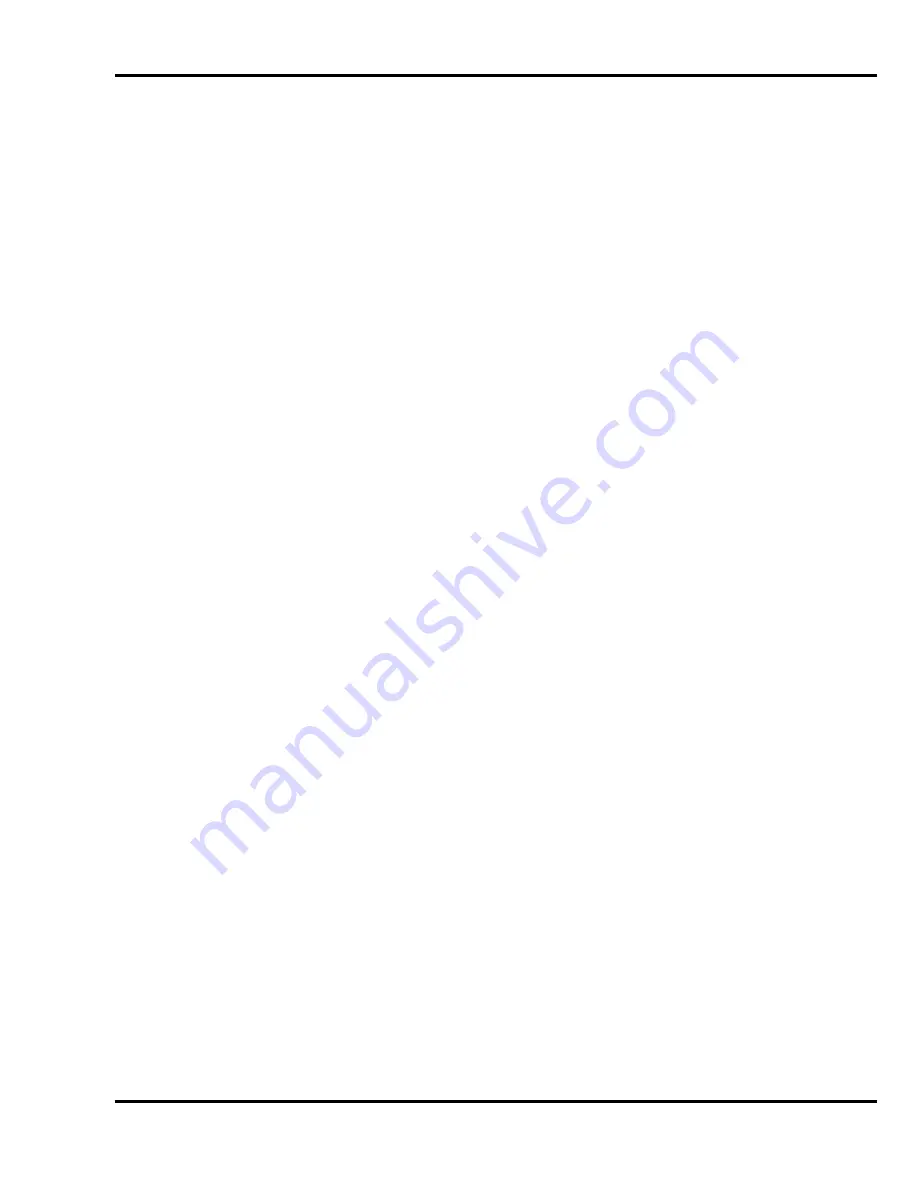
8.0 Maintenance Guide
29
The knife makes a “rougher” sound as it passes through stock.
Nicks are visible on the cutting edge of the knife.
8.1.4 Bevel Angle
The most appropriate bevel angle depends upon four factors.
1. The length of time desired between sharpening
2. Physical properties of the stock being cut (hardness, impurities, density)
3. Power output of machine
4. Amount of clamp pressure applied
1. Length of Time Between Sharpening
Under identical cutting conditions, knives with larger bevel angles will require sharpening less
frequently than knives with smaller bevel angles. There is more material supporting the cutting
edge of larger bevel angles.
