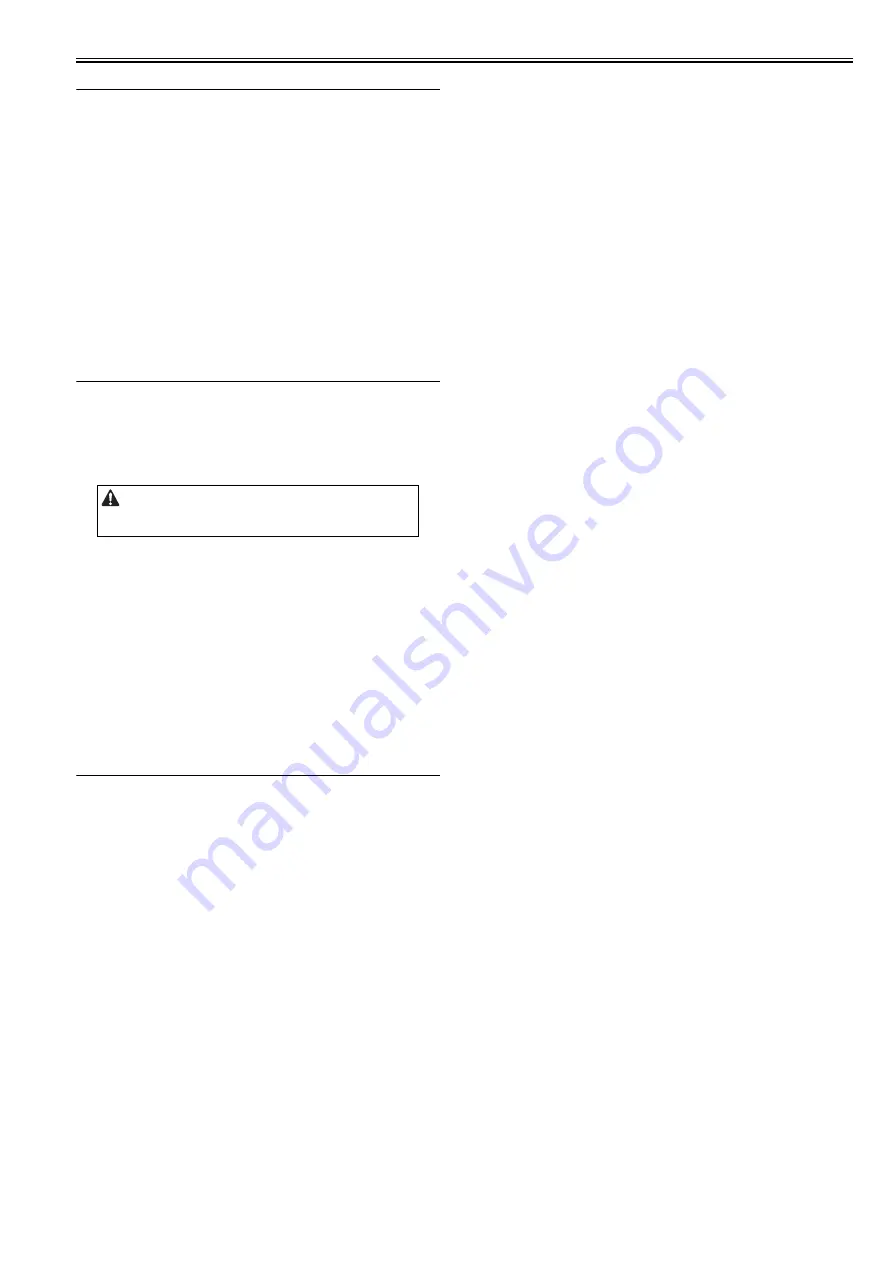
Chapter 11
11-1
11.1 Scanning System
11.1.1 Procedure after Replacing the CIS
0020-4282
After replacing the contact image sensor (CIS), go through the following
steps to perform inter-channel output correction:
1) Enter the service mode.
Sequentially press the Additional Functions, # key on the operation panel.
2) Using the upper/lower arrow keys on the operation panel, select "Test".
3) Press the OK key.
4) Using the upper/lower arrow keys on the operation panel, select "Scanner
test".
5) Press the OK key.
6) Using the upper/lower arrow keys on the operation panel, select "CS Out-
put Test".
7) Press the OK key.
8) Select "Yes" and then press the OK key.
After completion of the above steps, contact sensor output correction will be
performed and parameters will be set automatically.
11.2 Image Formation System
11.2.1 Procedure after Replacing the Developing
Assembly
0020-4283
<Going through the Developer Idling Mode>
1) Plug the power cord into the outlet.
2) Open the front cover.
3) With the front cover open, turn on the main power switch.
4) When a message appears on the operation panel display, press the follow-
ing keys to enter the service mode:
Additional Functions key > # key
5) Select "Service's Choice" using the arrow key, and then press the OK key.
