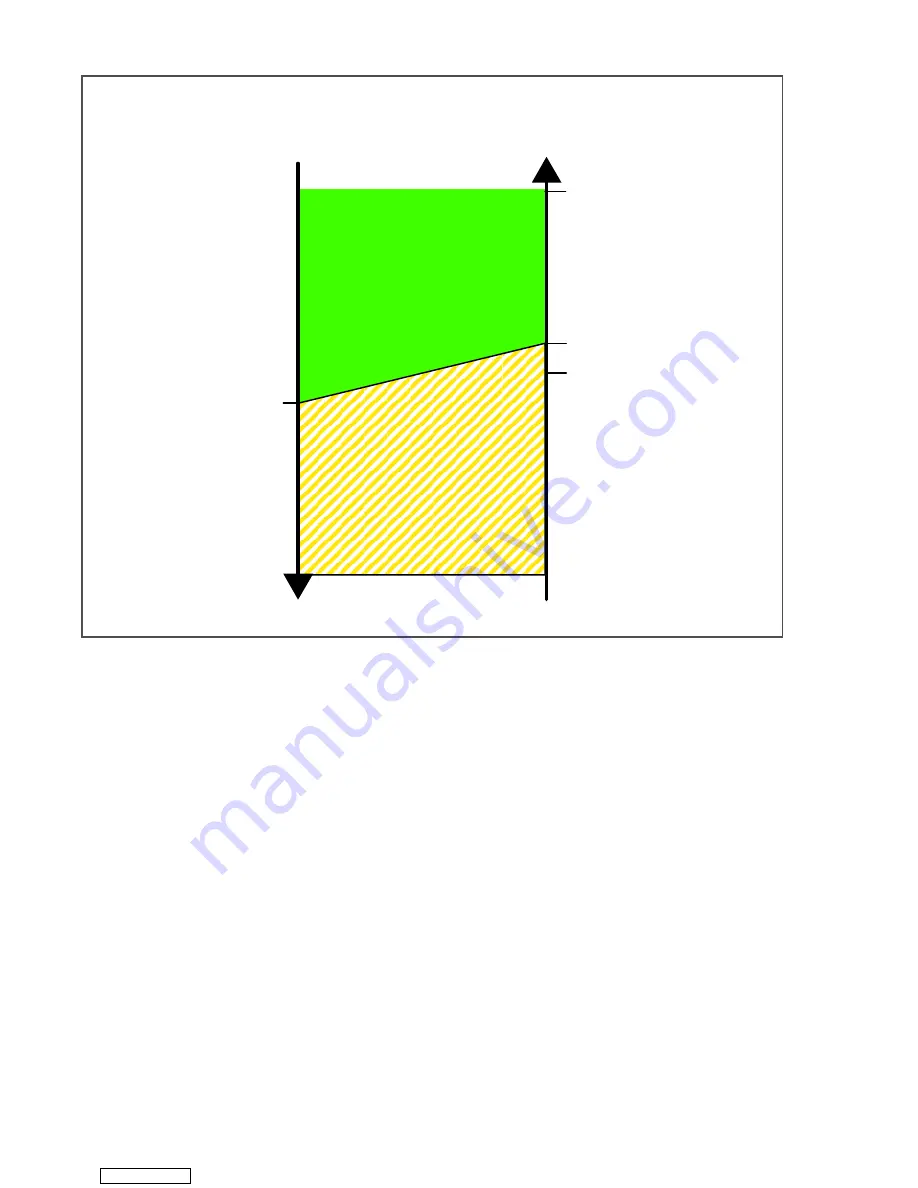
T-368
4–8
Figure 4.8 Controller Operation - Frozen Mode
4.3.13
Frozen Idle Mode
When temperature drops to set point minus 0.2°C
(0.36°F) and the compressor has run for at least five
minutes, the unit will transition to the frozen idle mode.
The compressor is turned off and the evaporator fans
continue to run to circulate air throughout the container.
If temperature rises above set point +0.2°C, (0.36°F)
the unit will transition back to the frozen steady state
mode.
NOTE
On start up of the unit, SMV will reset to a
known open position. This is accomplished
by assuming the valve was fully open, driv-
ing it fully closed, resetting the percentage
open to zero, then opening to a known 21%
staging position.
To prevent rapid cycling of the compressor, a three
minute compressor off time must be satisfied before
the compressor will restart. Under a condition of rapidly
changing return air temperature, the time delay may
allow the return air temperature to rise slightly above
set point temperature before the compressor can
restart.
4.3.14
Frozen “Heat” Mode
If the temperature drops 10°C (18°F) below set point,
the unit will transition to the frozen “heating” mode. The
evaporator fans are brought to high speed, and the
heat from the fans is circulated through the container.
The unit will transition back to frozen steady state when
the temperature rises back to the transition point.
4.3.15
Frozen Economy Mode
In order to activate economy frozen mode operation, a
frozen set point temperature must be selected, and
Cd34 (Economy Mode) set to “ON.” When economy
mode is active, the system will perform normal frozen
mode operations except that the entire refrigeration
system, excluding the controller, will be turned off when
the control temperature is less than or equal to the set
point -2°C (3.6°F).
After an off-cycle period of 60 minutes, the unit will turn
on high speed evaporator fans for three minutes and
then check the control temperature. If the control tem-
perature is greater than or equal to the frozen set point
+0.2°C (0.36°F), the unit will restart the refrigeration
system and continue to cool until the previously men-
tioned off-cycle temperature criteria are met. If the con-
trol temperature is less than the frozen set point +0.2°C
(0.36°F), the unit will turn off the evaporator fans and
restart another 60 minute off-cycle.
Controller Set Point at or BELOW
ï
10
q
C (+14
q
F),
or
ï
5
q
C (+23
q
F) optionally
ï
.20
q
C
+.20
q
C
Air Circulation
Cooling
Set Point
+2.5
q
C
(+4.5
q
F)
Frozen Mode
Falling
Temperature
Rising
Temperature
Downloaded from
Summary of Contents for 69NT40-541-505
Page 2: ...Downloaded from ManualsNet com search engine...
Page 4: ...Downloaded from ManualsNet com search engine...
Page 10: ...Downloaded from ManualsNet com search engine...
Page 14: ...Downloaded from ManualsNet com search engine...
Page 18: ...Downloaded from ManualsNet com search engine...
Page 80: ...Downloaded from ManualsNet com search engine...
Page 86: ...Downloaded from ManualsNet com search engine...
Page 92: ...Downloaded from ManualsNet com search engine...
Page 124: ...Downloaded from ManualsNet com search engine...
Page 125: ...Downloaded from ManualsNet com search engine...
Page 126: ...Downloaded from ManualsNet com search engine...
Page 142: ...Downloaded from ManualsNet com search engine...