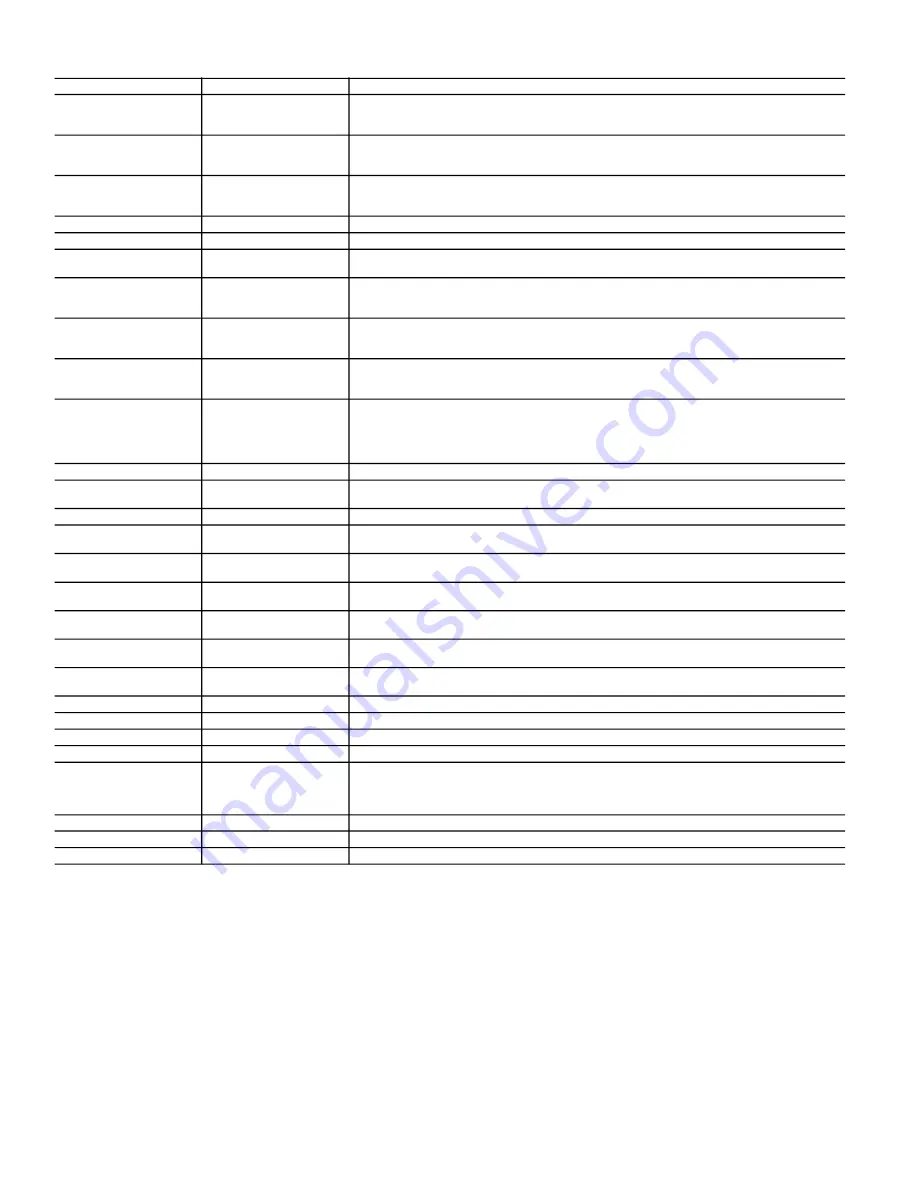
262
Table 52 —
Fault Codes
FAULT CODE
FAULT NAME IN PANEL
DESCRIPTION AND RECOMMENDED CORRECTIVE ACTION
1
OVERCURRENT
Output current is excessive. Check for excessive motor load, insufficient acceleration time
(parameters 2202 ACCELER TIME 1, default 30 seconds), or faulty motor, motor cables or
connections.
