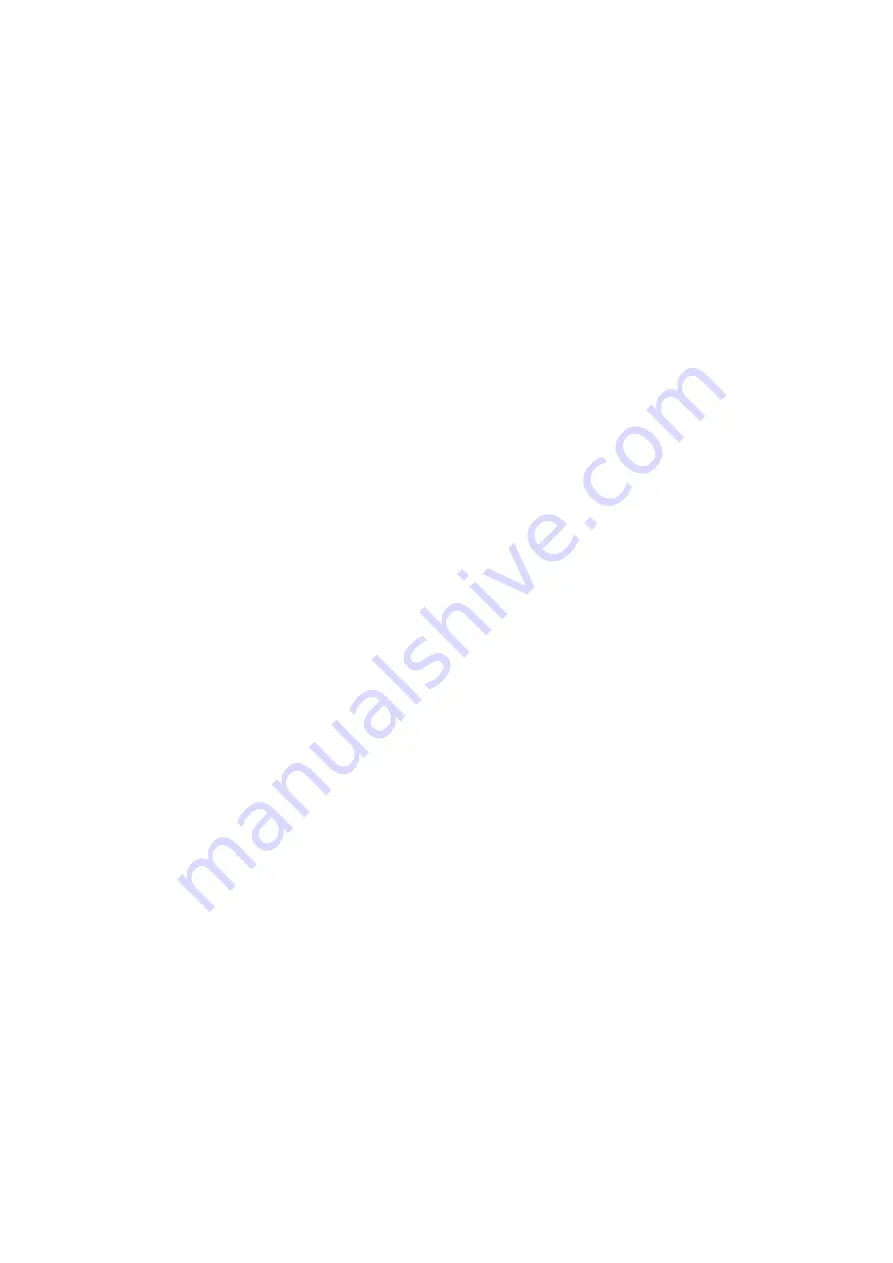
6
1.
SAFETY CONSIDERATIONS
19DV centrifugal liquid chillers are designed to provide safe and reliable service when operated within design
specifications. When operating this equipment, use good judgment and safety precautions to avoid damage to
equipment and property or injury to personnel. Be sure you understand and follow the procedures and safety
precautions contained in the machine instructions, as well as those listed in this guide.
