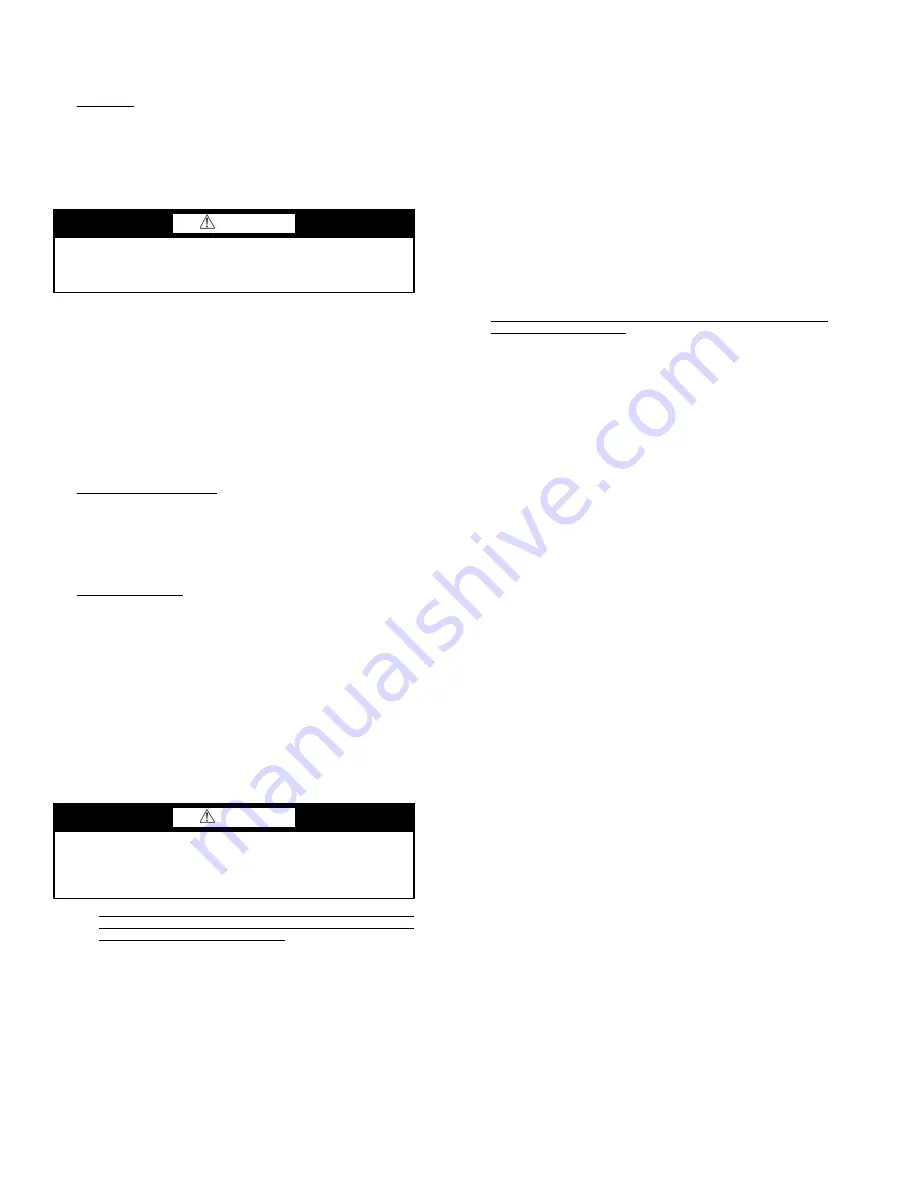
178
NOTES FOR FIG. 71
19XR with Free-Standing Medium Voltage VFD
I.
GENERAL
1.0 Variable Frequency Drive (VFD) shall be designed and
manufactured in accordance with Carrier Engineering
Requirement Z-416.
1.1 All field-supplied conductors, devices, and the field installa-
tion wiring, termination of conductors and devices, must be
in compliance with all applicable codes and job specifica-
tions.
1.2 The routing of field-installed conduit and conductors and
the location of field-installed devices must not interfere with
equipment access or the reading, adjusting, or servicing of
any component.
1.3 Equipment installation and all starting and control devices,
must comply with details in equipment submittal drawings
and literature.
1.4 Contacts and switches are shown in the position they would
assume with the circuit de-energized and chiller shutdown.
1.5 WARNING - Do not use aluminum conductors.
1.6 Installer is responsible for any damage caused by improper
wiring between VFD and machine.
1.7 All field-installed wiring is field-supplied.
II. POWER WIRING TO VFD
2.0 Provide a means of disconnecting power to VFD.
2.1 Lug adapters may be required if installation conditions dic-
tate that conductors be sized beyond the minimum ampac-
ity required. Contact VFD supplier for lug information.
2.2 Compressor motor and controls must be grounded by using
equipment grounding lug provided inside VFD enclosure.
III. CONTROL WIRING
3.0 Field supplied control conductors to be at least 18 AWG or
larger.
3.1 Optional Ice build start/terminate device contacts, optional
remote start/stop device contacts and optional spare safety
device contacts (devices not supplied by Carrier), must
have 24 VAC rating. MAX current is 60 mA, nominal current
is 10 mA. Switches with gold plated bifurcated contacts are
recommended.
