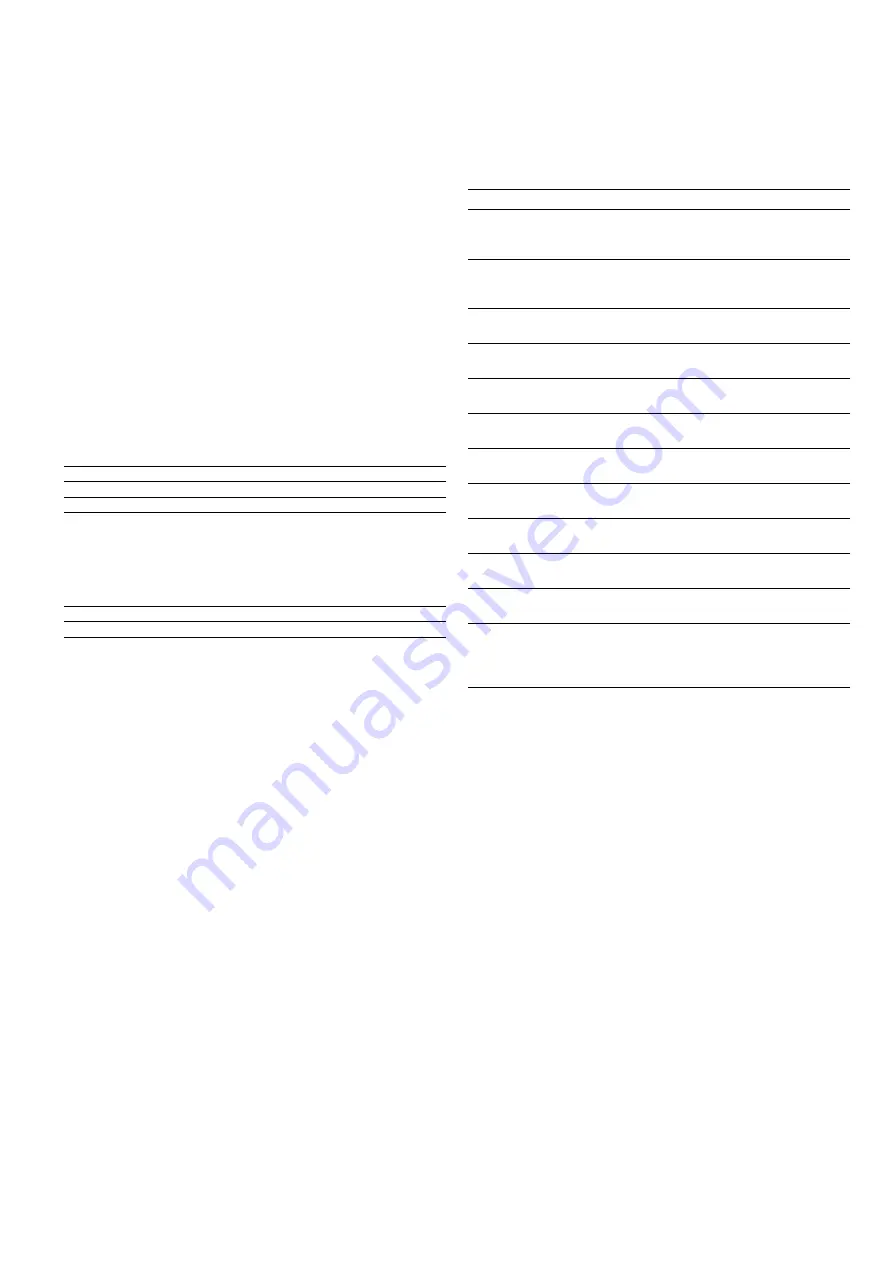
33
8.14 - Circuit capacity loading sequence
This function determines in which order the circuit capacity
is changed. Compressor loading is based on compressor
control.
Two types of compressor loading sequences are available
and can be configured by setting the Loading Sequence
parameter [seq_typ] via the Touch Pilot user interface
(GEN_CONF).
•
Balanced loading sequence (“seq_typ” set to “no”):
The control maintains equal capacity between both
circuits as the machine loads and unloads. The lag circuit
can be started when the pre-defined capacity of the lead
circuit is reached, i.e. 50% by default.
•
Staged loading sequence (“seq_typ” set to “yes”):
The control loads the lead circuit completely before
the lag circuit is started. When the load is decreasing,
the lag circuit is unloaded first.
To set loading sequence
1. Navigate to the Configuration menu.
2. Select
General Configuration
(GEN_CONF).
3. Set
Staged Loading Sequence
[seq_typ].
Staged Loading Sequence [seq_typ]
no = Equal loading sequence
yes = Staged loading sequence = Circuit B priority
To set capacity required to start the second circuit
1. Navigate to the Configuration menu.
2. Select
General Configuration
(GEN_CONF).
3. Set
Cap. to start 2nd cir
[transcap].
Cap. to start 2nd cir [transcap]
30 to 80%
50%
8.15 - Master/Slave assembly (option 58)
Two units can be linked to create the master/slave assembly.
The master unit can be controlled locally, remotely or by
network commands. Master/slave assembly must be validated
in order to start the master/slave chiller operation.
All control commands to the master/slave assembly (start/
stop, setpoint selection, load shedding, etc.) are handled by
the unit which is configured as the master. The commands
are transmitted automatically to the slave unit. If the master
chiller is turned off while the master/slave function is active,
then the slave chiller will be stopped. Under certain
circumstances, the slave unit may be started first to balance
the run times of the two units.
In the event of a communication failure between the two
units, each unit will return to an autonomous operating mode
until the fault is cleared. If the master unit is stopped due to
an alarm, the slave unit is authorised to start.
NOTE:
Master/slave assembly can be configured only by
Carrier service technicians.
8.16 - Energy Management Module (option 156)
The energy management module (EMM) enables to control
the level of energy consumption, providing users with
information such as current unit status, compressors
operating status, etc.
This option requires the installation of an additional SIOB
board.
Description
Connector
Remarks
Occupancy override
control
DI-01, 77-78
If the contact is closed in
Remote mode, the unit goes
into the occupied mode
Demand limit switch 2 DI-02, 73A-74A If the contact is closed,
the second capacity limit
switch is active
Customer interlock
DI-03, 34A-35A Permits immediate unit
shutdown (Remote mode only)
Ice storage
DI-04, 75-76
If the contact is closed, the unit
enters the ice storage mode
Space temperature
AI-01, 71A-72A Active setpoint reset via space
temperature control
Capacity limit control
AI-10, 67-68
Active setpoint reset via unit
capacity control (4-20 mA)
Compressor A
DO-01,
37A1-38A1
Output active if compressor A
is operating
Compressor B
DO-02,
37B1-38B1
Output active if compressor B
is operating
Chiller shutdown
DO-06, 30-31
Output closed when the unit
is stopped due to an alarm
Alert
DO-05,
30B-31B
Output closed when the alert
has been tripped
Chiller running or
ready to start
DO-04,
37A-38A
Output closed when the chiller
is ready to start or running
Unit capacity
AO-01, 78+-79- Capacity running output
(0 to 10 VDC),
0V = 0% capacity and
10V = 100% capacity
DI = Digital Input; DO = Digital Output, AI = Analogue Input; AO = Analogue Output
Summary of Contents for TOUCHPILOT 30KAV
Page 1: ...CONTROLS MANUAL Original document Touch Pilot Control 30KAV ...
Page 43: ......