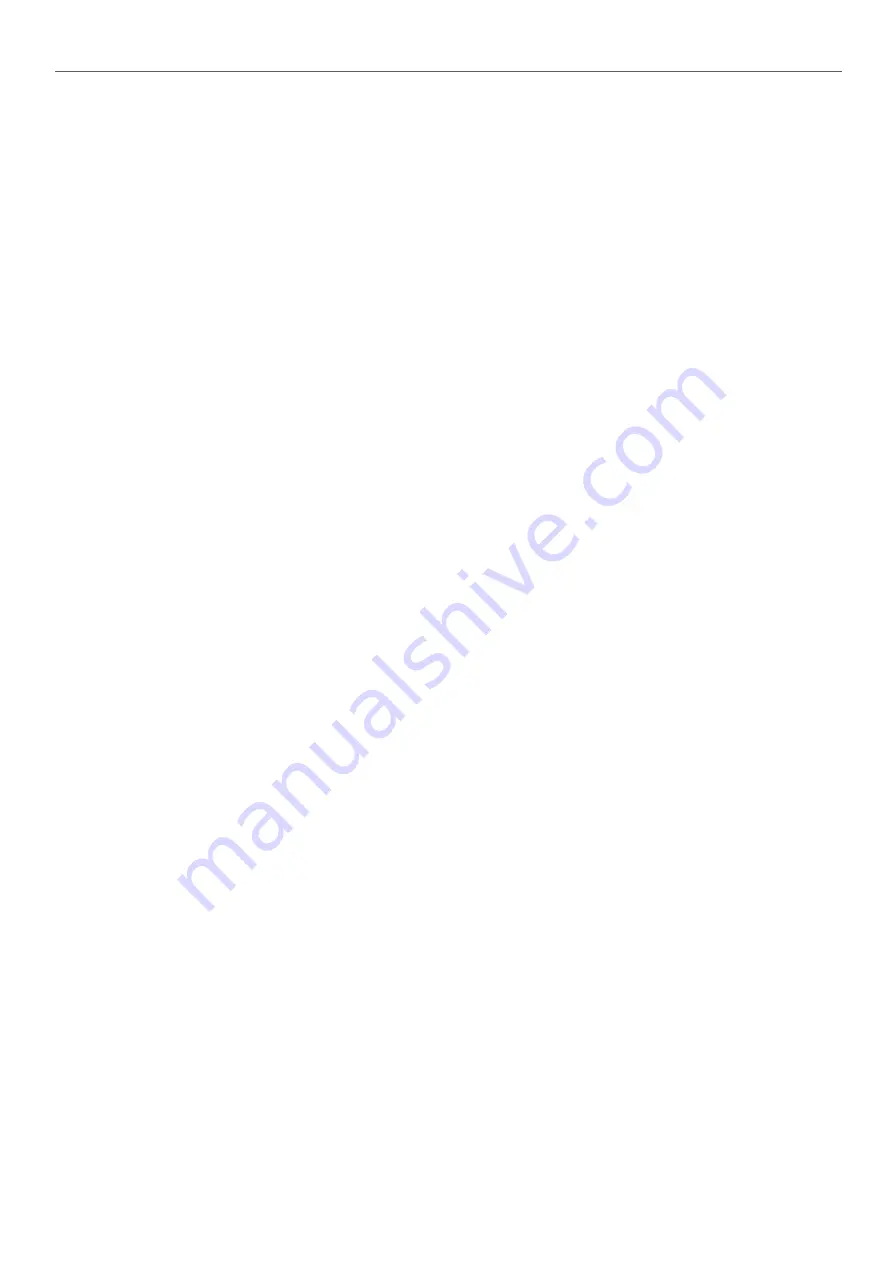
25
10 - MAJOR SYSTEM COMPONENTS AND OPERATION DATA
10.1 -
Direct-drive twin-screw compressor with
variable capacity slide valve
The unit uses 06T geared twin-screw compressors equipped with
a variable capacity slide valve for continuous control between 15%
or 30% and 100% of full load.
10.1.1 -
Oil filter
The 06T screw compressor has an independent oil filter.
