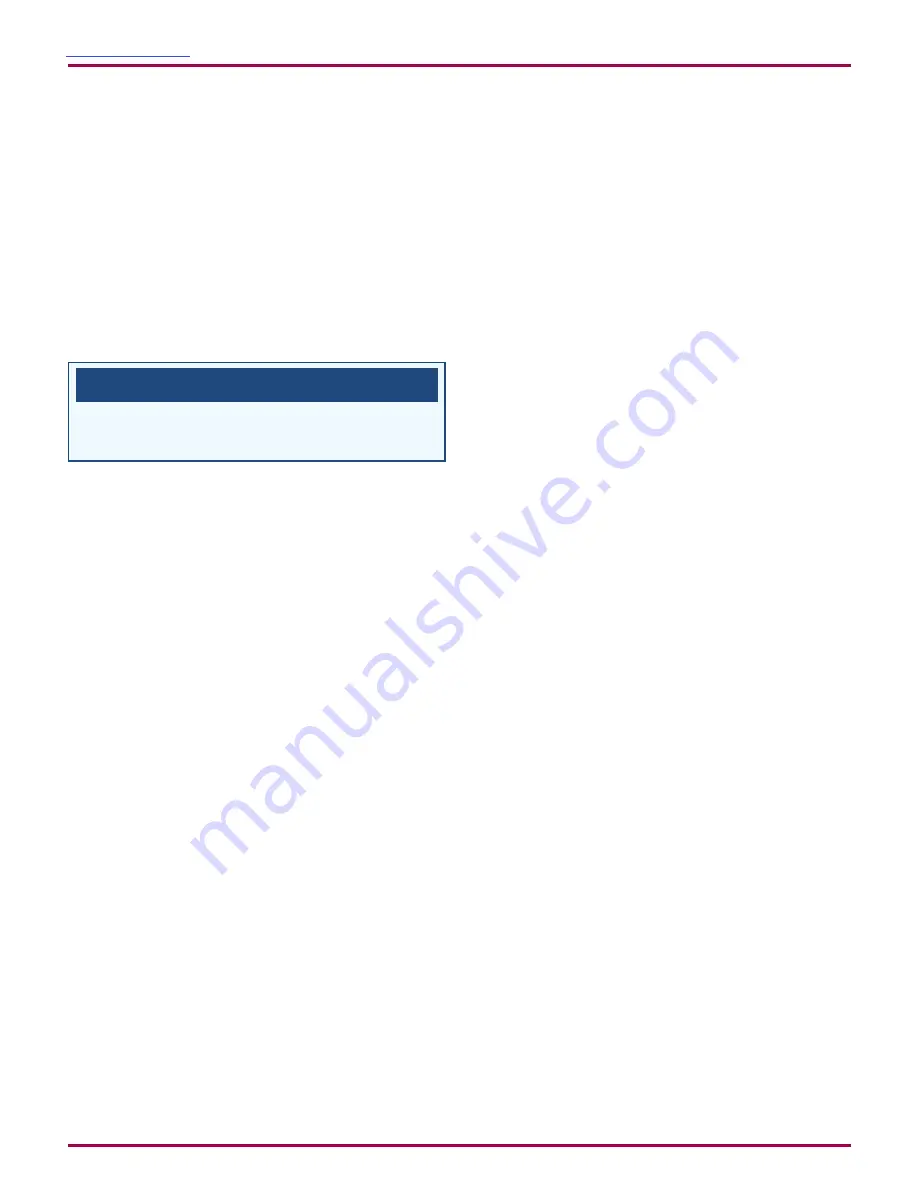
Clean
Any CHANNEL or Gun can be placed into a CLEAN mode
by an external command or through the Host controller. The
Clean mode forces the material regulator fully open until
turned OFF. The GUN Enable and CLEAN inputs must be
active and all system or GUN faults cleared. To properly
exit the CLEAN MODE, the GUN Clean input should be
removed followed by a GUN Halt signal, or a command
issued from the Operator Interface Panel (host controller).
Each CHANNEL must be set as a "clean" CHANNEL in
the Clean CHANNEL parameter located in the Gun Con-
figuration table.
Full Error Detection
The DynaFlow controller will detect certain error conditions
and indicate the cause of the error with a code. The code
indicates the faulted Gun and CHANNEL, as well as giving
you a text error message. All errors are categorized by
CHANNEL, Gun or System depending on the type of error.
The error codes and conditions are listed in the appendix
and include:
• Tolerance errors in fluid flow rates for each material
• Tolerance errors in fluid flow ratios for each material
• Reverse fluid flow
• Low material flow
• High material flow
• Pot-life timers expired
• Memory errors
• Backup disk errors
• Configuration errors
• System errors
PROCEDURES
First-Time System Start-Up
This section is intended for skilled trades personnel. Always
be aware of safety guidelines while operating equipment.
Before power is supplied to the DynaFlow Fluid Flow
Control, take time to familiarize yourself with the controls.
Unexpected actions can occur during initial power-up
sequences and you should know which controls shut down
the controller. The following information serves as a guide
for initial system testing and start-up. Operational problems
will be avoided if time is taken to follow the steps outlined
below. Read through the entire sequence first before
performing any actions.
• Verify that the Interface and Channel Module dip switch
settings are correct. Reference the HARDWARE
SETTINGS section.
• Visually inspect the entire system. Review the
"Installation" section of this manual and any related
manuals such as the flow meter and material regulator.
Verify that all air and fluid lines are routed properly and
fittings are secure.
• Make sure that the required fluid filtration is installed. Fluid
lines should be flushed out manually before installation
of the flow meters to ensure that any large particles or
contamination located from the fluid filter to the flow
meter connection are removed.
• Make sure that the required air filtration for the E/P
transducer(s) is installed.
• If rotary applicators are used, remove the front shroud
and bell cup to expose the paint feed tube. If GUNs
are being used, point the applicator(s) downward if
possible. This will prevent the possibility of material
from contaminating the applicator and provide additional
safety for any per-sonnel working near the system.
• Turn ON the main power disconnect to the fluid flow
control panel.
• Turn ON the power switch located on the flow
control panel.
NOTE
Make sure the proper channels are configured to
"clean" on the Gun Parameters screen.
LN-9400-00-R11 (08/2018)
51 / 96
www.carlisleft.com
PARTS IDENTIFICATION