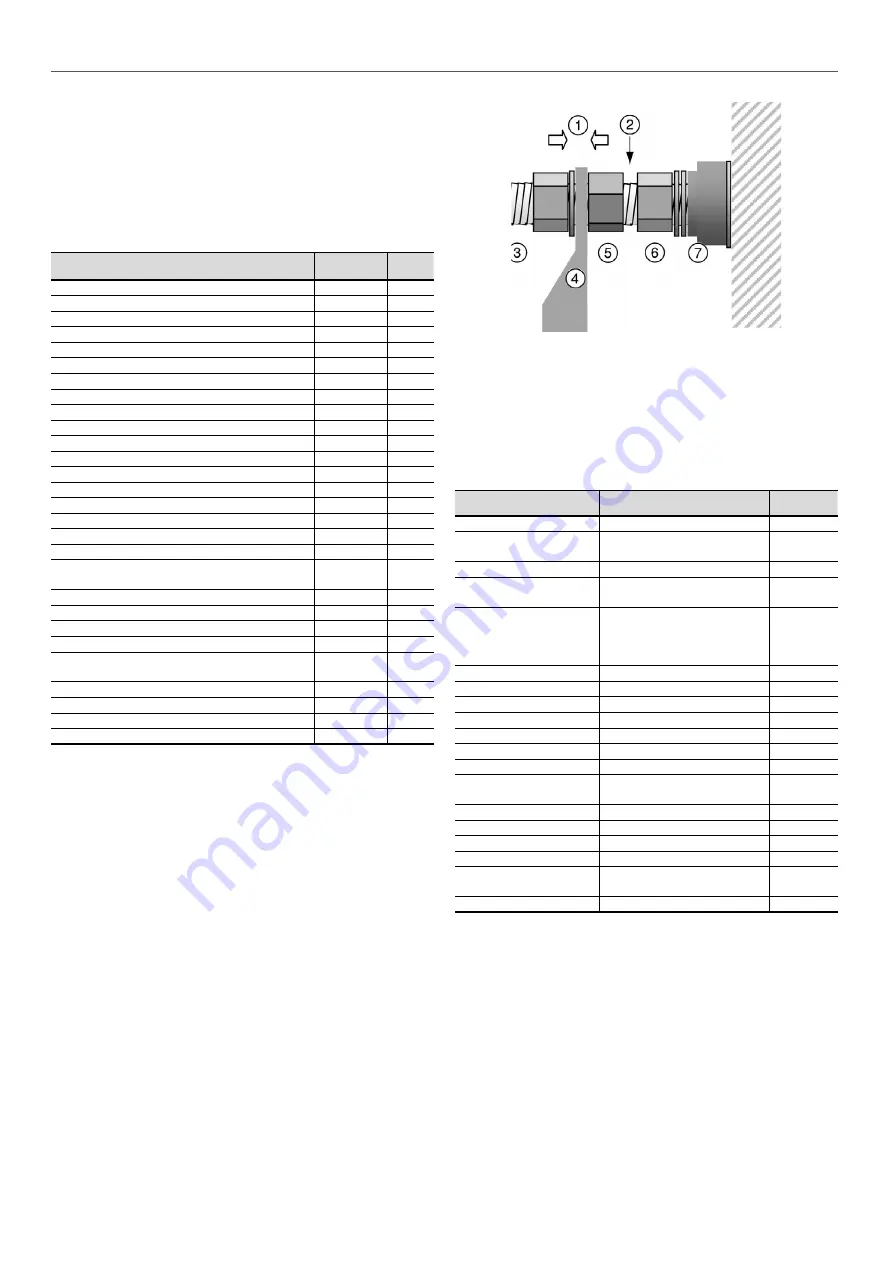
58
The compressor oil that is covered during maintenance contains
refrigerant and must be treated accordling.
Refrigerant under pressure must not be purged to the open air.
