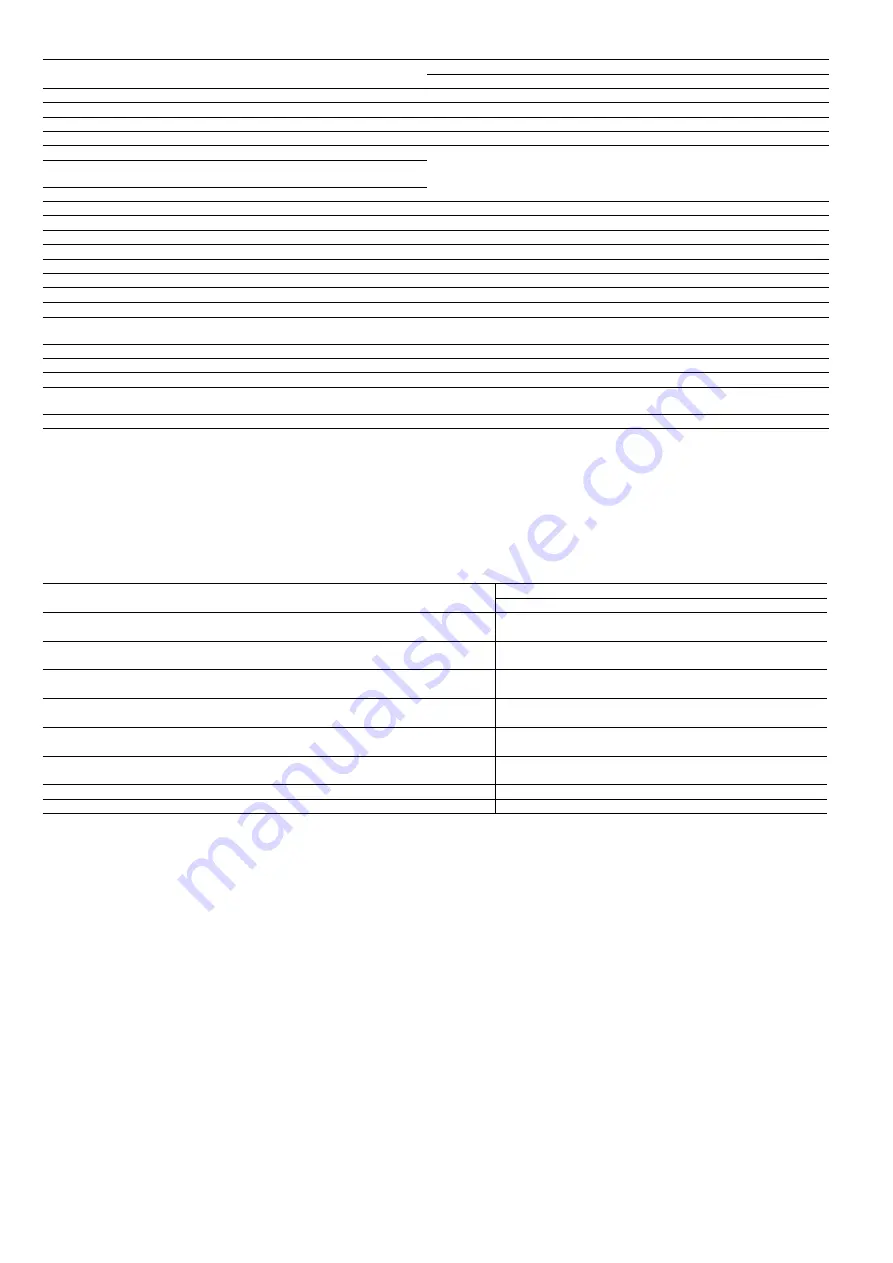
28
Motors of single and dual high-pressure pumps (option 116R, 116S, 116V, 116W)
No.** Description***
30RQS/RQSY
039
045
050
060
070
078
080
090
100
120
140
160
1
Nominal efficiency at full load and nominal voltage
%
84,8 84,8 84,8 84,8 84,8 84,8 84,8 84,8 84,8 85,9 85,9 85,9
1
Nominal efficiency at 75% rated load and nominal voltage
%
82,2 82,2 82,2 82,2 82,2 82,2 82,2 82,2 82,2 84
84
84
1
Nominal efficiency at 50% rated load and nominal voltage
%
79
79
79
79
79
79
79
79
79
82,1 82,1 82,1
2
Efficiency level
IE3
3
Year of manufacture
This information varies depending on the manufacturer and model at the time of
incorporation. Please refer to the motor name plates.
