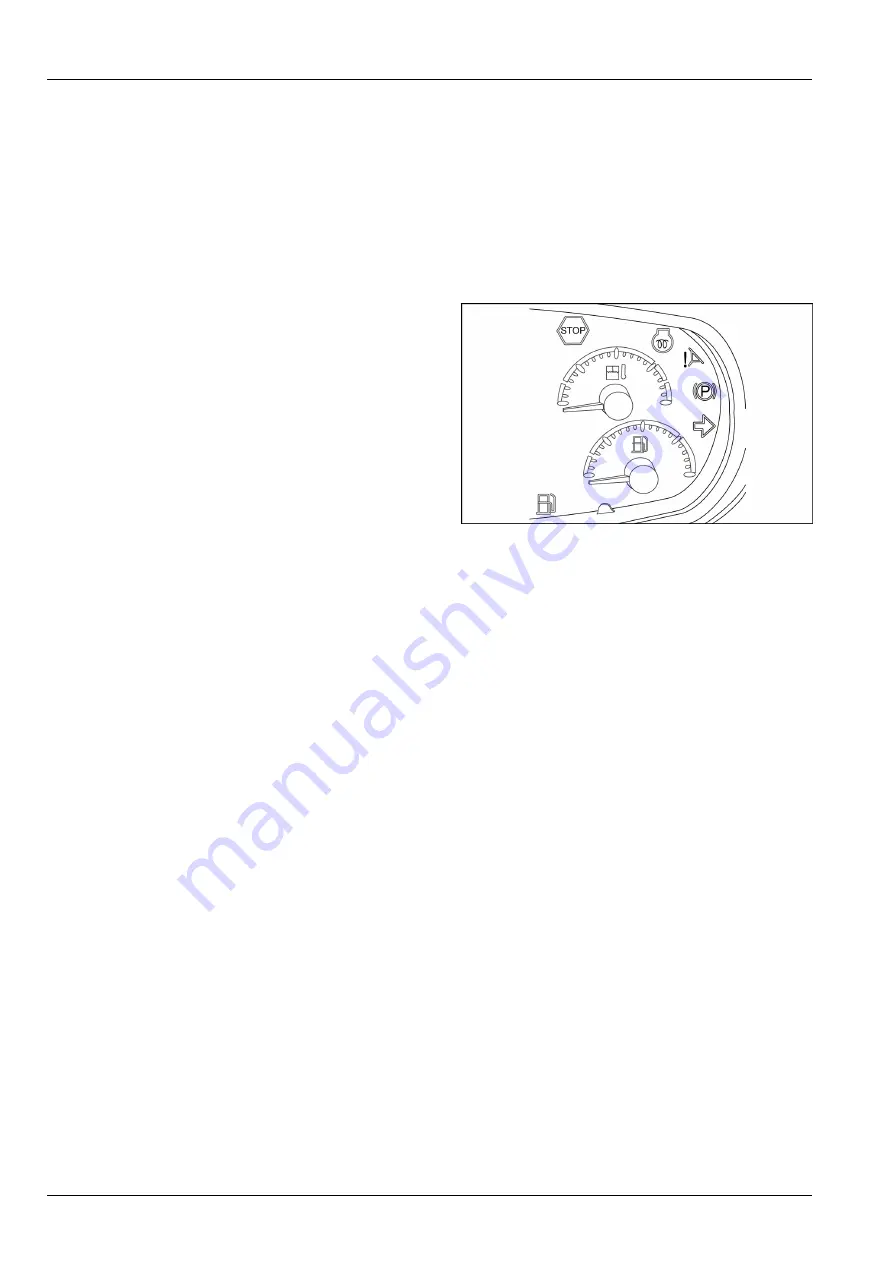
7 - MAINTENANCE
Secondary Steering (optional) [60637076]
The secondary steering system is electrically powered. This system allows you to steer the machine if the primary
steering system stops working. Maintain the batteries to assure the system will function.
Check the secondary steering when the hour meter reads 250 hours or any time electronic warnings may so indicate.
Prior operation:
Keep all non-authorized personnel clear of the area. Park the machine on hard packed level ground with enough
clearance around the machine to allow complete steering from side to side. Raise the bucket approximately
500 mm
(
19.7 in
) above the ground.
1. With the key switch on and the engine off, confirm the
secondary steering light within the cluster is on. This
indicates the steering pressure is low.
2. Start the machine and let the engine run for a few sec-
onds. Confirm the secondary steering light is out after
the first few seconds. This confirms the electrical func-
tion of the circuit is operating correctly and adequate
pressure has built. The secondary steering module is
now functional.
3. With the machine at low idle and steering straight
ahead, turn the key switch to the OFF position to stop
the engine. Immediately turn the key back to the ON
position (not start position). The secondary steering
pump/motor should start running. Confirm the light is
on and the motor is running.