2.
Physical Properties of Stock
In general a smaller bevel achieves a better quality cut. Hard, dense, and impure papers,
however, will dull a small angle bevel quickly. Impurities may put nicks on the cutting edge.
As a result, cut quality is lost quickly, and knives require sharpening often. Therefore, a
larger angle bevel should be chosen for such materials. Soft materials can be cut with small
angle bevels without adversely affecting sharpening frequency.
3.
Power Output of Machine
As the bevel angle increases, more power is required to push the knife through stock. If a
bevel angle is too large for a machine, the machine may take excessive wear-and-tear and
may stall part way through the cut cycle. Although the knife will require sharpening less
often, the machine may incur costly damage.
4.
Amount of Clamp Pressure Applied
As clamp pressure increases, the pile density increases. As discussed in 2, above, more
dense materials are harder to cut. This presents a dilemma. Higher clamping pressures are
used to reduce draw when cutting with large angle bevels. While higher bevel angles
increase the lifetime of the k
nife, high pressure clamping increases the material’s density and
detracts from knife life. As a result, a compromise must be made between knife life and cut
quality.
8.1.5 Helpful Suggestions
If your shop is large enough to purchase more than one set of knives, the following
suggestions may be helpful. A set consists of 3 knives, one in the machine, one back up,
and one at the grinder.
If you cut a variety of stocks (easy and hard to cut), purchase two sets of knives. One set
should be beveled at around 21
0
and the other around 23
0
.
Use the smaller angle bevel to cut softer stocks at lower clamping pressures. Begin by
cutting the most pure, easy to cut stocks. As the knife dulls, begin cutting the less pure of the
softer stocks.
Use the larger bevel to cut harder more dense stocks at higher clamping pressures. Begin by
cutting the softer and most pure of the hard stocks. Then move to cutting the harder and less
pure of the hard stocks.
Summary of Contents for CHAMPION 370 TC
Page 10: ...5 0 Footprint 10 5 0 Footprint...
Page 12: ...6 0 Installation Setup 12 Figure 2 Figure 3...
Page 22: ...7 0 Operation 22 NOTES...
Page 56: ...10 0 MAIN ASSEMBLIES 56 10 0 MAIN ASSEMBLIES 10 1 Main Assembly Front view 49300 Sh t 1 Rev A...
Page 57: ...10 0 MAIN ASSEMBLIES 57 10 2 Main Assembly Side View 49300 Sh t 2 Rev A...
Page 58: ...10 0 MAIN ASSEMBLIES 58 10 3 Main Assembly Top View 49300 Sh t 3 Rev A...
Page 59: ...10 0 MAIN ASSEMBLIES 59 10 4 Main Assembly Rear View 49300 Sh t 4 Rev A...
Page 60: ...10 0 MAIN ASSEMBLIES 60 10 5 Main Assembly Clamp 49300 Sh t 5 Rev A...
Page 61: ...10 0 MAIN ASSEMBLIES 61 Main Assembly Clamp 49300 Sh t 5 Rev A cont d...
Page 62: ...10 0 MAIN ASSEMBLIES 62 10 6 Main Assembly Knife 49300 Sh t 6 Rev A...
Page 63: ...10 0 MAIN ASSEMBLIES 63 10 7 Main Assembly Table 49300 Sh t 7 Rev A...
Page 64: ...10 0 MAIN ASSEMBLIES 64 Main Assembly Table 49300 Sh t 7 Rev A cont d...
Page 65: ...10 0 MAIN ASSEMBLIES 65 Main Assembly Table 49300 Sh t 7 Rev A cont d...
Page 66: ...10 0 MAIN ASSEMBLIES 66 10 8 Main Assembly Table 49300 Sh t 8 Rev A...
Page 67: ...10 0 MAIN ASSEMBLIES 67 10 9 Main Assembly Hydraulics 49300 Sh t 9 Rev A...
