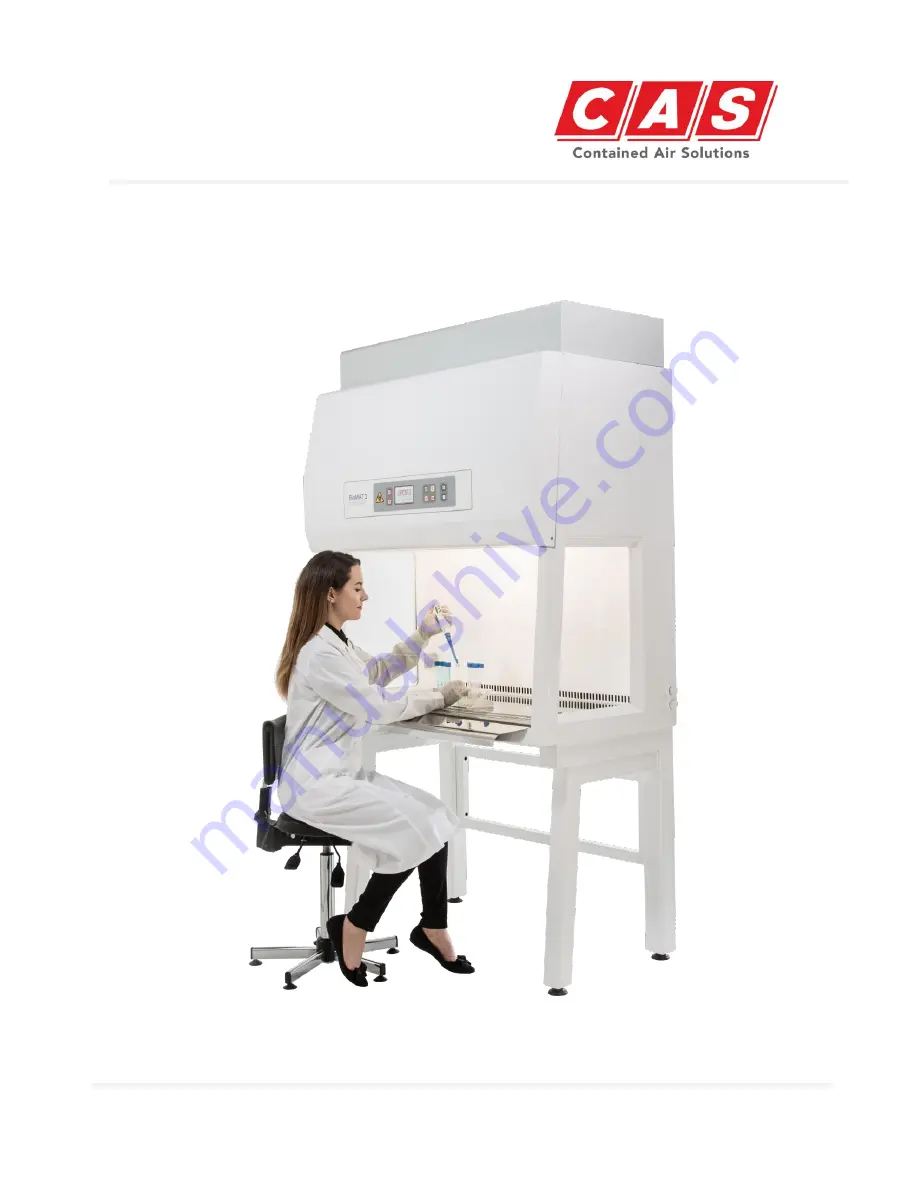
Contained Air Solutions Ltd | Unit 4 Greengate | Middleton Junction | Manchester M24 1RU |
T +44 (0)161-655-8860 | F +44 (0)161-655-8865
[email protected] | www.containedairsolutions.co.uk
We reserve the right to change specification without notice. © 2016 Contained Air Solutions Ltd
BioMAT 2-
S2
Summary of Contents for BioMAT 2-S2
Page 35: ...Wiring Diagram 5 3 ...