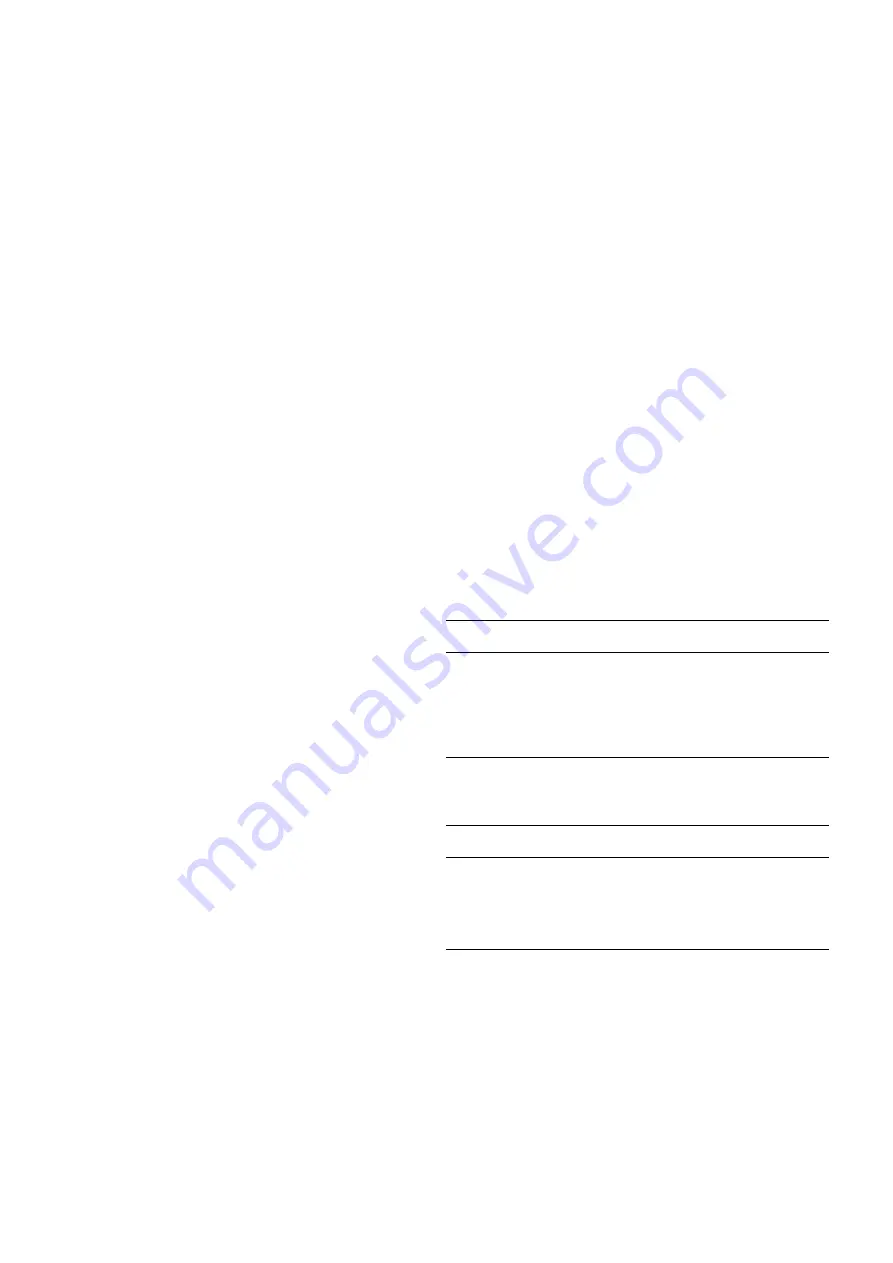
34
•
Check the unit operating parameters and compare them
with previous values,
•
Keep and maintain a maintenance sheet, attached to each
HVAC unit.
All these operations require strict observation of adequate
safety measures: individual protection garments, compliance
with all industry regulations, compliance with applicable
local regulations and using common sense.
