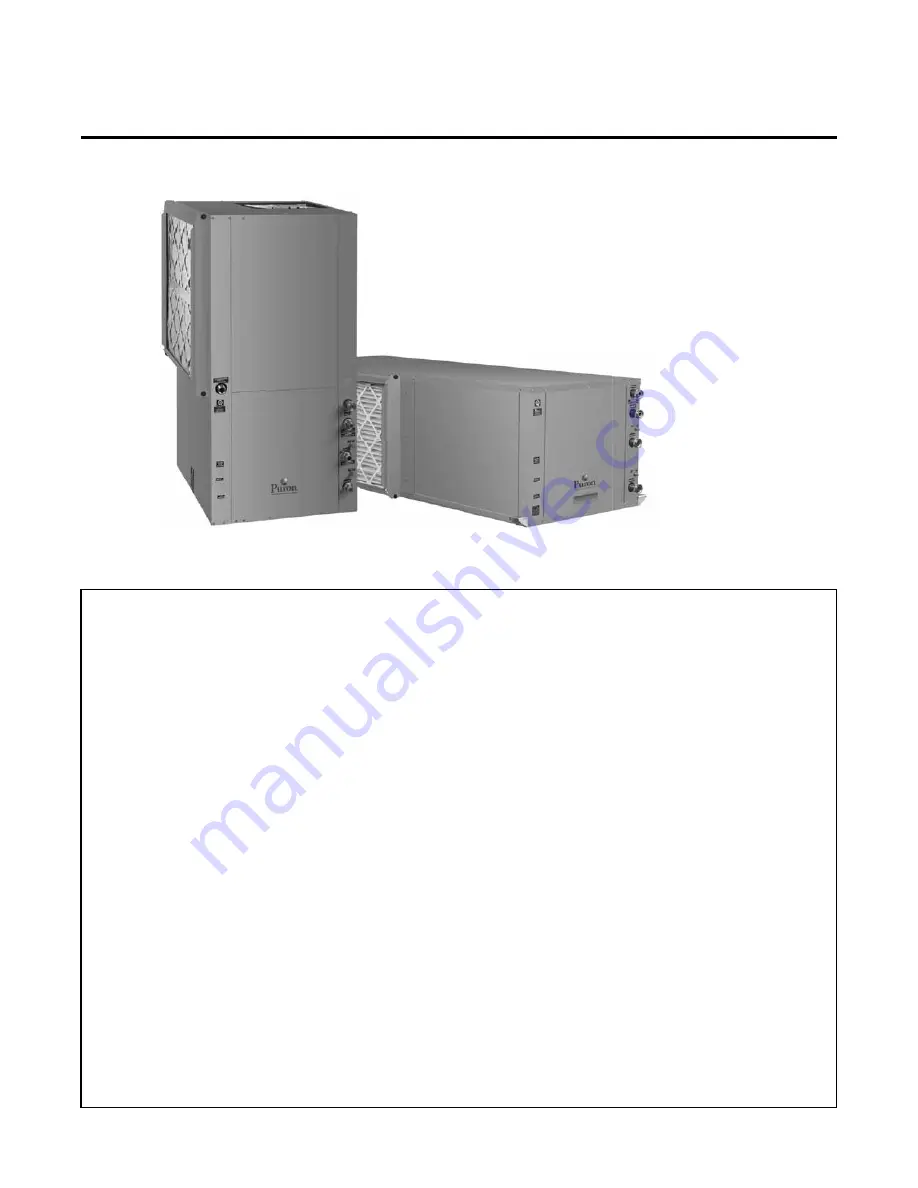
Table of Contents
Model Nomenclature
3
General Information
4
Pre-Installation 4
Vertical Installation
5
Horizontal Installation
6-8
Condensate and Water Connections
9
Integrated Variable-Speed Water Flow
10
Control Heat Pump Applications Overview
Closed Loop Applications
11
with Internal Flow Control
Flushing the Earth Loop
12-14
Multiple Unit Piping and Flushing
15-17
Ground Loop Applications
18-19
Closed Loop - External Central
20
Pumping Applications
Open Loop or Ground Water Systems
21-22
Water Quality Requirements
23
Hot Water Generator
24-26
Electrical - Line Voltage
27
Electrical - Low Voltage Wiring
28
Thermostat Wiring
29
Wiring Diagrams
30-33
ECM Blower Control
34
Blower Data
35
DXM2 Controls
36-37
Low Water Temperature Cutout Selection
37
Unit Commissioning
38
and Operating Conditions
Unit and System Checkout
39
Unit Start-Up Procedure
39-41
Unit Operating Conditions
41-43
Performance Data (Full Load)
44-49
Preventive Maintenance
50
Troubleshooting
51-52
DXM2 Troubleshooting
53
Functional & Performance Troubleshooting
54-57
Troubleshooting Form
58
Warranty
59
Revision History
60
GT-PB Series (50YFV, 50YFH Models)
Installation, Operation and Maintenance Instructions
Residential Digital Horizontal & Vertical Packaged
Geothermal Heat Pumps
97B0046N05
Rev: 4 April, 2014