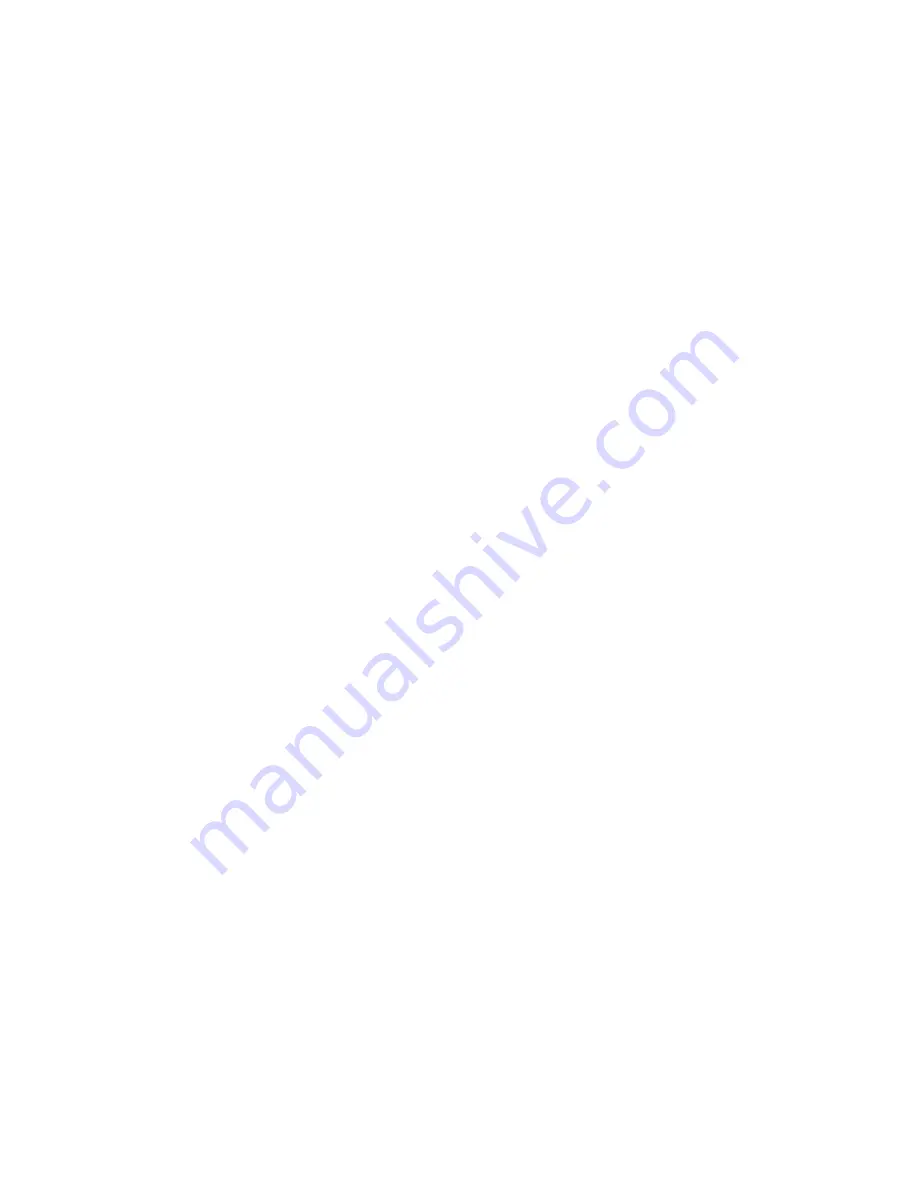
32
The sensors and configurations that automatically turn on this
board are:
Configuration
UNIT
SFS.M
= 1 (Supply Fan Status
Switch Monitoring)
Configuration
EDT.R
RES.S
= Enable (4 to 20 mA Sup-
ply Air Reset Sensor Enable)
Configuration
DMD.L
DM.L.S
= 1 (2 SWITCHES) (De-
mand Limiting using 2 discrete switches)
Configuration
DMD.L
DM.L.S
= 2 (4-20 MA CTRL)
(Demand Limiting using a 4 to 20 mA sensor)
Configuration
IAQ
AQ.CF
IQ.I.C
= 1 (IAQ DIS-
CRETE) (IAQ discrete switch control)
Configuration
IAQ
AQ.CF
IQ.I.C
= 2 (IAQ
DISC.OVR) (IAQ discrete switch “override” control)
Configuration
IAQ
AQ.CF
OQ.A.C
= 1 (OAQ
SENS-DAQ) (Outdoor Air Quality Sensor)
Configuration
IAQ
AQ.CF
OQ.A.C
= 2 (4-20 NO
DAQ) (4 to 20 mA sensor, no DAQ)
Temperature Compensated Start Cooling Factor (TCS.C)
This factor is used in the equation of the Temperature Compen-
sated Start Time Bias for cooling. Refer to the Temperature
Compensated Start section on page 76 for more information. A
setting of 0 minutes indicates Temperature Compensated Start
in Cooling is not permitted.
Temperature Compensated Start Heating Factor (TCS.H)
This factor is used in the equation of the Temperature Compen-
sated Start Time Bias for heating. Refer to the Temperature
Compensated Start section for more information. A setting of 0
minutes indicates Temperature Compensated Start in Heating
is not permitted.
Fan Fail Shuts Downs Unit (SFS.S)
This configuration will determine whether the unit should shut
down on a supply fan status fail or simply alert the condition
and continue to run. If set to YES, then the control will shut
down the unit and send out an alarm if supply fan status moni-
toring fails. If set to NO, the control will not shut down the unit
if supply fan status monitoring fails but the control will send
out an alert.