12.3 - level 3 (or higher) maintenance (see note)
The maintenance at this level requires specific skills/approval/
tools and know-how and only the manufacturer, his represen-
tative or authorised agent are permitted to carry out these
operations. These maintenance operations concern for example:
•
A major component replacement (compressor, water heat
exchanger),
•
Any intervention on the refrigerant circuit (handling
refrigerant),
•
Changing of parameters set at the factory (application
change),
•
Removal or dismantling of the HVAC unit,
•
Any intervention due to a missed established maintenance
operation,
•
Any intervention covered by the warranty.
Note:
Any deviation or non-observation of these maintenance criteria will render
the guarantee conditions for the HVAC unit nul and void, and the manufacturer,
Carrier France, will no longer be held responsible.
12.4 - Tightening torques for the main electrical
connections
Component
Designation
value
in the unit
(Nm)
M12 screw on bus bar, customer connection
80
Soldered screw PE, customer connection
80
Tunnel terminal screw, fuse holder
Fu-
3-3.5
Tunnel terminal screw, compressor contactor
KM1-->KM12
3-4.5
Brass screw M6, compressor earth
EC-
5
Screw M6, compressor connection
EC-
5
Tunnel terminal screw, disconnects
QM-
0.8-1.2
Screw M6, earth power distribution
10
12.5 - Tightening torques for the main bolts and
screws
screw type
Used for
value
(Nm)
Metal screw D=4.8
Air heat exchanger, housing supports
4.2
Screw H M8
Air heat exchanger, compressor fixing
18
Taptite screw M10
Air heat exchanger, chassis - structure fixing
30
Taptite screw M6
Piping support, cowling
7
Screw H M8
Piping clip
12
Screw H M6
Piping clip
10
Nut H M10
Compressor chassis
30
12 - sTaNDaRD MaINTENaNCE
Air conditioning equipment must be maintained by professional
technicians, whilst routine checks can be carried out locally by
specialised technicians.
simple preventive maintenance will allow you to get the
best performance from your hvaC unit:
•
improved cooling performance
•
reduced power consumption
•
prevention of accidental component failure
•
prevention of major time-consuming and costly
interventions
•
protection of the environment
There are five maintenance levels for HVAC units, as defined
by the AFNOR X60-010 standard.
12.1 - level 1 maintenance (see note)
Simple procedure can be carried out by the user:
•
Visual inspection for oil traces (sign of a refrigerant leak),
•
Air heat exchanger (condenser) cleaning - see chapter ‘Air
heat exchanger coil - level 1’,
•
Check for removed protection devices, and badly closed
doors/covers,
•
Check the unit alarm report when the unit does not work*.
General visual inspection for any signs of deterioration.
12.2 - level 2 maintenance (see note)
This level requires specific know-how in the electrical, hydronic
and mechanical fields. It is possible that these skills are available
locally: existence of a maintenance service, industrial site,
specialised subcontractor.
In these cases, the following maintenance operations are
recommended.
Carry out all level 1 operations, then:
•
At least once a year tighten the power circuit electrical
connections**,
•
Check the correct operation of the differential switches
every six meonths
•
Check and retighten all control/command connections, if
required**,
•
Remove the dust and clean the interior of the control
boxes, if required,
•
Check the presence and the condition of the electrical
protection devices,
•
Check the correct operation of all heaters,
•
Replace the fuses every 3 years or every 15000 hours
(age-hardening),
•
Check the water connections,
•
Purge the water circuit (see chapter ‘Water flow control
procedure’),
•
Clean the water filter (see chapter ‘Water flow control
procedure’),
•
Fully clean the air heat exchangers with a low-pressure jet
and a bio-degradable cleaner (counter-current cleaning -
see chapter ‘Air heat exchanger coil - level 2),
•
Replace the stuffing box packing of the pump after 10000
hours of operation,
*
See report in the 30RB/RQ Pro-Dialog Plus control manual
** See table with tightening torques