To find out, if these products comply with European directives (machine safety, low voltage, electromagnetic
compatibility, equipment under pressure, etc.) check the declarations of conformity for these products.
1.1 Installation safety considerations
In certain cases the safety relief valves are installed on ball valves. These ball valves are factory-supplied lead-sealed
in the open position. This system permits isolating and removing the safety relief valves for checking and replacing.
The safety relief valves are designed and installed to ensure protection against fire risk. Removing the safety relief
valves is only permitted if the fire risk is fully controlled and the responsibility of the user.
All factory-installed safety valves are lead-sealed to prevent any calibration change. If a safety stop is removed for
checking or replacement please ensure that there is always an active safety stop on each of the reversing valves
installed in the unit.
The safety valves must be connected to discharge pipes. These pipes must be installed in a way that ensures that
people and property are not exposed to refrigerant leaks. These fluids may be diffused in the air, but far away from
any building air intake, or they must be discharged in a quantity that is appropriate for a suitably absorbing
environment.
The set pressure of a relief valve that has leaked is generally lower than its original setting. The new setting may
affect the operating range. To avoid nuisance tripping or leaks, replace or re-set the valve.
DANGER: Do not vent refrigerant relief valves within a building. Outlet from relief valve must be vented outdoors.
The accumulation of refrigerant in an enclosed space can displace oxygen and cause asphyxiation.
Provide adequate ventilation, especially for enclosed and low overhead spaces. Inhalation of high concentrations of
vapour is harmful and may cause heart irregularities, unconsciousness, or death. Misuse can be fatal. Vapour is
heavier than air and reduces the amount of oxygen available for breathing. Product causes eye and skin irritation.
Decomposition products are hazardous.
Do not use oxygen to purge lines or to pressurize a machine for any purpose. Oxygen gas reacts violently with oil,
grease, and other common substances. Never exceed specified test pressures, verify the allowable test pressure by
checking the instruction literature and the design pressures on the equipment nameplate.
Do not use air for leak testing. Use only refrigerant or dry Nitrogen.
Do not valve off any safety device. Be sure that all pressure relief devices are properly installed before operating the
machine.
1.2 Maintenance safety considerations
Engineers working on the electric or refrigeration components must be authorized, trained and fully qualified to do
so. All refrigerant circuit repairs must be carried out by a trained person, fully qualified to work on these units. He
must have been trained and be familiar with the equipment and the installation. All welding operations must be
carried out by qualified specialists.
During maintenance operations (such as a refrigerant charge transfer or pumpdown) or leak repairs, that can result
in a significant pressure loss of saturated evaporation pressure, the qualified technician must ensure that the heat
exchanger water pumps continue to operate to ensure a sufficient flow rate and prevent evaporator freeze-up. If
there is a fault, the chiller control is wired to automatically control the water pumps and the cooling tower fans to
guarantee independent machine frost protection. If for a specific installation water flow control and control of the
cooling towers must be done by another means, a parallel Carrier control must be put in place.
Any manipulation (opening or closing) of a shut-off valve must be carried out by a qualified and authorized
engineer. These procedures must be carried out with the unit shut-down.
During any handling, maintenance and service operations the engineers working on the unit must be equipped with
safety gloves, glasses, shoes and protective clothing.
Summary of Contents for PIC 5+
Page 26: ...26 VFD not shown Fig 13 Sensors actuators location ...
Page 52: ...52 Fig 24 19DV control box ...
Page 53: ...53 1 Power supply 24V AC 2 LEN 3 CCN 4 Ethernet 5 USB Fig 25 19DV HMI box rear view ...
Page 54: ...54 Fig 26 19DV IOB1 wiring Fig 27 19DV IOB2 wiring ...
Page 57: ...57 ...
Page 113: ...113 APPENDIX A SmartView SCREEN AND MENU STRUCTURE ...
Page 114: ...114 Detailed menu description ...
Page 116: ...116 APPENDIX B MAINTENANCE SUMMARY AND LOGSHEETS Cont 19DV monthly Maintenance Log ...