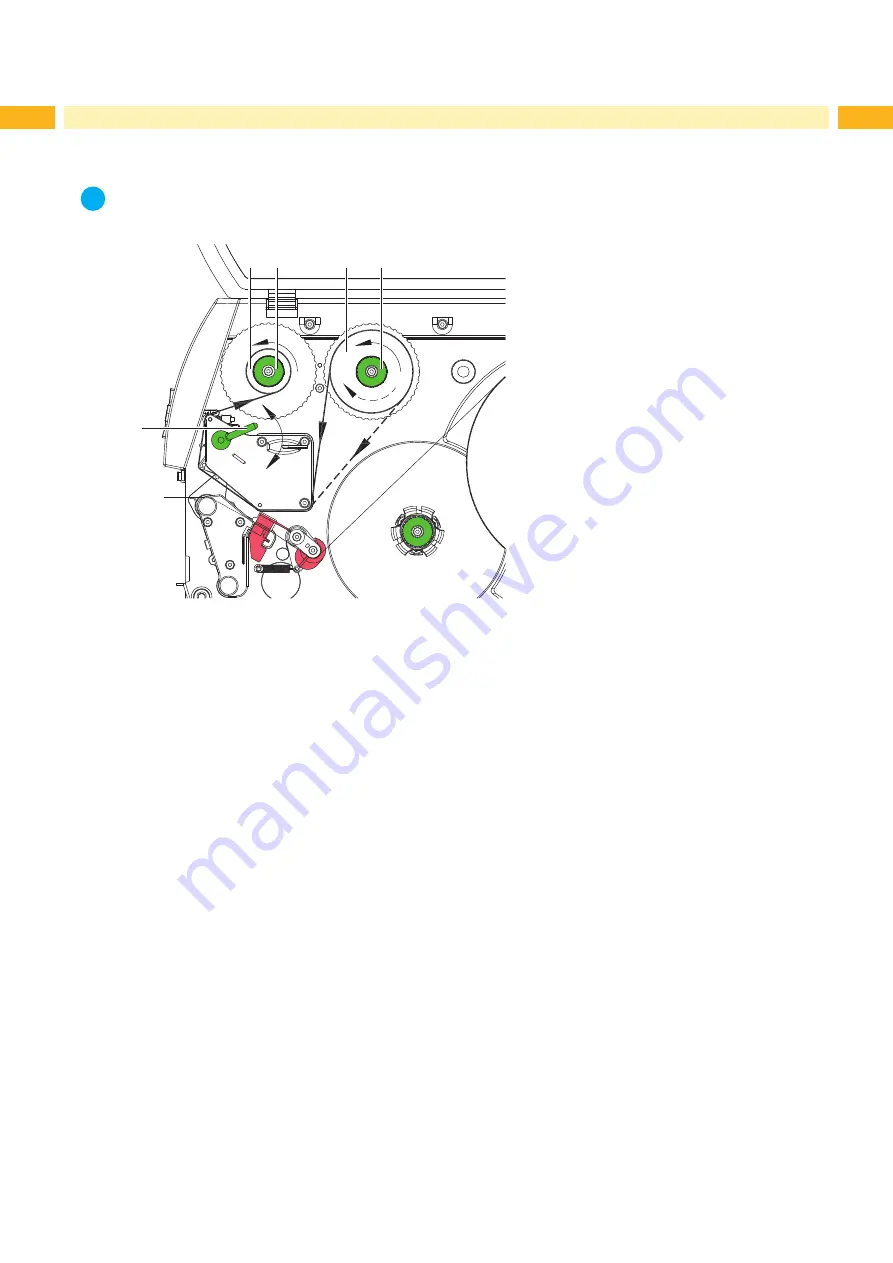
20
20
4
Loading Material
4.5
Loading Transfer Ribbon
i
Notice!
With direct thermal printing, do not load a transfer ribbon; if one has already been loaded, remove it.
1
3
4
5
2
Fig. 14
Feed path of the transfer ribbon
1. Clean printhead before loading the transfer ribbon (
2. Turn lever (5) counterclockwise to lift the printhead.
3. Slide transfer ribbon roll (3) onto the ribbon supply hub (4) until it stops and so that the color coating of the ribbon
faces downward when being unwound. No rotation direction is specified for the ribbon supply hub (4).
4. Hold transfer ribbon roll (3) firmly and turn knob on ribbon supply hub (4) counterclockwise until the transfer ribbon
roll is secured.
5. Slide suitable transfer ribbon core (1) onto the transfer ribbon take-up hub (2) and secure it in the same way.
6. Guide transfer ribbon through the print unit as shown in Fig. 17.
7. Secure starting end of transfer ribbon to the transfer ribbon core (1) with adhesive tape. Ensure counterclockwise
rotation direction of the transfer ribbon take-up hub here.
8. Turn transfer ribbon take-up hub (2) counterclockwise to smooth out the feed path of the transfer ribbon.
9. Turn lever (5) clockwise to lock the printhead.