6) Select "Printer Setting" using the arrow key, and hen press the OK key.
7) Select "BitSwitch14" using the arrow key, and hen press the OK key.
8) Select "SW-14-1" using the arrow key, and hen press the OK key.
9) Select "On" using the arrow key, and hen press the OK key.
10) Press the Reset key to exit the service mode.
11) Close the front cover. The machine will run in the developer idling mode
for about 1 minute.
12) When the machine stops, the idling mode ends.
Install, the toner cartridge following the above-mentioned procedure.
11.3 Electrical Components
11.3.1 Procedure after Replacing the Image Processor
PCB
0020-4284
If you have replaced the image processor PCB with a new one, perform the
following operations:
- Using the user support tool, download the latest firmware (System/Boot).
- Input the all value printed on the service label affixed to the rear cover.
Make the following adjustments:
- Correction of output between CIS channels
1) Enter the service mode.
Sequentially press the Additional Functions, # key on the operation panel.
2) Using the upper/lower arrow keys on the operation panel, select "Test".
3) Press the OK key.
4) Using the upper/lower arrow keys on the operation panel, select "Scanner
test".
5) Press the OK key.
6) Using the upper/lower arrow keys on the operation panel, select "CS Out-
put Test".
7) Press the OK key.
8) Select "Yes" and then press the OK key.
After completion of the above steps, contact sensor output correction will be
performed and parameters will be set automatically.
- Read position adjustment (Stream reading: Only when the ADF is installed)
1) Enter the service mode.
Sequentially press the Additional Functions, # key on the operation panel.
2) Using the upper/lower arrow keys on the operation panel, select "Test".
3) Press the OK key.
4) Using the upper/lower arrow keys on the operation panel, select "Scanner
test".
5) Press the OK key.
6) Using the upper/lower arrow keys on the operation panel, select "CS Po-
sition Test".
7) Press the OK key.
8) Select "Yes" and press the OK key.
The optical system starts scanning. Several seconds later, automatic adjust-
ment of the reading position finishes and "OK" appears.
After replacing the developing assembly, go through the following
steps in the developing assembly idle rotation mode before installing the
toner cartridge.
Summary of Contents for iR2422 series
Page 1: ...May 12 2014 Service Manual iR2422 2420 2320 2318 Series...
Page 2: ......
Page 6: ......
Page 16: ...Contents...
Page 17: ...Chapter 1 Introduction...
Page 18: ......
Page 20: ......
Page 50: ......
Page 51: ...Chapter 2 Installation...
Page 52: ......
Page 54: ......
Page 58: ...Chapter 2 2 4 7 Left cover front 15 Right cover upper 8 Manual feed tray 16 Right cover lower...
Page 62: ...Chapter 2 2 8 8 Manual feed tray 16 Right cover lower...
Page 64: ...Chapter 2 2 10 8 Manual feed tray 16 Right cover lower...
Page 89: ...Chapter 2 2 35...
Page 90: ......
Page 91: ...Chapter 3 Main Controller...
Page 92: ......
Page 94: ......
Page 102: ......
Page 103: ...Chapter 4 Original Exposure System...
Page 104: ......
Page 135: ...9 Remove the reader heater left 1 Connector 2 1 pc Screw 3 1 pc F 4 73 2 3 1...
Page 136: ......
Page 137: ...Chapter 5 Laser Exposure...
Page 138: ......
Page 140: ......
Page 148: ...Chapter 5 5 8...
Page 149: ...Chapter 6 Image Formation...
Page 150: ......
Page 152: ......
Page 165: ...Chapter 7 Pickup Feeding System...
Page 166: ......
Page 192: ...Chapter 7 7 24...
Page 193: ...Chapter 8 Fixing System...
Page 194: ......
Page 196: ......
Page 207: ...Chapter 9 External and Controls...
Page 208: ......
Page 229: ...Chapter 10 Maintenance and Inspection...
Page 230: ......
Page 232: ......
Page 235: ...Chapter 11 Standards and Adjustments...
Page 236: ......
Page 238: ......
Page 240: ...Chapter 11 11 2...
Page 241: ...Chapter 12 Correcting Faulty Images...
Page 242: ......
Page 244: ......
Page 256: ......
Page 257: ...Chapter 13 Self Diagnosis...
Page 258: ......
Page 260: ......
Page 269: ...Chapter 14 Service Mode...
Page 270: ......
Page 272: ......
Page 287: ...Chapter 15 Upgrading...
Page 288: ......
Page 290: ......
Page 295: ...Chapter 16 Service Tools...
Page 296: ......
Page 298: ......
Page 300: ......
Page 301: ...Chapter 17 Backup Data...
Page 302: ......
Page 303: ...Contents Contents 17 1 Backup Data 17 1...
Page 304: ......
Page 306: ......
Page 307: ...May 12 2014...
Page 308: ......