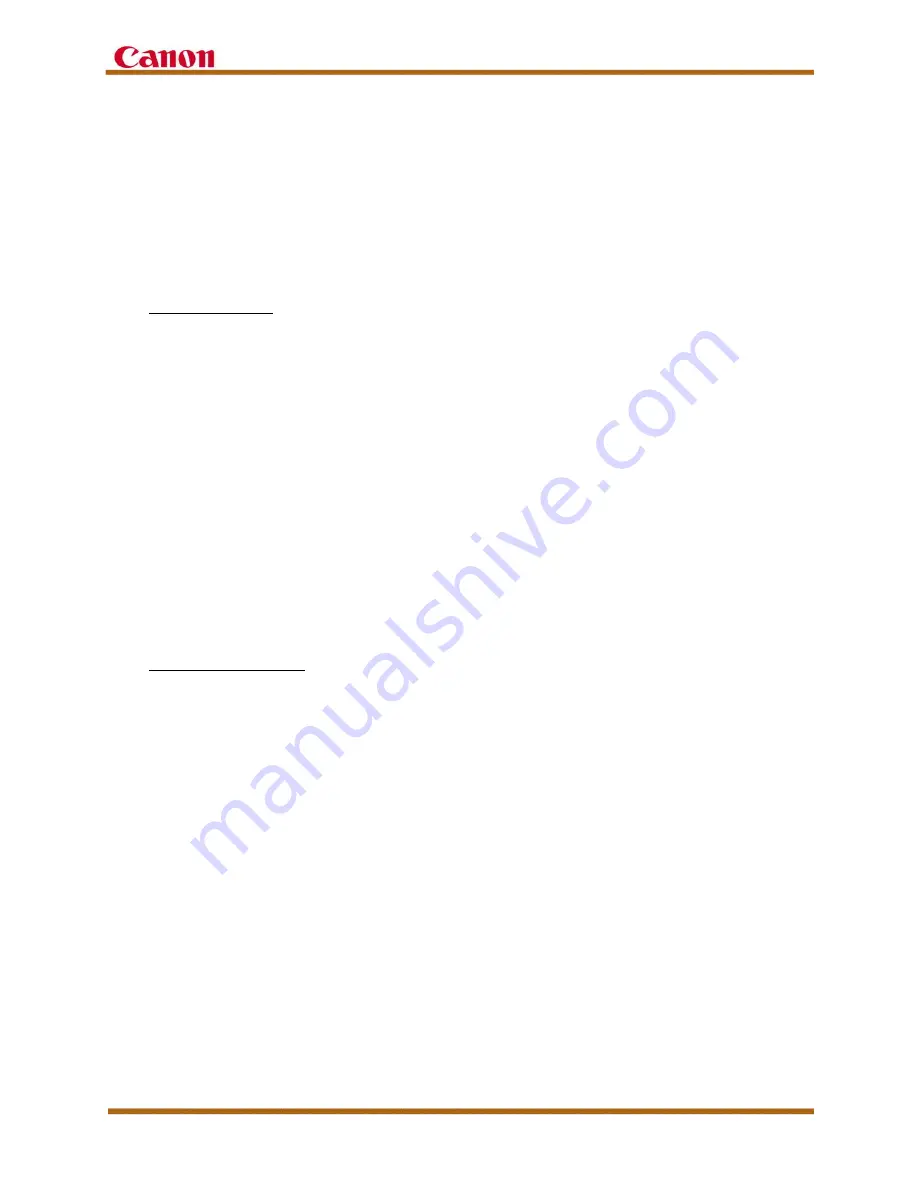
imagePRESS C910/C810/C710 Customer Expectations Document
Version 5
imagePRESS C910/C810/C710 Customer Expectations Document
Page 13
2.4 Customer-Defined Image Quality Adjustments and Recommendations
Customer-defined image quality adjustments enable the customer to enhance the
productivity of the machine. There are several ways to maintain color consistency
for each job. The recommendations below aim at reproducing optimal images
under variable factors (i.e., changes in the environment).
To achieve the best image quality, the following factors are recommended.
All Controllers
•
Tighter control of the temperature and humidity will result in tighter color
consistency in the device.
•
The device must be maintained properly, which includes performing preventative
maintenance as scheduled.
•
The customer can also maintain proper color calibration on the device by
performing an Automatic Gradation Adjustment once a day. For optimal quality,
the customer should perform an Auto Gradation Adjustment whenever a change
in print quality is noticed and when dither pattern adjustments are made. It is
strongly suggested that the customer uses one media for the Automatic
Gradation Adjustment daily. The media for optimal color control should be
consistent with Hammermill 28 lb color laser.
•
Some customers may want to incorporate a Color Management workflow that
consists of not only the above, but also utilizes the Color and Imaging features
included with the attached print controller.
PRISMAsync Only
Optimal quality is maintained through the calibration of media families in use.
Additionally, each halftone can be calibrated per media family for an environment
that requires the highest degree of color control.
Best Practices: While working, Color Management must be implemented with
consistency. This, along with a stable environment and a well-maintained system,
makes the customer’s ability to reproduce color more efficient.