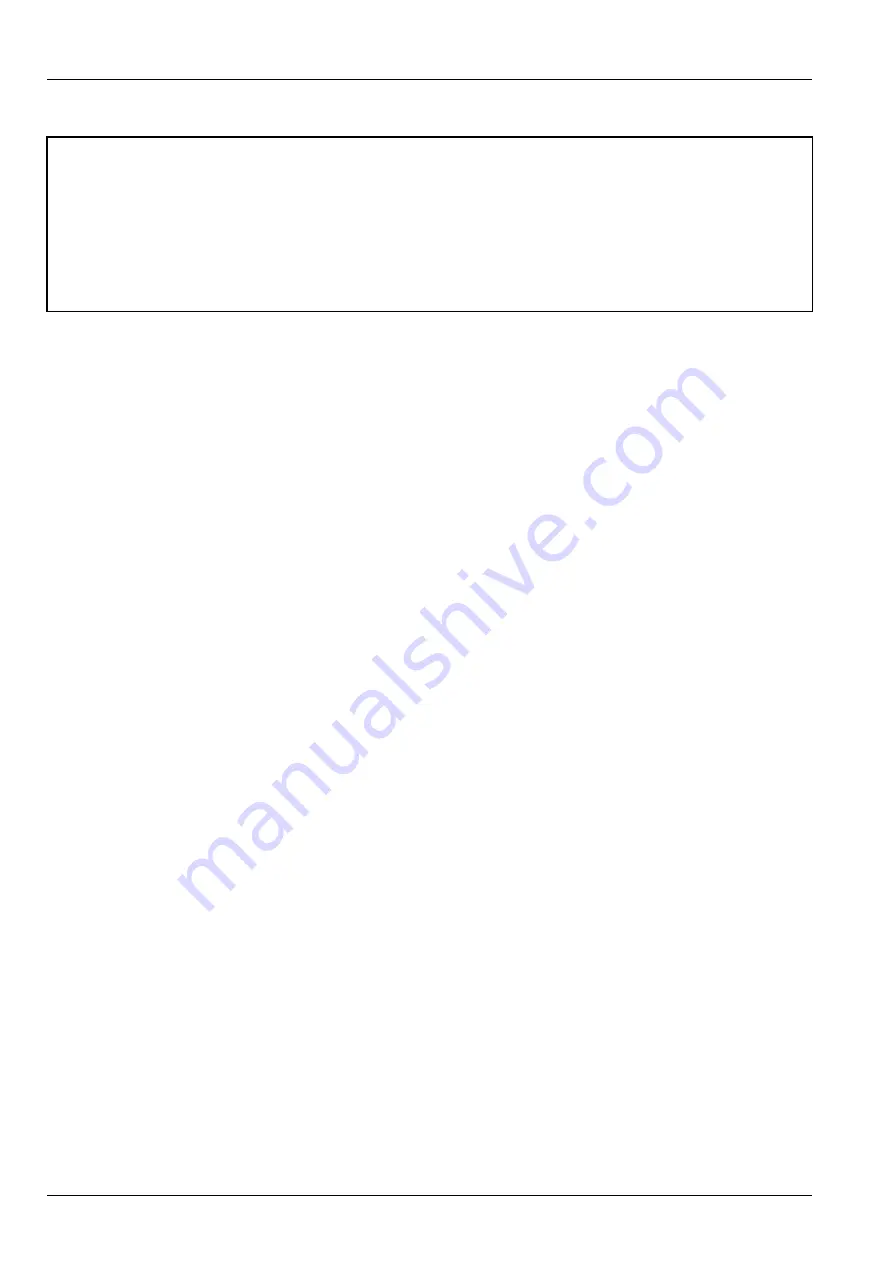
1 - GENERAL INFORMATION
Safety rules
CALIFORNIA
PROPOSITION 65 WARNING
Diesel engine exhaust and some of its constituents
are known to the State of California to cause cancer,
birth defects and other reproductive harm.
Battery post, terminals and related accessories
contain lead and lead compounds.
Wash hands after handling
1-2
Summary of Contents for CX300C
Page 6: ......
Page 18: ...1 GENERAL INFORMATION 1 12...
Page 28: ...2 SAFETY INFORMATION QNTTT2 011B_TU 3 2 10...
Page 50: ...2 SAFETY INFORMATION 2 32...
Page 130: ...3 CONTROLS INSTRUMENTS 3 80...
Page 157: ...4 OPERATING INSTRUCTIONS 4 Operate the arm control to unhook the tool KKZVLU 024A 14 4 27...
Page 172: ...4 OPERATING INSTRUCTIONS 4 42...
Page 182: ...5 TRANSPORT OPERATIONS 5 10...
Page 272: ...6 MAINTENANCE 6 90...
Page 280: ...8 SPECIFICATIONS Working range 4M8ORU 002A 2 See next page for the values 8 6...
Page 282: ...8 SPECIFICATIONS 8 8...