3.2 Remove jumper wire between ISM J2-1 and ISM J2-2
before connecting auxiliary safeties between these
terminals.
3.3 Each integrated contact output can control loads (VA) for
evaporator pump, condenser pump, tower fan low, tower fan
high, and alarm annunciator devices rated 5 amps at 115
VAC and up to 3 amps at 277 VAC.
Do not use control transformers in the control center as the
power source for external or field-supplied contactor coils,
actuator motors or any other loads.
3.4 Do not route control wiring carrying 30 v or less within a
conduit which has wires carrying 50 v or higher or along
side wires carrying 50 v or higher.
3.5 Control wiring between VFD and power panel must be sep-
arate shielded cables with minimum rating 600 v, 80 C.
Ground shield at VFD
3.6 If optional pumpout/oil pump circuit breaker is not supplied
within the starter enclosure, it must be located within sight
of machine with wiring routed to suit.
3.7 When providing conductors for oil pump motor and oil
heater power, refer to sizing data on label located on the
chiller power panel, equipment submittal documentation or
equipment product data catalog.
3.8 Spare 4-20 mA output signal is designed for controllers with
a non-grounded 4-20 mA input signal and a maximum input
impedance of 500 ohms.
IV. POWER WIRING BETWEEN FREE-STANDING VFD AND
COMPRESSOR MOTOR
4.0 Medium voltage (over 600 volts) compressor motors have
(3) terminals. Connections are
9
/
16
-in. threaded stud. A
compression lug with a single
9
/
16
-in. diameter hole can be
connected directly to the stud or 3 adapters are supplied for
connecting a NEMA lug. Use suitable connectors and insu-
lation for high voltage alternating current cable terminations
(these items are not supplied by Carrier). Compressor
motor starter must have nameplate stamped as to conform-
ing with Carrier Engineering requirement "Z-416."
4.1 Power conductor rating must meet minimum unit nameplate
voltage and compressor motor RLA. Refer to the label
located on the side of the chiller control panel, equipment
submittal documentation or equipment product data catalog
for conductor sizing data. (Conductor as defined below may
be a single lead or multiple smaller ampacity leads in paral-
lel for the purpose of carrying the equivalent or higher cur-
rent of a single larger lead.)
When (3) conductors are used:
Minimum ampacity per conductor = 1.25 x compressor RLA
When 96) conductors are used:
Minimum ampacity per conductor = 1.25 x compressor
RLA/2
4.2 When more than one conduit is used to run conductors
from VFD to compressor motor terminal box, an equal num-
ber of leads from each phase (conductor) must be in each
conduit to prevent excessive heating. (For example, con-
ductors to motor terminals 1, 2, and 3 in one conduit, and to
1, 2, and 3 in another conduit).
4.4 Compressor motor power conductors may enter terminal
box through top, left side or bottom left using holes cut by
contractor to suit conduit. Flexible conduit should be used
for the last few feet to the terminal box for unit vibration iso-
lation. Use of stress cones may require an oversize (spe-
cial) motor terminal box (not supplied by Carrier).
4.3 Compressor motor frame to be grounded in accordance
with the National Electrical Code (NFPA-70) and applicable
codes. Means for grounding compressor motor is a #4
AWG to 500 MCM pressure connector, supplied and
located in the lower left side corner of the compressor
motor terminal box.
4.5 Do not allow motor terminals to support weight of wire
cables. Use cable supports and strain reliefs as required.
4.6 Use backup wrench when tightening lead connectors to
motor terminal studs. Torque to 30-35 ft-lb max.
4.7 Do not exceed 100 ft. maximum power cable length
between the VFD and motor terminals without consulting
Carrier for special requirements.
CAUTION
To prevent damage to machine, do NOT punch holes or drill into
the top surface of the VFD enclosure for field wiring. Field wiring
knockouts are provided on the top and side of the VFD enclo-
sure for field wiring connections.
CAUTION
Control wiring for Carrier to start pumps and tower fan motors
and establish flows must be provided to assure machine protec-
tion. If primary pump, tower fan, and flow control is by other
means, also provide parallel means for control by Carrier. Fail-
ure to do so could result in machine freeze-up or overpressure.
Summary of Contents for AquaEdge 19XR series
Page 69: ...69 Fig 33 19XR Leak Test Procedures a19 1625 ...
Page 154: ...154 Fig 64 Benshaw Inc Wye Delta Unit Mounted Starter Wiring Schematic Low Voltage a19 1873 ...
Page 161: ...161 Fig 69 Typical Low Voltage Variable Frequency Drive VFD Wiring Schematic 575 v ...
Page 162: ...162 Fig 69 Typical Low Voltage Variable Frequency Drive VFD Wiring Schematic 575 v cont ...
Page 186: ...186 APPENDIX B LEAD LAG WIRING 19XR Lead Lag Schematic Series Cooler Flow a19 1655 ...
Page 187: ...187 APPENDIX B LEAD LAG WIRING cont 19XR Lead Lag Schematic Parallel Cooler Flow a19 1717 ...