13.4 -
Tightening torques for the main electrical
connections
13.4.1 -
Tightening torques for the main electrical
connections
Component
Designation
in the unit
Value
(N.m)
Screw on bus bar, customer connection
M8
-
18
M10
L1 /L2 /L3
30
Soldered screw PE, customer connection (M12)
PE
70
Tunnel terminal screw, compressor contactor
Contactor 3RT103_
Contactor 3RT104_
5
Contactor 3RT105_
11
Contactor 3RT106_
KM_
21
Nut on compressor contactor deck
M8 for contactor 3RT105_
18
M10 for contactor 3RT10_7
KM_
30
Tunnel terminal screw, current transformer
Size 2 (3RB2956_)
11
Size 3 (3RB2966_)
TI_
21
Nut on current transformer deck
M8
18
M10
TI_
30
Compressor earth terminal in the power wiring
control box
Terminal M8
Gnd
30
Compressor phase connection terminals
M12
25
M16
EC_
30
Compressor earth connection
Gnd sur
EC_
25
Tunnel terminal screw, disconnects 3RV1011_
QF_ /QM_
1
Tunnel terminal screw, hydronic pump contactor
Contactor 3RT101_
KM90_
1
Contactor 3RT102_
2,2
ATTENTION: The tightening of the connections at the
compressor terminals requires special precautions. Please
refer to the chapter below.
13.4.2 - Connection precautions for the compressor
power terminals
These precautions must be applied during an intervention that
requires the removal of the power conductors connected to the
compressor supply terminals.
The tightening nut of terminal (6) supporting the isolator (7) must
never be loosened, as ist ensures terminal tightness and
compressor leak tightness.
The tightening of phase lug (4) must apply the torque between counter
nut (5) and tightening nut (3): During this operation a counter-torque
must be applied at counter nut (5). Counter-nut (5) must not be in
contact with the tightening nut of terminal (6).
1. Torque application to tighten the lug
2. Avoid contact between the two nuts
3. Lug tightening nut
4. Flat lug
5. Counter-nut
6. Terminal tightening nut
7. Isolator
13.5 -
Tightening torques for the main bolts and
screws
Screw type
Use
Value (N.m)
(N·m)
Metal screw D = 4.8
Condensing module, housing
supports
4,2
Metal screw D = 6.3
Plastic volute & grill
4,2
Screw H M8
Condensing module,
compressor fixing
18
Taptite screw M10
Condensing module, chassis
- structure fixing, control box
fixings, compressor fixings, oil
separator fixing
30
Taptite screw M6
Piping support, cowling
7
Screw H M8
Piping clip
12
Screw H M6
Piping clip
10
Nut H M10
Compressor chassis
30
Nut H M10
Hydraulic pump chassis
30
Screw H M8
Filter drier cover
35
Screw H M12
Economiser port flange
40
Screw H M16
Oil separator flanges, suction
flanges
110
Screw H M16
Heat exchanger water boxes
190
Screw H M20
Suction flanges
190
Nut 5/8 ORFS
Oil line
65
Nut 3/8 ORFS
Oil line
26
Nut H M12/M16
Victaulic collars on suction
piping
60/130
Self-locking Nut M16
Compressor fixing
30
ATTENTION: The tightening of the connections at the
compressor terminals requires special precautions. Please
refer to the chapter below.
13.6 - Condenser coil
We recommend that coils are inspected regularly to check the
degree of cleanliness. This depends on the environment where
the unit is installed, especially urban and industrial sites, and for
units installed near trees that shed their leaves. Recommendations
for maintenance and cleaning of micro-channel coils (MCHE):
-
Regularly cleaning the coil surface is essential for correct
-
unit operation.
-
Eliminating contamination and removal of harmful residue
will increase the operating life of the coils and the unit.
-
The maintenance and cleaning procedures below are part of
the regular maintenance to increase the operating life of coils.
13 -STANDARD MAINTENANCE