10.1.2 - Refrigerant
The unit is a liquid chiller operating with refrigerant R-1234ze(E)
(standard) or R-515B (option 330).
10.1.3 -
Lubricant
The 06T screw compressor is approved for use with the following
lubricant: CARRIER MATERIAL SPEC PP 47-38.
10.1.4 -
Oil supply solenoid valve
An oil supply solenoid valve is installed on the oil return line as
standard to isolate the compressor from oil flow when the
compressor is not operating. The oil solenoid valve is field
replaceable.
10.1.5 -
Capacity control system
The 06T screw compressor has an unloading system that is
standard on all compressors. This unloading system consists of
slide valve that permits changing the length of the screw used for
the refrigerant compression. This valve is controlled by the action
of a piston controlled by two solenoid valves on the oil return line.
10.1.6 -
Suction valve (option 92)
An isolating valve can be added to ease maintenance on
compressor. This valve can be moved only without pressure
differential upstream and downstream of this valve.
10.2 -
Pressure vessels
General
Monitoring during operation, re-qualification, re-testing and re-
testing dispensation:
• Follow the regulations on monitoring pressurised equipment.
• It is normally required that the user or operator sets up and
maintains a monitoring and maintenance file.
• If no regulations exist or to complement regulations, follow
the control programmes of EN 378.
• If they exist follow local professional recommendations.
• Regularly inspect the condition of the coating (paint) to
detect blistering resulting from corrosion. To do this, check
a non-insulated section of the container or the rust formation
at the insulation joints.
• Regularly check for possible presence of impurities
(e.g. silica grains) in the heat exchange fluids. These
impurities maybe the cause of the wear or corrosion by
puncture.
• Filter the coolant and carry out internal inspections as
described in EN 378.
• In case of re-testing please refer to the maximum operating
pressure given on the unit nameplate.
• The reports of periodical checks by the user or operator
must be included in the supervision and maintenance file.
Repair
Any repair or modification, including the replacement of moving
parts:
•
Must follow local regulations and be made by qualified
operators and in accordance with qualified procedures,
including changing the heat exchanger tubes.
• Must be made in accordance with the instructions of the
original manufacturer. Repair and modification that
necessitate permanent assembly (soldering, welding,
expanding etc.) must be made using the correct procedures
and by qualified operators.
•
An indication of any modification or repair must be shown
in the monitoring and maintenance file.
Recycling
The unit is wholly or partly recyclable. After use it contains
refrigerant vapours and oil residue. It is coated by paint.
Operating life
The evaporator and oil separator are designed for:
• Prolonged storage of 15 years under nitrogen charge with
a temperature difference of 20K per day.
•
452000 cycles (start-ups) with a maximum difference of 6
K between two neighbouring points in the vessel, based on
6 start-ups per hour over 15 years at a usage rate of 57%.
Corrosion allowances
Gas side: 0 mm
Heat exchange fluid side: 1 mm for tubular plates in lightly alloyed
steels, 0 mm for stainless steel plates or plates with copper-nickel
or stainless steel protection and 1 mm for water box.
Painted parts : 0 mm
If any parts of the piece (with 0 mm of acceptable corrosion) shows
corrosion, change the piece.
10.2.1 -
Evaporator
30XW-ZE chillers use a flooded multi-tube evaporator. The water
circulates in the tubes and the refrigerant is on the outside in the
shell. One vessel is used to serve both refrigerant circuits. There
is a center tube sheet which separates the two refrigerant circuits.
The tubes are 3/4” diameter copper with an enhanced surface
inside and out.
There is just one water circuit with two water passes (one pass
with option 100C, please refer to chapter 7.5).
The evaporator shell has a polyurethane foam thermal insulation
and a water drain and purge.
It has been tested and stamped in accordance with the applicable
pressure codes. The maximum standard relative operating
pressure is 2100 kPa for the refrigerant side and 1000 kPa for the
water-side. These pressures can be different depending on the
code applied. The water connection of the heat exchanger is a
Victaulic connection.
The products that may be added for thermal insulation of the
containers during the water piping connection procedure must be
chemically neutral in relation to the materials and coatings to which
they are applied. This is also the case for the products originally
supplied by Carrier.