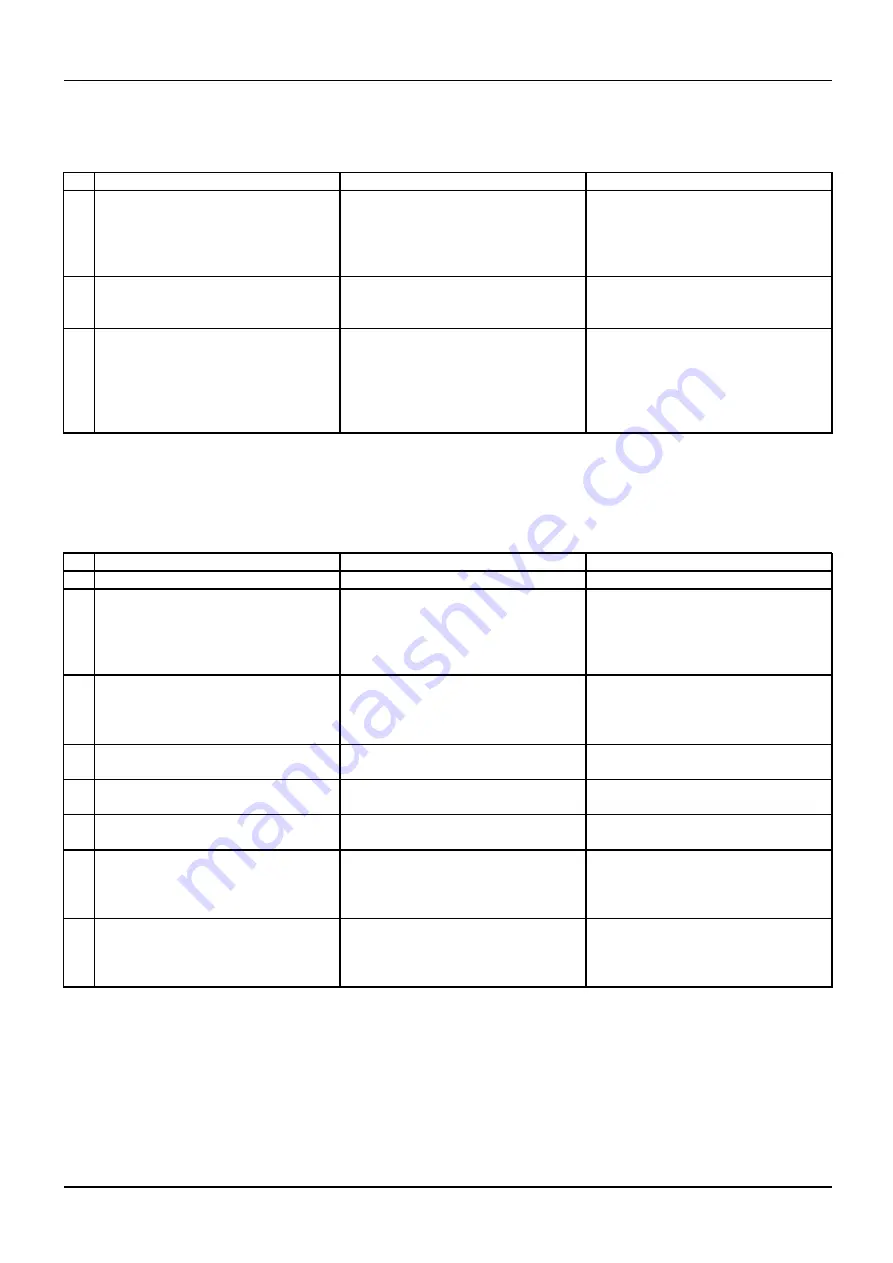
DISTRIBUTION SYSTEMS - LIGHTING SYSTEM
Turn/hazard light Turn switch - Testing (A.40.A.13.83 - G.40.A.20)
435, 445, 445CT
NOTE:
For wiring diagram refer to
Wiring harness - Electrical schematic frame 20 (A.30.A.88 - C.20.E.20)
N°
Test Point
Expected Result
Other Result (Possible Cause)
1 Turn the key switch to the ON
position.
