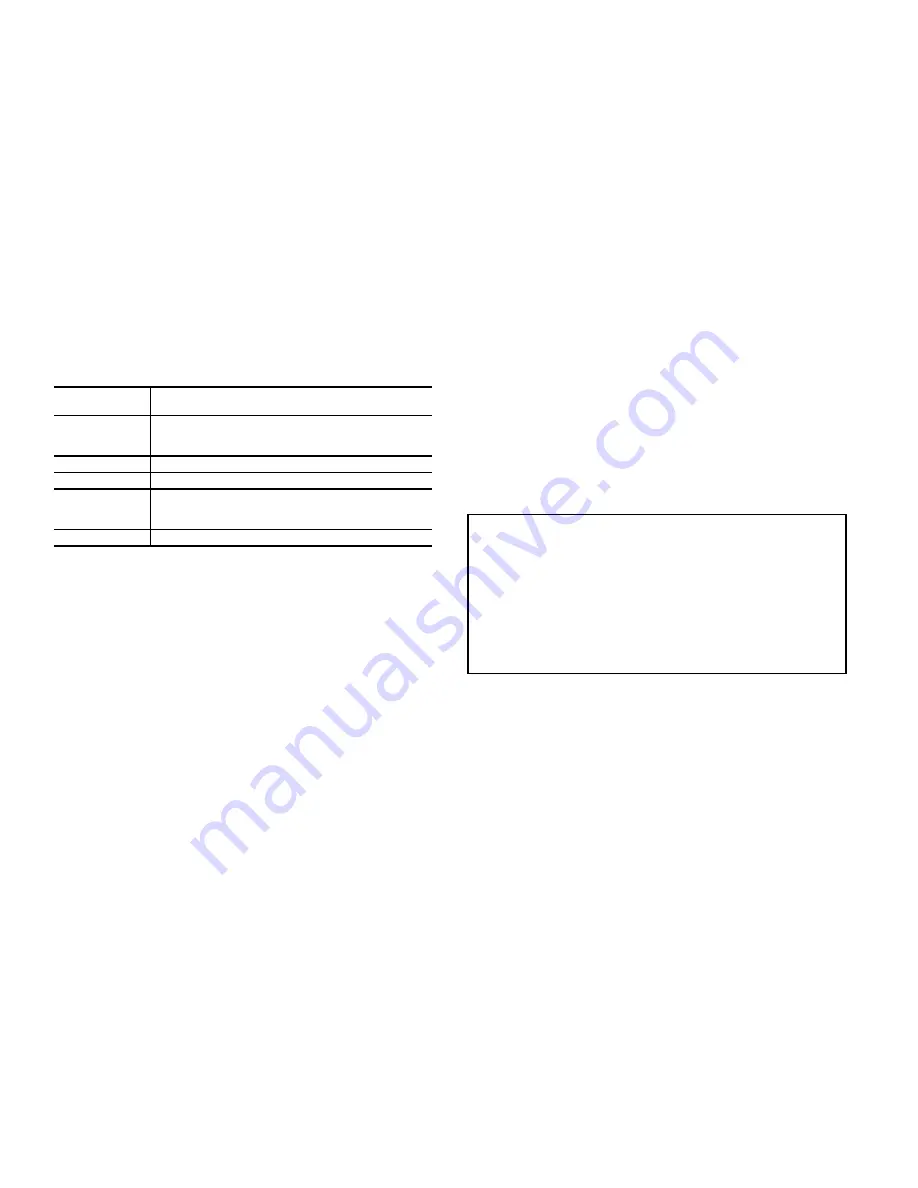
30
the suction line near the compressor. The switch is stem-
mounted. Trip setting is 54 psig ± 5 psig (372 ± 34 kPa). Reset
is automatic at 117 ± 5 psig (807 ± 34 kPa).
EVAPORATOR FREEZE PROTECTION
The system is protected against evaporator coil frosting and
low temperature conditions by a temperature switch mounted
on the evaporator coil hairpin. Trip setting is 30°F ± 5°F (-1°C
± 3°C). Reset is automatic at 45°F (7°C).
SUPPLY (INDOOR) FAN MOTOR PROTECTION
Disconnect and lockout power when servicing fan motor.
The standard supply fan motor is equipped with internal over-
current and over-temperature protection. Protection devices re-
set automatically.
The high static option supply fan motor is equipped with a pi-
lot-circuit Thermix combination over-temperature/over-current
protection device. This device resets automatically. Do not by-
pass this switch to correct trouble. Determine the cause and
correct it.
