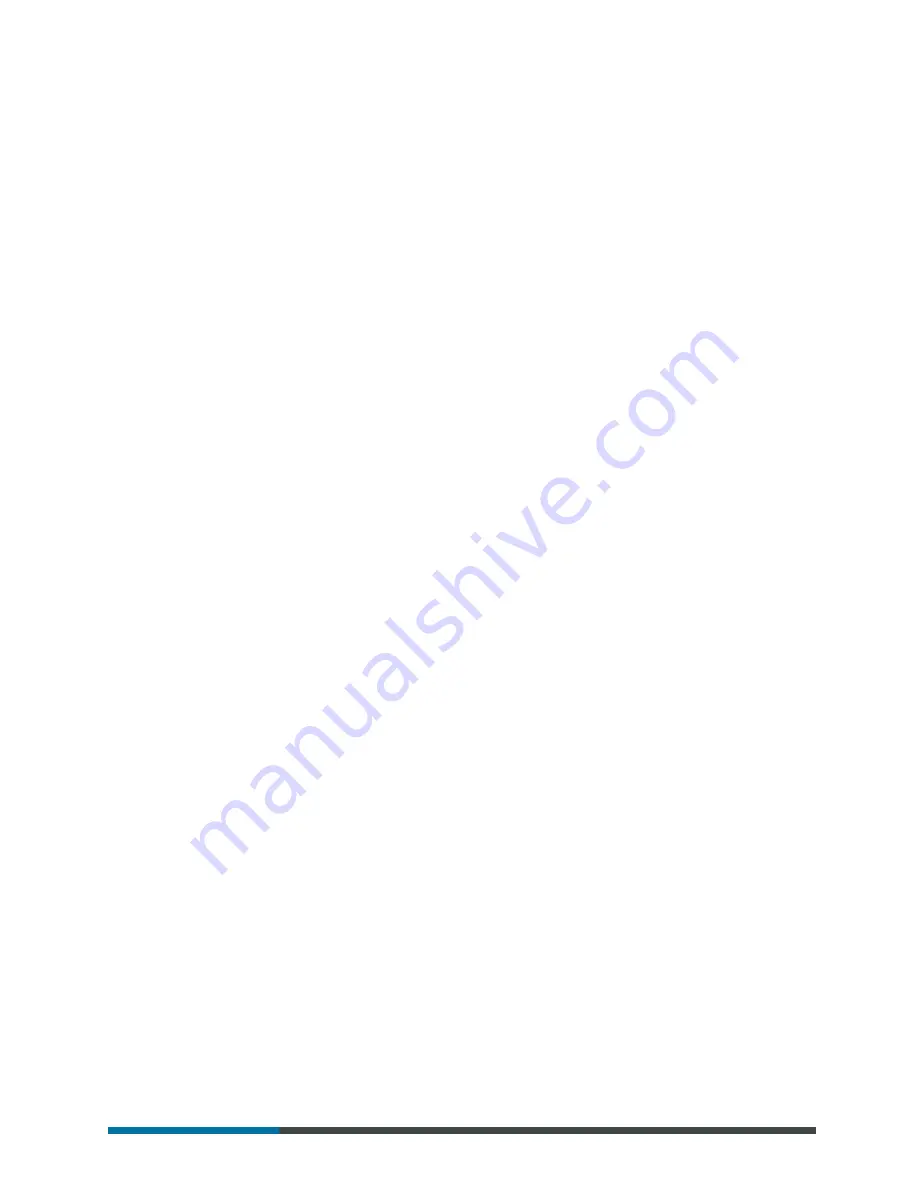
CPB-515 Operation and Maintenance Manual
– TTS 45, 70, 80,100, 110 Series (10-2017)
21
5. When alignment is complete reinstall the lock plates and tighten cap screws to
their required torque specification of 130 N-m (95 lb-ft).
6.3 Track system inspection
Track System
Inspect track system for material build-up on frames and wheels. Clean material from
undercarriage.
Idlers and midrollers
Check the general condition of the idlers and midrollers, in particular on inner guide
surface of the wheels. Excessive wear in these areas can be caused by track alignment
issue, debris ingestion or continuous hillside work.
Rubber track guide lugs
Guide lugs keep the track on the track system. Proper alignment of the track is essential
to improving overall life and decreasing operating costs. If track is misaligned or operating
on side slope, guide lug wear or damage may occur. Also guide lug damage may occur if
proper break-in procedures are not followed or system is operated outside the maximum
speed recommendations listed in this manual. Monitoring guide lugs condition will alert
the operator to an issue and generally if corrected early prior to loss of performance or
durability.
Track carcass
Inspect track surface to remove imbedded stones or debris. This contamination can work
its way into the track and damage the steel cable.
Steel wire may come out from the track carcass without affecting the performance of the
track. Remove loose wires by cutting them at the rubber surface.
Track tread
Muddy soils usually cause limited wear, while roading long distances can bring about
accelerated tread wear. Due to the crown of the road, and deflection in the system, the
tread closest to the machine will tend to wear faster than the tread on the outer portion of
the track. Adhere to speed and weight limitations published in this document.
6.4 Adjusting track tension
Tension is pre-set at the factory and requires no adjustment during operation. Provision is
made to detension the track system allowing for removal of the rubber track.