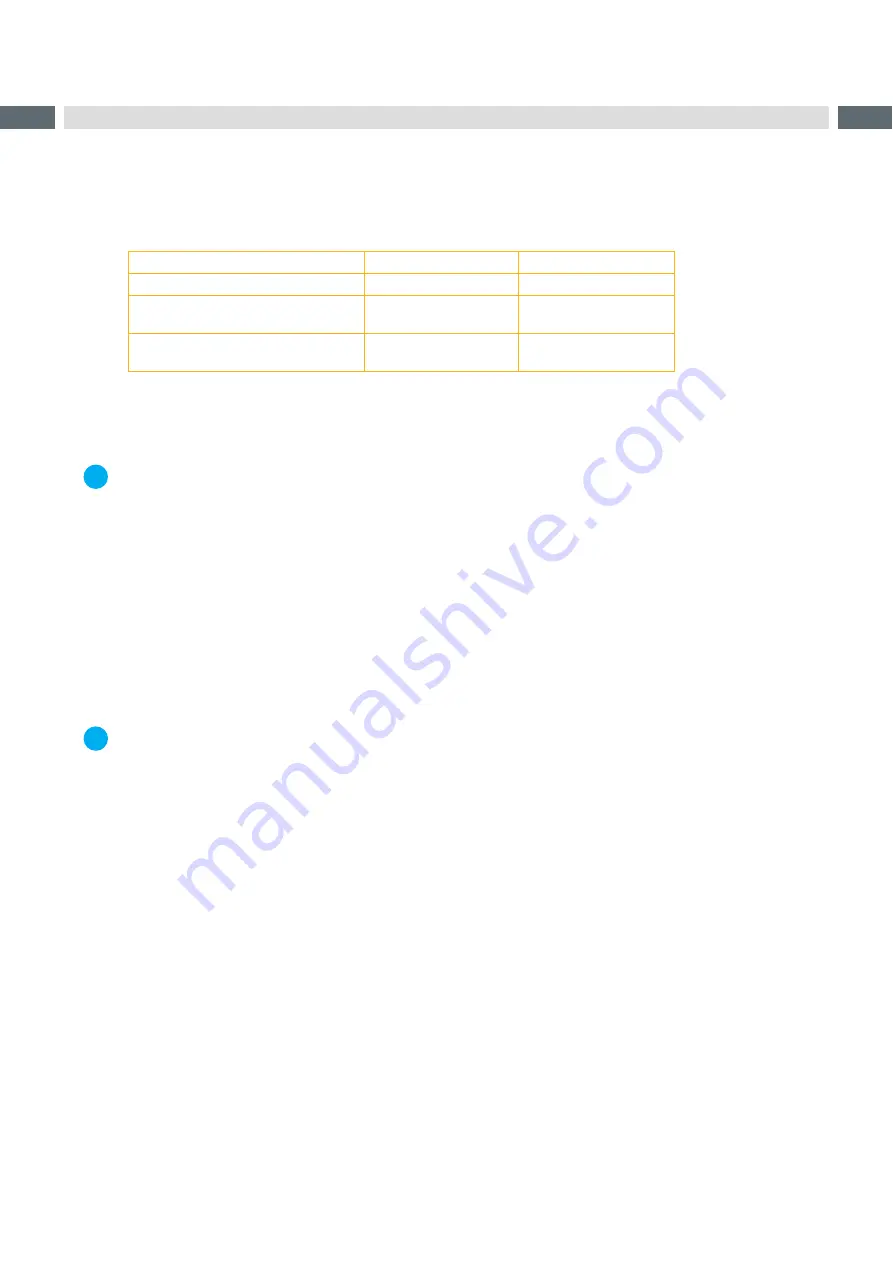
22
22
7
Configuration
The applicator can be operated in different ways. While the original process stays the same, the operation mode can
be chosen within the printer setup.
The most important setting is the selection between the operation modes "Stamp on" and "Blow on".
Additionally the applicator has different application modes concerning the order of printing and applying within one
labeling cycle.
Stamp on
Blow on
Print/Apply
x
x
Apply/Print
Waiting position up
x
x
Apply/Print
Waiting position down
-
x
Table 4
Operation and application modes
Additionally all operating modes can be adjusted by setting different time delays.
i
Note!
For more information about the printer configuration and the function of the keys in the navigator pad
Configuration manual of the printer or
Operator's manual of the printer
7.1
Method for Changing the Printer Setup
1. Press menu key.
2. Select
Setup > Machine param. > Applicator
.
3. Select and adjust the needed parameters
4. Return to the "Ready" mode.
7.2
Quick Mode for Setting the Delay Times
Beside the standard method for the printer configuration there is a quick mode to adjust the delay times available.
i
Note!
The quick mode settings can be made during operation . The changes affect directly the current print job.
1. Press the menu key for at least 2 seconds.
The first delay time appears on the display.
2. Adjust the delay time by pressing the
~
key and
key.
3. To switch between the different delay times press the
}
key.
4. To leave the quick setup mode press the
|
key.
The selected delay times are stored in the printer.