Table 8 — Detector Indicators
CONDENSER FAN MOTOR PROTECTION
The condenser fan motor is internally protected against over-
temperature.
Relief Device
A soft solder joint at the suction service access port provides
pressure relief under abnormal temperature and pressure condi-
tions (i.e., fire in building). Protect this joint during brazing op-
erations near this joint.
Control Circuit, 24-V
The control circuit is protected against overcurrent conditions
by a circuit breaker mounted on control transformer TRAN.
Reset is manual.
PremierLink™ Control
For details on operating units equipped with the factory-in-
stalled PremierLink controller option, refer to the
PremierLink
Retrofit Rooftop Controller Version 3.x Installation, Start-Up,
and Configuration Instructions
manual.
RTU Open Control System
For details on operating units equipped with the factory-in-
stalled RTU Open controller, refer to the
“Factory-Installed
RTU Open Multi-Protocol Controller Control, Start-Up, Oper-
ation and Troubleshooting”
manual.
ECONOMIZER SYSTEMS
The unit may be equipped with a factory-installed or accessory
(field-installed) economizer system. Three types are available:
with a logic control system (EconoMi$er IV and EconoMi$er X)
and without a control system (EconoMi$er2). See Fig. 60-62 for
component locations on each type. See Fig. 63-66 for economiz-
er section wiring diagrams. The W7212 controller is used for
EconoMi$er IV and the W7220 controller is used for
EconoMi$er X. See Table 9 for EconoMi$er IV input and output
logic.
All three economizers use direct-drive damper actuators.
CONTROL OR
INDICATOR
DESCRIPTION
Magnetic test/
reset switch
Resets the sensor when it is in the alarm or trouble
state. Activates or tests the sensor when it is in the
normal state.
Alarm LED
Indicates the sensor is in the alarm state.
Trouble LED
Indicates the sensor is in the trouble state.
Dirty LED
Indicates the amount of environmental
compensation used by the sensor (flashing
continuously = 100%)
Power LED
Indicates the sensor is energized.
IMPORTANT: Any economizer that meets the economizer
requirements as laid out in California’s Title 24 mandatory
section 120.2 (fault detection and diagnostics) and/or pre-
scriptive section 140.4 (life-cycle tests, damper leakage,
5 year warranty, sensor accuracy, etc), will have a label on
the economizer. Any economizer without this label does
not meet California’s Title 24. The five year limited parts
warranty referred to in section 140.4 only applies to factory
installed economizers. Please refer to your economizer on
your unit.
Summary of Contents for WeatherMaster 50HC04
Page 32: ...32 Fig 63 RTU Open Overlay for Economizer Wiring ...
Page 33: ...33 Fig 64 VFD Overlay for W2770 Controller Wiring ...
Page 86: ...86 Fig C 50HC A07 PAC Control Diagram 208 230 3 60 460 575 3 60 APPENDIX D WIRING DIAGRAMS ...
Page 91: ...91 Fig H 50HC D12 PAC Control Diagram 208 230 3 60 460 575 3 60 APPENDIX D WIRING DIAGRAMS ...
Page 93: ...93 Fig J 50HC A04 A06 PAC Power Diagram 208 230 1 60 APPENDIX D WIRING DIAGRAMS ...
Page 95: ...95 Fig L 50HC A07 PAC Power Diagram 208 230 3 60 460 3 60 575 3 60 APPENDIX D WIRING DIAGRAMS ...
Page 100: ...100 Fig Q 50HC D11 PAC Power Diagram 208 230 3 60 APPENDIX D WIRING DIAGRAMS ...
Page 101: ...101 Fig R 50HC D11 PAC Power Diagram 460 3 60 575 3 60 APPENDIX D WIRING DIAGRAMS ...
Page 103: ...103 Fig T 50HC D14 PAC Power Diagram 208 230 3 60 APPENDIX D WIRING DIAGRAMS ...
Page 104: ...104 Fig U 50HC D14 PAC Power Diagram 460 3 60 575 3 60 APPENDIX D WIRING DIAGRAMS ...
Page 124: ...124 Fig AO PremierLink System A04 A06 Wiring Diagram APPENDIX D WIRING DIAGRAMS ...
Page 125: ...125 Fig AP RTU Open System Control A04 A06 Wiring Diagram APPENDIX D WIRING DIAGRAMS ...
Page 126: ...126 Fig AQ PremierLink System A07 D14 Wiring Diagram APPENDIX D WIRING DIAGRAMS ...
Page 127: ...127 Fig AR RTU Open A07 D14 Wiring Diagram APPENDIX D WIRING DIAGRAMS ...