Page 68: ...10 0 MAIN ASSEMBLIES 68 10 10 Main Assembly Final Asm Wiring w Fuses 49300 Sheet 10 Rev A...
Page 70: ...10 0 MAIN ASSEMBLIES 70 10 12 Main Assembly 380 415 460 Wiring w Fuses 49300 Sh t 11 rev A...
Page 71: ...10 0 MAIN ASSEMBLIES 71 Main Assembly 380 415 460 Wiring w Fuses 49300 Sh t 11 rev A cont d...
Page 73: ...10 0 MAIN ASSEMBLIES 73 Main Assembly 380 415 460V Wiring w Circuit Breakers cont...
Page 74: ...10 0 MAIN ASSEMBLIES 74 10 14 Main Assembly Hydraulic Cover 49300 Sh t 12 rev A...
Page 75: ...10 0 MAIN ASSEMBLIES 75 10 15 Main Assembly Parts List 49300 Sh t 13 Rev M...
Page 76: ...10 0 MAIN ASSEMBLIES 76 10 16 Main Assembly Parts List 49300 Sh t 14 Rev B...
Page 77: ...10 0 MAIN ASSEMBLIES 77 10 17 Main Assembly Parts List 49300 Sh t 15 Rev E...
Page 82: ...11 0 ELECTRICAL AND SCHEMATICS 82 Power Panel Asm 208 230V 3ph w Fuses EE 3479 SH T 2 REV H...
Page 92: ...11 0 ELECTRICAL AND SCHEMATICS 92 11 8 Interconnection Diagram TC Spacer E 3463 1 rev A...
Page 93: ...12 0 Hydraulics 93 12 0 Hydraulics 12 1 Hydraulic Manifold Assembly H 512 1 Rev C...
Page 94: ...12 0 Hydraulics 94 12 2 Hydraulic Manifold H 468 3 REV C...
Page 95: ...12 0 Hydraulics 95 Hydraulic Schematic Parts List H 468 3 Rev C cont...
Page 96: ...12 0 Hydraulics 96 12 3 Hydraulic Pressure Switch Assembly 49195 Rev B...
Page 97: ...13 0 SUB ASSEMBLIES 97 13 0 SUB ASSEMBLIES 13 1 Air Extension Table Option 49157 Rev A...
Page 98: ...13 0 SUB ASSEMBLIES 98 13 2 Air Table Blower Assembly Single Phase 49083 Rev D...
Page 99: ...13 0 SUB ASSEMBLIES 99 13 3 Clamp Compressor Assembly 47645 1 Rev F...
Page 100: ...13 0 SUB ASSEMBLIES 100 13 4 Knife Latch Assembly 49228 1 Rev B...
Page 101: ...13 0 SUB ASSEMBLIES 101 13 5 Paper Deflector Assembly 49115 Rev H...
Page 103: ...13 0 SUB ASSEMBLIES 103 NOTES...
Page 104: ...13 0 SUB ASSEMBLIES 104 13 7 Controls Asm Cut Switch Main Disconnect EE 3383 Rev D STANDARD...
Page 105: ...13 0 SUB ASSEMBLIES 105 Controls Asm Cut Switch Main Disc EE 3383 Rev D Cont...
Page 107: ...13 0 SUB ASSEMBLIES 107 Controls Asm Touch Switch Main Disc Cont EE 3383 1 Rev A Sheet 1...
Page 111: ...13 0 SUB ASSEMBLIES 111 NOTES...
Page 112: ...13 0 SUB ASSEMBLIES 112 13 12 Label Power Panel Connection Procedure w Fuses S 1781 211 Rev A...
Page 114: ...13 0 SUB ASSEMBLIES 114 13 14 Warning Label S 1781 116...
Page 115: ...13 0 SUB ASSEMBLIES 115 13 15 Jogging Aid Construction Guide A 12608 Rev D...
Page 117: ...14 0 Safety System Tests 117 NOTES...
Page 118: ...F 370 C December 2018...