4
Manufacturer's name and trademark, commercial registration
number and place of manufacturer
5
Product's model number
6
Number of motor poles
2
2
2
2
2
2
2
2
2
2
2
2
7-1
Rated shaft power output at full load and nominal voltage (400 V) kW
1,7
1,7
1,7
1,7
1,7
1,7
1,7
1,7
1,7
2,2
2,2
2,2
7-2
Maximum power input (400 V)****
kW
2,4
2,4
2,4
2,4
2,4
2,4
2,4
2,4
2,4
2,9
2,9
2,9
8
Rated input frequency
Hz
50
50
50
50
50
50
50
50
50
50
50
50
9-1
Rated voltage
V
3 x 400
9-2
Maximum current drawn (400 V)†
A
4,2
4,2
4,2
4,2
4,2
4,2
4,2
4,2
4,2
5
5
5
10
Rated speed
rpm
2870 2870 2870 2870 2870 2870 2870 2870 2870 2855 2855 2855
r/s
48
48
48
48
48
48
48
48
48
48
48
48
11
Product disassembly, recycling or disposal at end of life
Disassembly using standard tools. Disposal and recycling using an appropriate
company.
12
Operating conditions for which the motor is specifically designed
I - Altitudes above sea level
m
< 1000††
II - Ambient air temperature
°C
< 55
IV - Maximum air temperature
°C
Please refer to the operating conditions given in this manual or in the specific
conditions in the Carrier selection programs.
V - Potentially explosive atmospheres
Non-ATEX environment
* Required by regulation 640/2009 with regard to the application of directive 2009/125/EC on the eco-design requirements for electric motors
** Item number imposed by regulation 640/2009, annex I2b.
*** Description given by regulation 640/2009, annex I2b.
**** To obtain the maximum power input for a unit with hydronic module add the maximum unit power input from the electrical data table to the pump power input.
† To obtain the maximum unit operating current draw for a unit with hydronic module add the maximum unit current draw from the electrical data table to the pump current
draw.
†† Above 1000 m, a degradation of 3% for each 500 m should be taken into consideration.
9.3 - Compressor usage and electrical data for standard units
Compressor
I Nom
I Max
(Un)
I Max
(Un-10%)
LRA*
A
LRA**
A
Cosine
phi max.
Circuit
30RQS/30RQSY
039 045 050 060
070 078 080
090 100 120 140 160
ZP90
11.4
16
17.6
95
57
0.82
A
2
-
-
-
-
-
-
-
-
-
-
-
B
-
-
-
-
-
-
-
-
-
-
-
-
ZP103
13.1
21
23.1
111
67
0.84
A
-
2
-
-
-
-
-
-
-
-
-
-
B
-
-
-
-
-
-
-
-
-
-
-
-
ZP120
15.1
22
24.3
118
71
0.84
A
-
-
2
-
-
-
-
-
-
-
-
-
B
-
-
-
-
-
-
-
-
-
-
-
-
ZP137
16.6
25
27.8
118
71
0.86
A
-
-
-
2
-
-
-
3
-
-
-
-
B
-
-
-
-
-
-
-
-
-
-
-
-
ZP154
18.7
31
34.9
140
84
0.85
A
-
-
-
-
2
-
-
-
3
-
2
-
B
-
-
-
-
-
-
-
-
-
-
2
-
ZP182
23.9
34
37.3
174
104
0.84
A
-
-
-
-
-
2
2
-
-
3
-
2
B
-
-
-
-
-
-
-
-
-
-
-
2
Total circuit A
2
2
2
2
2
2
2
3
3
3
2
2
Total circuit B
-
-
-
-
-
-
-
-
-
-
2
2
I Nom Nominal current draw at Eurovent conditions (see definition of conditions under nominal unit current draw), A
I Max Maximum operating current at 360 V, A
*
Locked rotor current at nominal voltage, A
**
Locked rotor current at nominal voltage, electronic starter
Summary of Contents for 30RQS039
Page 55: ......