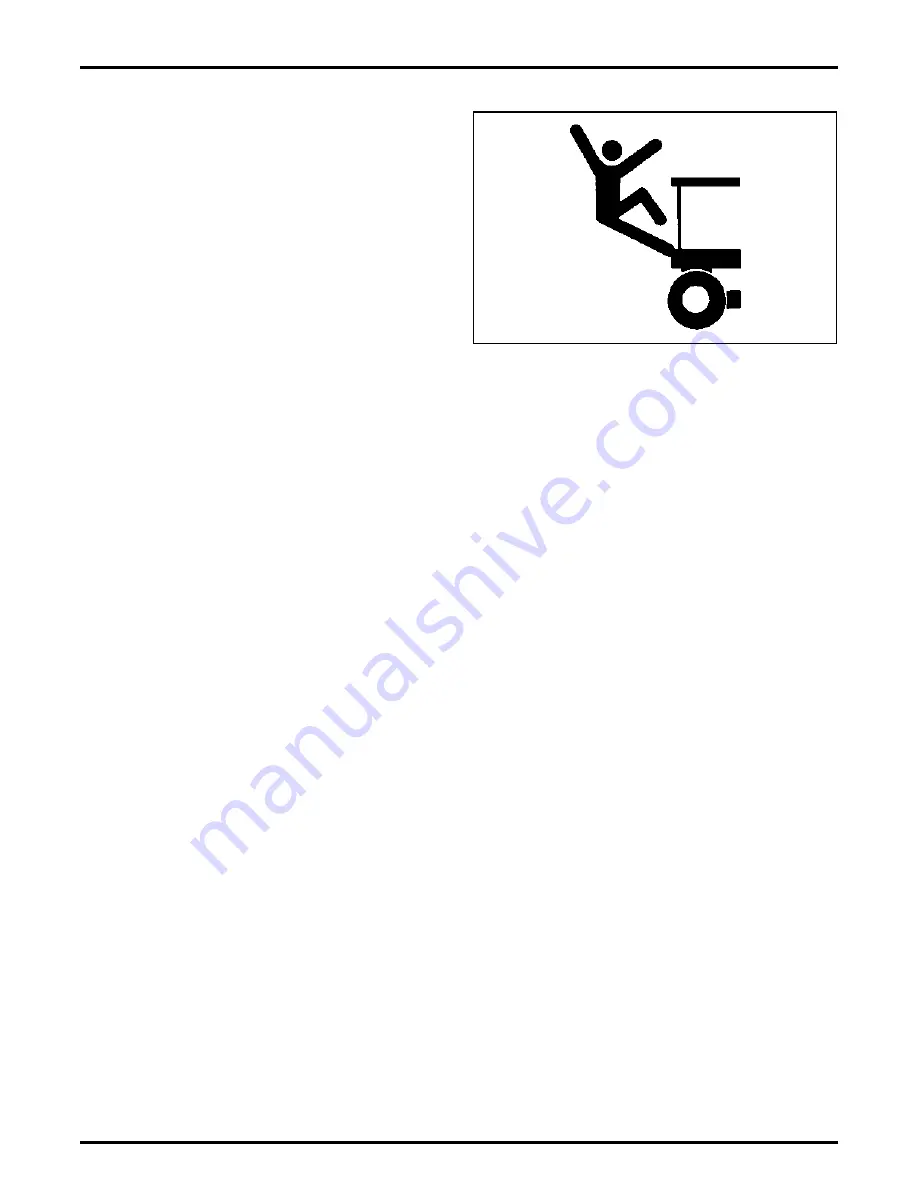
79033095 C Rev.
1-7
Introduction
Mounting and Dismounting
FIG. 8:
Mount and dismount machine only where there
are steps and/or hand holds. Face machine whenever
mounting or dismounting.
Maintain three-point contact with steps and hand holds.
Three-point contact is two feet and one hand or one foot
and two hands.
Never mount or dismount a moving machine. Never jump
off machine except in an emergency.
Do not carry tools or supplies when trying to mount or
dismount machine. Use a hand line to pull equipment
onto platform.
Do not use any controls as hand holds when entering or
exiting operator compartment.
IMPORTANT: Make sure steps are not adjusted too
close to hood of machine.
Leave a minimum dimension of 75 mm between inside
hand hold and hood so there is enough room for
operator's hand.
Crushing Prevention and Cutting
Prevention
Stay clear of center articulation joint area of machine
when engine is running. Connect articulation joint stop
whenever servicing this area.
Support equipment properly when performing work under
equipment. Do not depend on hydraulic cylinders to hold
equipment.
m
WARNING: An implement can fall if a
control lever is moved or if a hydraulic line
breaks.
Never jump across starter solenoid terminals to start
machine. Unexpected machine movement could result.
Never attempt adjustments while machine is moving or
while engine is running.
Whenever there are attachment control linkages,
clearance in linkage area changes with movement of
attachment.
Stay clear of all rotating and moving parts. Keep objects
away from moving fan blades. Fan blades will throw and
cut objects.
Wear gloves to handle wire cable and do not use kinked
or frayed wire cable.
Retainer pins can fly when struck, ensure there are no
personnel in area before striking. Wear protective glasses
to protect eyes. When striking objects, chips or other
debris may fly off. Ensure there will be no injury prior to
striking any object.
FIG. 8
N020903008
Find manuals at http://best-manuals.com/search?&s=CHAL-79033095