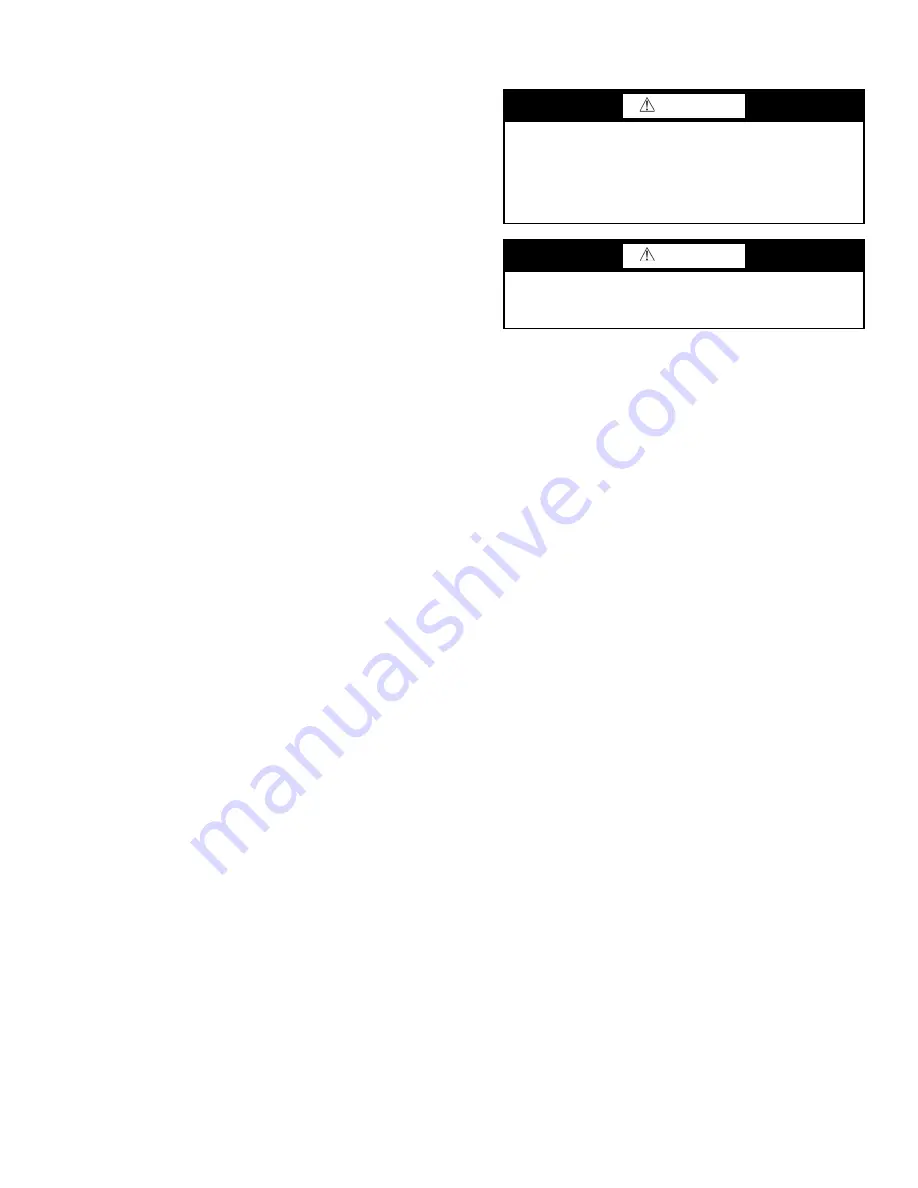
13
START-UP
Pre-Start Check —
Once installation is complete, make
the following pre-start checks:
1. All indoor and outdoor units are properly installed.
2. All piping and insulation is complete.
3. All electrical connections (both power and control) are
properly terminated.
4. All condensate drains are installed correctly.
5. The power supply is of the right voltage and frequency.
6. The units are properly grounded in accordance with cur-
rent electrical codes.
7. Suction and liquid line service valves are in open posi-
tion.
System Operation Check —
Once the installation
and pre-start checks are completed, follow these steps:
1. Using remote controller, select cooling or heating mode
to check the operation of the system.
2. While the system is in operation, check the following on
indoor unit:
a. Switches or buttons on the remote controller are
easy to push.
b. Indicator light is showing normal operation and no
error is indicated.
c. Swing mode of air louvers is working (if applica-
ble to unit).
d. Drain pump operation is normal (if applicable).
e. No abnormal vibration or noise is noticed.
3. While the system is in operation, check the following on
outdoor unit:
a. No abnormal vibration or noise is noticed.
b. Condenser fan is in operation.
c. Indicator light is showing normal operation and no
error is indicated.
NOTE: If the unit is turned off or restarted, there is a time
delay of 3 minutes for the compressor to start from the time the
power is restored.
MAINTENANCE
The following are recommended guidelines. Jobsite conditions
may dictate that the maintenance schedule be performed more
often than recommended here.
EVERY 3 MONTHS:
• Check coil condition. Clean the coil if necessary.
EVERY 6 MONTHS — Follow 3-month maintenance sched-
ule. In addition:
• Check for and remove debris that may have settled
around the base of the outdoor unit.
• Check for proper condensate drainage (clear basepan).
• Eliminate any standing water inside the outdoor unit.
EVERY 12 MONTHS — Follow 6-month maintenance
schedule. In addition:
• Be sure all electrical connections are secure.
• Check the heating and cooling action to confirm proper
operation.
TROUBLESHOOTING
There are two buttons on Main Board 1 that can aid during
troubleshooting.
SW1 — Push this button to operate the complete system in
Cooling mode. (This function is typically used if error messag-
es are received during the commissioning process.)
SW2 — Push this button to run a system check. This function
checks that the entire system is in operation, including all in-
door units.
Table 7 lists errors, possible causes, and possible solutions.
CAUTION
When servicing or repairing this unit, use only factory-
approved service replacement parts. Refer to the rating
plate on the unit for complete unit model number, serial
number and company address. Any substitution of parts or
controls not approved by the factory will be at the owner’s
risk and may result in equipment damage.
CAUTION
To avoid equipment damage, do not attempt to reuse any
mechanical or electrical controllers that have been wet.
Replace defective controller.