2
DC OVERVOLT
Intermediate circuit DC voltage is excessive. Check for static or transient over voltages in the
input power supply, insufficient deceleration time (parameters 2203 DECELER TIME 1,
default 30 seconds), or undersized brake chopper (if present).
3
DEV OVERTEMP
Drive heat sink is overheated. Temperature is at or above 115°C (239°F). Check for fan fail
-
ure, obstructions in the airflow, dirt or dust coating on the heat sink, excessive ambient tem-
perature, or excessive motor load.
4
SHORT CIRC
Fault current. Check for short-circuit in the motor cable(s) or motor or supply disturbances.
5
OVERLOAD
Inverter overload condition. The drive output current exceeds the ratings.
6
DC UNDERVOLT
Intermediate circuit DC voltage is not sufficient. Check for missing phase in the input power
supply, blown fuse, or under voltage on main circuit.
7
AI1 LOSS
Analog input 1 loss. Analog input value is less than AI1 FLT LIMIT (3021). Check source and
connection for analog input and parameter settings for AI1 FLT LIMIT (3021) and 3001
AI<MIN FUNCTION.
8
AI2 LOSS
Analog input 2 loss. Analog input value is less than AI2 FLT LIMIT (3022). Check source and
connection for analog input and parameter settings for AI2 FLT LIMIT (3022) and 3001
AI<MIN FUNCTION.
9
MOT OVERTEMP
Motor is too hot, as estimated by the drive. Check for overloaded motor. Adjust the parame-
ters used for the estimate (3005 through 3009). Check the temperature sensors and Group
35 parameters.
10
PANEL LOSS
Panel communication is lost and either drive is in local control mode (the control panel dis-
plays LOC), or drive is in remote control mode (REM) and is parameterized to accept start/
stop, direction or reference from the control panel. To correct, check the communication
lines and connections. Check parameter 3002 PANEL COMM ERROR, parameters in Group
10: Command Inputs and Group 11: Reference Select (if drive operation is REM).
11
ID RUN FAIL
The motor ID run was not completed successfully. Check motor connections.
12
MOTOR STALL
Motor or process stall. Motor is operating in the stall region. Check for excessive load or
insufficient motor power. Check parameters 3010 through 3012.
13
RESERVED
Not used.
14
EXT FAULT 1
Digital input defined to report first external fault is active. See parameter 3003 EXTERNAL
FAULT 1.
15
EXT FAULT 2
Digital input defined to report second external fault is active. See parameter 3004 EXTER-
NAL FAULT 1.
16
EARTH FAULT
The load on the input power system is out of balance. Check for faults in the motor or motor
cable. Verify that motor cable does not exceed maximum specified length.
17
UNDERLOAD
Motor load is lower than expected. Check for disconnected load. Check parameters 3013
UNDERLOAD FUNCTION through 3015 UNDERLOAD CURVE.
18
THERM FAIL
Internal fault. The thermistor measuring the internal temperature of the drive is open or
shorted. Contact Carrier.
19
OPEX LINK
Internal fault. A communication-related problem has been detected between the OMIO and
OINT boards. Contact Carrier.
20
OPEX PWR
Internal fault. Low voltage condition detected on the OINT board. Contact Carrier.
21
CURR MEAS
Internal fault. Current measurement is out of range. Contact Carrier.
22
SUPPLY PHASE
Ripple voltage in the DC link is too high. Check for missing main phase or blown fuse.
23
RESERVED
Not used.
24
OVERSPEED
Motor speed is greater than 120% of the larger (in magnitude) of 2001 MINIMUM SPEED or
2002 MAXIMUM SPEED parameters. Check parameter settings for 2001 and 2002. Check
adequacy of motor braking torque. Check applicability of torque control. Check brake chop-
per and resistor.
25
RESERVED
Not used.
26
DRIVE ID
Internal fault. Configuration block drive ID is not valid.
27
CONFIG FILE
Internal configuration file has an error. Contact Carrier.