4. Steer the machine full left and then full right to confirm
that the secondary steering pump is working. Confirm
there is no lack of steering function.
5. Look at the instrument cluster to verify that the sec-
ondary steering light comes on.
NOTICE:
Do not run the secondary steering pump/motor
continuously for more than 20 seconds at a time without a
2 minute cool down.
6. Restart the engine. Confirm the secondary steering
light stays on. The secondary steering motor should
stop after approximately 3 seconds and the secondary
steering light should go out.
7. If steps
2
through
6
function properly, the secondary
steering is operating correctly. If not, repair and retest.
If you have any problems with this procedure, call your
dealer.
RCIL10WHL178BAL
1
NOTE:
Do not turn the ignition off if the machine is turned against either the right hand or left hand steering stop. The
steering wheel may kick back.
7-94
Summary of Contents for 1021F
Page 1: ...Wheel Loader Print No 47557863 2st edition English 05 14 Operator s Manual Tier 2 1121F 1021F ...
Page 20: ...1 GENERAL INFORMATION 1 14 ...
Page 52: ...2 SAFETY INFORMATION LEEN11T0046GA 20 33 Tie down point decal 34 Lifting point decal 2 32 ...
Page 54: ...2 SAFETY INFORMATION LEEN14T0049GA 23 38 Decal fuses 39 Decal fuses and relays 2 34 ...
Page 56: ...2 SAFETY INFORMATION LEEN11T0137GA 26 42 Tie down point decal 43 Decal fuses and relays 2 36 ...
Page 57: ...2 SAFETY INFORMATION LEEN11T0138GA 27 44 Decal Maximum Speed 45 Reflector 2 37 ...
Page 65: ...2 SAFETY INFORMATION Empty tool LEEN11T0024AA 20 2 45 ...
Page 66: ...2 SAFETY INFORMATION 2 46 ...
Page 125: ...3 CONTROLS AND INSTRUMENTS Software legend RCPH10WHL910FAH 11 3 59 ...
Page 138: ...3 CONTROLS AND INSTRUMENTS 3 72 ...
Page 180: ...5 TRANSPORT OPERATIONS 5 10 ...
Page 192: ...6 WORKING OPERATIONS 6 12 ...
Page 203: ...7 MAINTENANCE Hydraulic Brake system temperature range LEIL12WHL0012BA 3 7 11 ...
Page 301: ...7 MAINTENANCE LEEN14T0133HA 5 The fuse decal is located inside the access door 7 109 ...
Page 310: ...7 MAINTENANCE 7 118 ...
Page 312: ...8 SPECIFICATIONS Voltage 24 V 8 2 ...
Page 326: ...8 SPECIFICATIONS NOTE Refer to country regulation foreseen for exceptional vehicles 8 16 ...
Page 328: ...8 SPECIFICATIONS NOTE Refer to country regulation foreseen for exceptional vehicles 8 18 ...
Page 330: ...8 SPECIFICATIONS NOTE Refer to country regulation foreseen for exceptional vehicles 8 20 ...
Page 332: ...8 SPECIFICATIONS NOTE Refer to country regulation foreseen for exceptional vehicles 8 22 ...
Page 334: ...8 SPECIFICATIONS NOTE Refer to country regulation foreseen for exceptional vehicles 8 24 ...
Page 336: ...8 SPECIFICATIONS NOTE Refer to country regulation foreseen for exceptional vehicles 8 26 ...
Page 338: ...8 SPECIFICATIONS NOTE Refer to country regulation foreseen for exceptional vehicles 8 28 ...
Page 340: ...8 SPECIFICATIONS NOTE Refer to country regulation foreseen for exceptional vehicles 8 30 ...
Page 342: ...8 SPECIFICATIONS NOTE Refer to country regulation foreseen for exceptional vehicles 8 32 ...
Page 344: ...8 SPECIFICATIONS NOTE Refer to country regulation foreseen for exceptional vehicles 8 34 ...
Page 346: ...8 SPECIFICATIONS NOTE Refer to country regulation foreseen for exceptional vehicles 8 36 ...
Page 348: ...8 SPECIFICATIONS NOTE Refer to country regulation foreseen for exceptional vehicles 8 38 ...
Page 350: ...8 SPECIFICATIONS NOTE Refer to country regulation foreseen for exceptional vehicles 8 40 ...
Page 352: ...8 SPECIFICATIONS NOTE Refer to country regulation foreseen for exceptional vehicles 8 42 ...
Page 354: ...8 SPECIFICATIONS NOTE Refer to country regulation foreseen for exceptional vehicles 8 44 ...
Page 356: ...8 SPECIFICATIONS NOTE Refer to country regulation foreseen for exceptional vehicles 8 46 ...
Page 360: ...8 SPECIFICATIONS 8 50 ...