Fan Status Monitoring (SFS.M)
This configuration selects the type of fan status monitoring to
be performed.
0 - NONE — No switch or monitoring
1 - SWITCH — Use of the fan status switch
2 - SP RISE — Monitoring of the supply duct pressure
VAV Unoccupied Fan Retry Time (VAV.S)
Machine control types 1 and 2 (VAV-RAT,VAV-SPT) monitor
the return-air temperature during unoccupied periods to deter-
mine if there is a valid demand for heating or cooling before ini-
tiating an unoccupied heating or cooling mode. If the routine
runs but concludes a valid demand condition does not exist, then
the process is not permitted for the period of time defined by this
configuration. Reducing this value allows a more frequent re-
sampling process. Setting this value to zero will prevent any
sampling sequence.
Unit Size (SIZE)
There are several unit sizes (tons) for the A Series control. Make
sure this configuration matches the size called out by the model
number of the unit. This is important as the cooling stage tables
are directly determined based on this configuration.
Discharge Pressure Transducers (DP.XR)
This configuration configures the unit for use with discharge
pressure transducers. The 48/50A units will be automatically
configured for discharge pressure transducers and
DP.XR
should be set to Yes.
Suction Pressure Transducer Type (SP.XR)
This configuration specifies the type of suction pressure trans-
ducer that is being used. Set
SP.XR
to 0 for support of a pressure
transducer with a range of 0 to 135 psig. Set
SP.XR
to 1 for sup-
port of a pressure transducer with a range of 0 to 200 psig.
NOTE: The 48/50A units do not require a change to the
SP.XR
factory default setting.
Refrigerant Type (RFG.T)
This configuration specifies the type of refrigerant used in the
unit. Configuration
RFG.T
is set to 0 if the refrigerant used is
R-22. Configuration
RFG.T
is set to 1 if the refrigerant used is
R-410A. Do not change this setting.
Condenser Type (CND.T)
This configuration specifies the type of condenser installed in
the unit. Configuration
CND.T
is set to 0 if the condenser is a
round tube, plate fin coil (RTPF). Configuration
CND.T
is set
to 1 if the condenser is a microchannel heat exchanger coil
(MCHX).
MAT Calc Config (MAT.S)
This configuration gives the user three options in the process-
ing of the mixed-air temperature (MAT) calculation:
•
MAT.S
= 0
There will be no MAT calculation.
•
MAT.S
= 1
The control will attempt to learn MAT over time. Any time the
system is in a vent mode and the economizer stays at a particu-
lar position for long enough, MAT is set to equal EDT. Using
this, the control has an internal table whereby it can more
closely determine the true MAT value.
•
MAT.S
= 2
The control will not attempt to learn MAT over time.
To calculate MAT linearly, the user should reset the MAT table
entries by setting
MAT.R
to YES. Then set
MAT.S
= 2
. The con-
trol will calculate MAT based on the position of the economizer,
outside-air temperature, and return-air temperature.
To freeze the MAT table entries, let the unit run with
MAT.S
= 1
.
Once sufficient data has been collected, change
MAT.S
= 2
. Do
not reset the MAT table.
Reset MAT Table Entries? (MAT.R)
This configuration allows the user to reset the internally stored
MAT learned configuration data back to the default values. The
defaults are set to a linear relationship between the economizer
damper position and OAT and RAT in the calculation of MAT.
MAT Outside Air Position Default (MAT.D)
This configuration is used to calculate MAT when the econo-
mizer option is disabled. The configuration is adjustable from
0 to 100% outside air. This defines the fixed ventilation posi-
tion that will be used to correctly calculate MAT.
Altitude……..In Feet: (ALTI)
The control does not include a barometric pressure sensor to deter-
mine altitude. The altitude must be defined the calculation of en-
thalpy and cfm. The altitude parameter is used to set up a default
barometric pressure for use with calculations. The effect of baro-
metric pressure in these calculations is not great, but could have an
effect depending on the installed elevation of the unit. If the unit is
installed at a particularly high altitude and enthalpy or cfm are be-
ing calculated, set this configuration to the current elevation.
Summary of Contents for WEATHERMAKER 48A2020
Page 112: ...112 Fig 20 Typical Main Control Box Wiring Schematic 48 50A Units ...
Page 113: ...113 Fig 21 Typical Auxiliary Control Box Wiring Schematic ...
Page 114: ...114 Fig 22 Typical 2 Stage Gas Heat Wiring Schematic Size 060 Units Shown ...
Page 115: ...115 Fig 23 Typical Staged Gas Heat Wiring Schematic Size 060 Units Shown TO NEXT PAGE ...
Page 116: ...116 Fig 23 Typical Staged Gas Heat Wiring Schematic Size 060 Units Shown cont ...
Page 117: ...117 Fig 24 Typical Electric Heat Control Schematic 50 Series Size 060 Units Shown ...
Page 118: ...118 Fig 25 Typical Controls Option Wiring Schematic SW1 SW2 OR DEHUMIDIFY SWITCH ...
Page 119: ...119 Fig 26 Typical Power Schematic 48 50A2 A3 A4 A5 060 Unit Shown ...
Page 120: ...120 Fig 27 Typical Power Schematic of Greenspeed Low Ambient Option 48 50A 060 Unit Shown ...
Page 121: ...121 Fig 28 Typical Small Chassis Component Location Size 020 035 Units ...
Page 122: ...122 Fig 29 Typical Large Chassis Component Locations Size 040 060 Units ...
Page 185: ...185 APPENDIX C VFD INFORMATION cont Fig F Internal Enclosure Fan Replacement A48 7716 ...