Terminal for wire 759A (P) to ground.
12 volts
Check the circuit between the
fl
asher switch and the 10 amp fuse
in the options fuse block. Also check
the 10 amp fuse in the options fuse
block
2 Place the hazard switch on the ON
position.
Terminal for wire 758B (P) to ground.
12 volts
Bad hazard switch.
3 If the readings are correct and the
indicator lamp on the hazard switch
does not illuminate, proceed to the
following test.
Terminal for wire 178BM (B) to
ground.
Continuity
Bad ground circuit for hazard switch
indicator lamp.
If the readings are correct and the
indicator lamp on the hazard switch
doe not illuminate, replace the
hazard switch.
Turn/hazard light Flasher unit - Testing (A.40.A.13.86 - G.40.A.20)
435, 445, 445CT
NOTE:
For wiring diagram refer to
Wiring harness - Electrical schematic frame 20 (A.30.A.88 - C.20.E.20)
N°
Test Point
Expected Result
Other Result (Possible Cause)
1 Terminal for wire 178FA to ground. Continuity
Bad ground circuit.
2 Turn the key switch to the ON
position.
Terminal for wire 751FA (R) to
ground.
12 volts
Check the circuit between the
fl
asher and the 10 amp fuse in the
options fuse block. Also check the
10 amp fuse in the options fuse
block.
3 Place the hazard switch in the ON
position.
Terminal for wire 758FA (P) to
ground.
Intermittent 12 volts
Check the circuit between the
fl
asher and the
fl
asher switch. Also
check the
fl
asher switch.
4 Terminal for wire 757FA (P) to
ground.
Intermittent 12 volts
Bad
fl
asher.
Check diode in diode pack.
5 Terminal for wire 756FA (P) to
ground.
Intermittent 12 volts
Bad
fl
asher.
Check diode in diode pack.
6 Terminal for wire 759FO (P) to
ground.
Intermittent 12 volts
Bad
fl
asher.
7 Place the turn signal switch in the
left turn position.
Terminal for wire 756 to ground.
Intermittent 12 volts
Check the circuit between the
fl
asher and the turn signal switch.
Also check the turn signal switch.
Bad
fl
asher.
8 Place the turn signal switch in the
right turn position.
Terminal for wire 757 to ground.
Intermittent 12 volts
Check the circuit between the
fl
asher and the turn signal switch.
Also check the turn signal switch.
Bad
fl
asher.
1 04/05/2005
A.40.A / 4
Summary of Contents for 435
Page 1: ...REPAIR MANUAL 435 445CT 445 6 75491 1 04 05 2005 ...
Page 3: ...INTRODUCTION 6 75491 1 04 05 2005 1 ...
Page 15: ...INTRODUCTION bs04e020_1 4 6 75491 1 04 05 2005 13 ...
Page 16: ...INTRODUCTION bs04e021_1 5 6 75491 1 04 05 2005 14 ...
Page 19: ...REPAIR MANUAL DISTRIBUTION SYSTEMS 435 445CT 445 39702 1 04 05 2005 A ...
Page 86: ...39703 1 04 05 2005 A 10 A 66 ...
Page 104: ...39704 1 04 05 2005 A 12 A 18 ...
Page 126: ...39705 1 04 05 2005 A 16 A 22 ...
Page 127: ...DISTRIBUTION SYSTEMS A ELECTRICAL POWER SYSTEM 30 A 435 445CT 445 39706 1 04 05 2005 A 30 A 1 ...
Page 237: ...DISTRIBUTION SYSTEMS A LIGHTING SYSTEM 40 A 435 445CT 445 39707 1 04 05 2005 A 40 A 1 ...