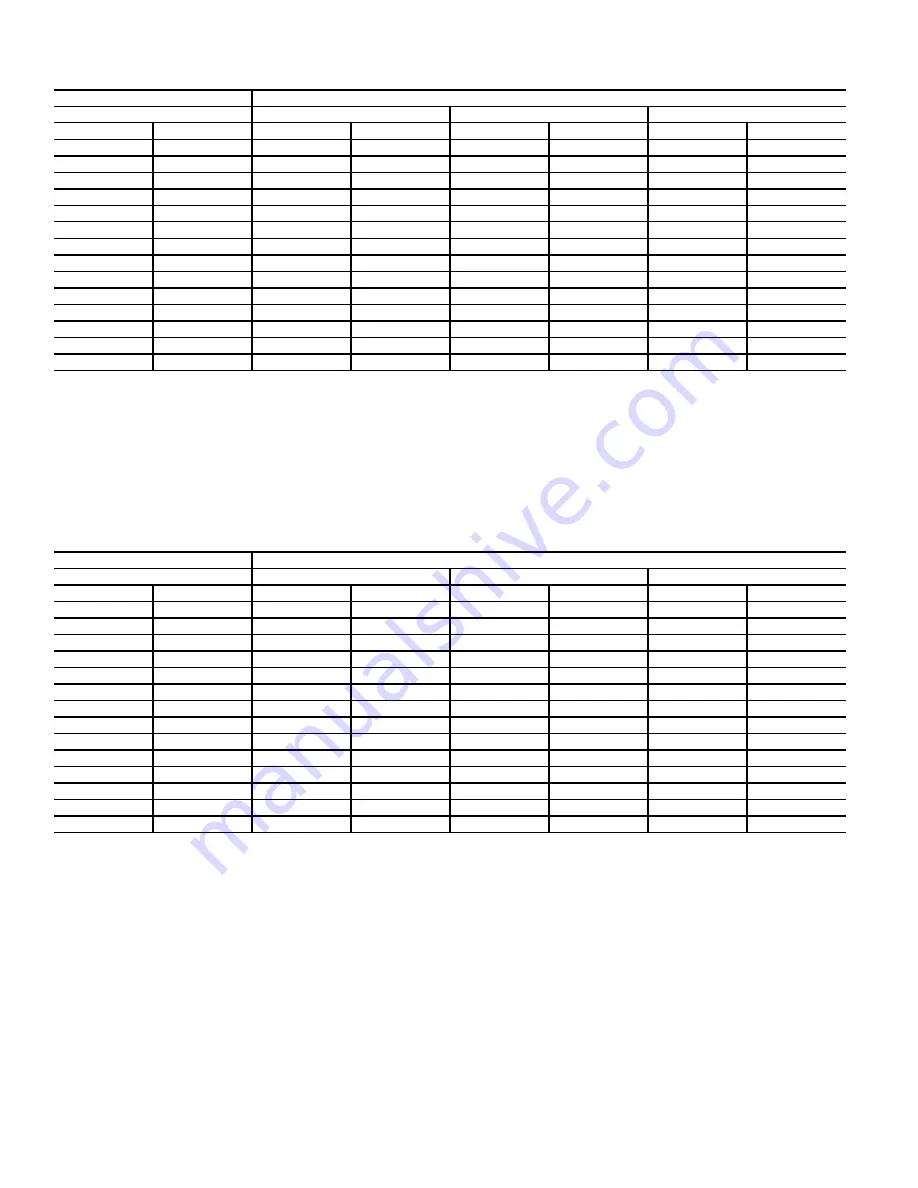
42
* As the height above sea level increases, there is less oxygen per cubic ft. of air. Therefore, heat input rate should be reduced at higher altitudes.
* As the height above sea level increases, there is less oxygen per cubic ft. of air. Therefore, heat input rate should be reduced at higher altitudes.
