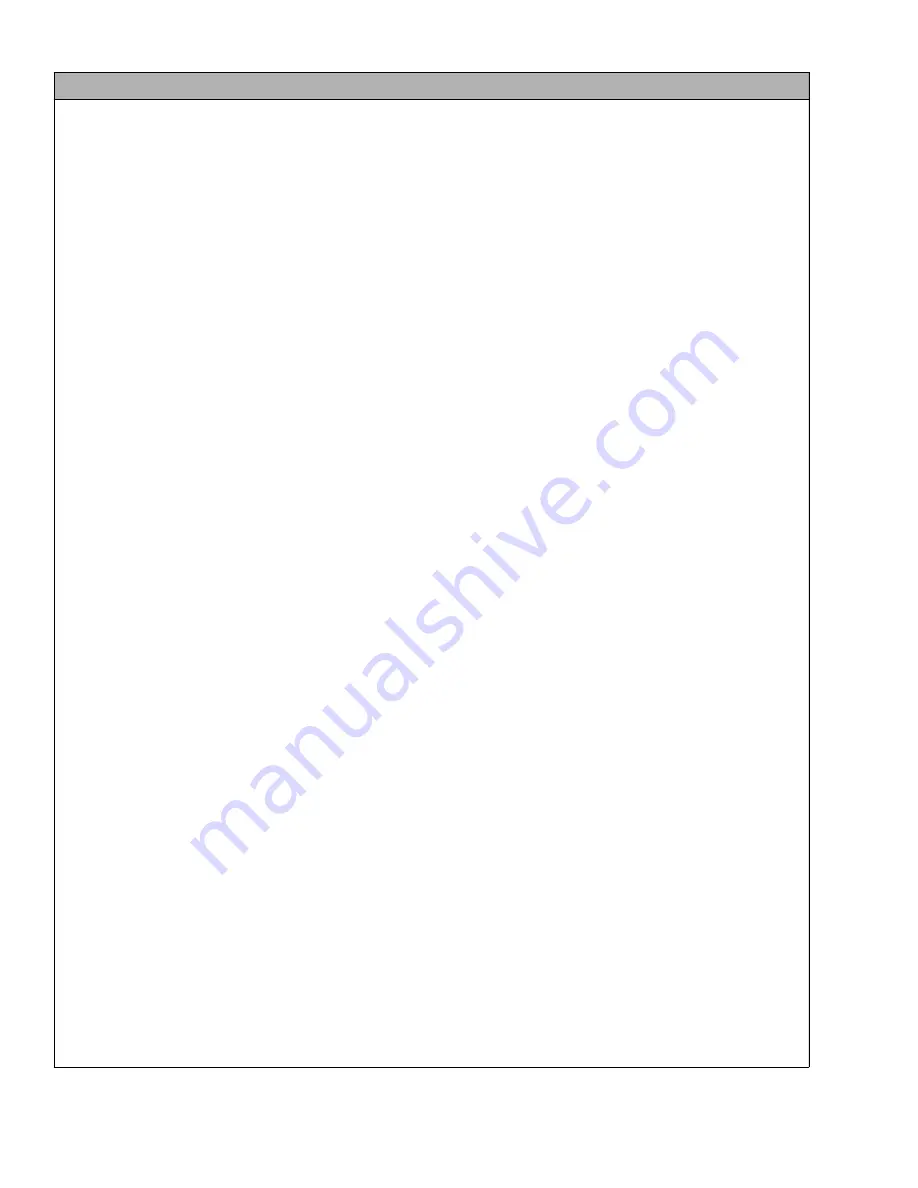
62-11637
7–10
00018
LOW REFRIGERANT PRESSURE
• ACTIVATION: The compressor is operating with the suction pressure less than -3 psig (-0.20 bar) for more
than the LP SHUTDOWN DELAY Configuration (up to 5 minutes) with RAT above -10°F (-23.3°C) or less
than -8 psig (-0.53 bar) with RAT at any temperature.
• UNIT CONTROL: Alarm only or (if configured for shutdown) shutdown and alarm.
• RESET CONDITION: Auto reset after 15 minutes if suction pressure is more than -2 psig (-0.13 bar) or
alarm may be manually reset using the display mounted keys or by turning the unit OFF, then ON again.
NOTE: Follow the steps below until a problem is found. Once a repair or correction has been made, the active
alarm should clear itself (refer to reset condition above). Operate the unit through the appropriate modes to see if
any active alarm occurs. Continue with the steps below as necessary.
CORRECTIVE ACTIONS:
1.
Check Airflow Through Evaporator Coil/Section
a. Inspect coil. Ninety percent or more of the coil surface must be undamaged. Coil must be clean.
b. Check airflow (with unit running). Even airflow through the entire coil. No “dead” spots.
c. Check return air bulkhead, air chute. Good air flow. Return air not restricted. Air chute in good condition.
d. Check fan clutch. Must be fully engaged.
e. Check upper and lower fan belt tension & condition. Verify no glazing, cracking, or slipping. Refer to
. Replace if required.
2.
Check Refrigerant Charge
Refer to
3.
Check System Pressures
Install manifold gauge set and check and compare compressor discharge, suction and evaporator out-
let pressure to the Unit Data readings. Suction pressure must be above
−
3 psig (
−
0.2 bar). Refer to
for instruction on comparison.
4.
Manually Defrost
Unit
Defrost unit and terminate automatically. Typical defrost cycle time is 5-20 minutes. Visually verify that
all ice is cleared from evaporator coil.
5.
Perform Pretrip Check
Clear Active Alarm list, then run Pretrip & check for any new alarms. Any active alarms must be cor-
rected and cleared before proceeding.
6.
Check Unloader Operation
Check Front (UL1) and Rear (UL2) Unloaders. Refer to Alarm
and
.
7.
Check Compressor Suction Modulation Valve
(CSMV)
Check compressor suction modulation valve. Refer to
8.
Check Expansion Valve
(EVXV)
Check operation of the EVXV. Refer to
.
9.
Visually Inspect Unit
Visually inspect unit for damage to the liquid line causing a restriction or any signs of temperature drop
at the drier. Verify all tubing from the receiver to the evaporator section is in good condition. Verify
there is no temperature drop at the drier or anywhere on the liquid line.
Summary of Contents for Transicold X4 7300
Page 21: ...62 11637 1 6 1 3 SAFETY DECALS ...
Page 22: ...1 7 62 11637 62 03958 ...
Page 23: ...62 11637 1 8 ...
Page 24: ...1 9 62 11637 ...
Page 119: ...62 11637 SECTION 6 MESSAGECENTER PARAGRAPH NUMBER Page 6 1 MESSAGECENTER MESSAGES 6 1 ...
Page 278: ......