Table 16 — Altitude Compensation* (17-30) for Natural Gas
NATURAL GAS
NOMINAL HEAT INPUT
ELEVATION
220k BTUH
310k BTUH
400k BTUH
Feet
Meters
Orifice Size
Input (btu/hr)
Orifice Size
Input (btu/hr)
Orifice Size
Input (btu/hr)
0-2000
0-610
30
220,000
30
310,000
30
400,000
2000
610
30
202,400
30
285,200
30
368,000
3000
914
31
1
193,600
31
1
272,800
31
1
352,000
4000
1219
31
1
184,800
31
1
260,400
31
1
336,000
5000
1524
31
1
176,000
31
1
248,000
31
1
320,000
6000
1829
31
1
167,200
31
1
235,600
31
1
304,000
7000
2134
32
1
158,400
32
1
223,200
32
1
288,000
8000
2438
32
1
149,600
32
1
210,800
32
1
272,000
9000
2743
34
1
140,800
34
1
198,400
34
1
256,000
10,000
3048
35
2
132,000
35
2
186,000
35
2
240,000
11,000
3353
37
2
123,200
37
2
173,600
37
2
224,000
12,000
3658
37
2
114,400
37
2
161,200
37
2
208,000
13,000
3962
39
2
105,600
39
2
148,800
39
2
192,000
14,000
4267
39
2
96,800
39
2
136,400
39
2
176,000
KIT NO.:
XX
1
= CRNGELEV001A00
XX
2
= CRNGELEV002A00
XX
3
= CRLPELEV005A00
XX
4
= CRLPELEV006A00
XX
5
= CRLPKIT9001A00
Table 17 — Altitude Compensation* (17-30) for Propane Gas
PROPANE GAS
NOMINAL HEAT INPUT
ELEVATION
220k BTUH
310k BTUH
400k BTUH
Feet
Meters
Orifice Size
Input (btu/hr)
Orifice Size
Input (btu/hr)
Orifice Size
Input (btu/hr)
0-2000
0-610
48
5
220,000
48
5
310,000
48
5
400,000
2000
610
49
3
202,400
49
3
285,200
49
3
368,000
3000
914
49
3
193,600
49
3
272,800
49
3
352,000
4000
1219
49
3
184,800
49
3
260,400
49
3
336,000
5000
1524
50
3
176,000
50
3
248,000
50
3
320,000
6000
1829
50
3
167,200
50
3
235,600
50
3
304,000
7000
2134
50
3
158,400
50
3
223,200
50
3
288,000
8000
2438
51
3
149,600
51
3
210,800
51
3
272,000
9000
2743
51
3
140,800
51
3
198,400
51
3
256,000
10,000
3048
52
4
132,000
52
4
186,000
52
4
240,000
11,000
3353
52
4
123,200
52
4
173,600
52
4
224,000
12,000
3658
53
4
114,400
53
4
161,200
53
4
208,000
13,000
3962
53
4
105,600
53
4
148,800
53
4
192,000
14,000
4267
53
4
96,800
53
4
136,400
53
4
176,000
KIT NO.:
XX
1
= CRNGELEV001A00
XX
2
= CRNGELEV002A00
XX
3
= CRLPELEV005A00
XX
4
= CRLPELEV006A00
XX
5
= CRLPKIT9001A00
Summary of Contents for WeatherMaster Puron 48HC D17
Page 18: ...18 COOLING CHARGING CHARTS Fig 22 Cooling Charging Chart 15 Ton ...
Page 19: ...19 Fig 23 Cooling Charging Chart 17 5 Ton ...
Page 20: ...20 Fig 24 Cooling Charging Chart 20 Ton ...
Page 21: ...21 Fig 25 Cooling Charging Chart 25 Ton ...
Page 37: ...37 Fig 48 Unit Control Box IGC Location IGC Board IGC Board Side view Front view ...
Page 40: ...40 Fig 51 Typical IGC Wiring Diagram ...
Page 46: ...46 Fig 57 RTU Open Overlay for Economizer Wiring ...
Page 47: ...47 Fig 58 VFD Overlay for W2770 Controller Wiring ...
Page 84: ...84 Fig B 48HC D17 D28 Control Diagram 208 230 3 60 460 575 3 60 ...
Page 85: ...85 Fig C 48HC D17 D28 Power Diagram 208 230 3 60 ...
Page 86: ...86 Fig D 48HC D17 D28 Power Diagram 460 3 60 ...
Page 87: ...87 Fig E 48HC D17 D28 Power Diagram 575 3 60 ...
Page 88: ...88 Fig F 48HC D17 D28 Control Diagram with Humidi MiZer System ...
Page 89: ...89 Fig G 48HC D17 D28 Power Diagram 208 230 3 60 with Humidi MiZer System ...
Page 90: ...90 Fig H 48HC D17 D28 Power Diagram 460 3 60 with Humidi MiZer System ...
Page 91: ...91 Fig I 48HC D17 D28 Power Diagram 575 3 60 with Humidi MiZer System ...
Page 92: ...92 Fig J PremierLink System Control Wiring Diagram 50HE500891 F ...
Page 93: ...93 Fig K PremierLink System Control Wiring Diagram with Humidi MiZer System ...
Page 94: ...94 Fig L RTU OPEN Wiring Diagram ...
Page 95: ...95 Fig M RTU OPEN Wiring Diagram with Humidi MiZer System ...
Page 97: ......