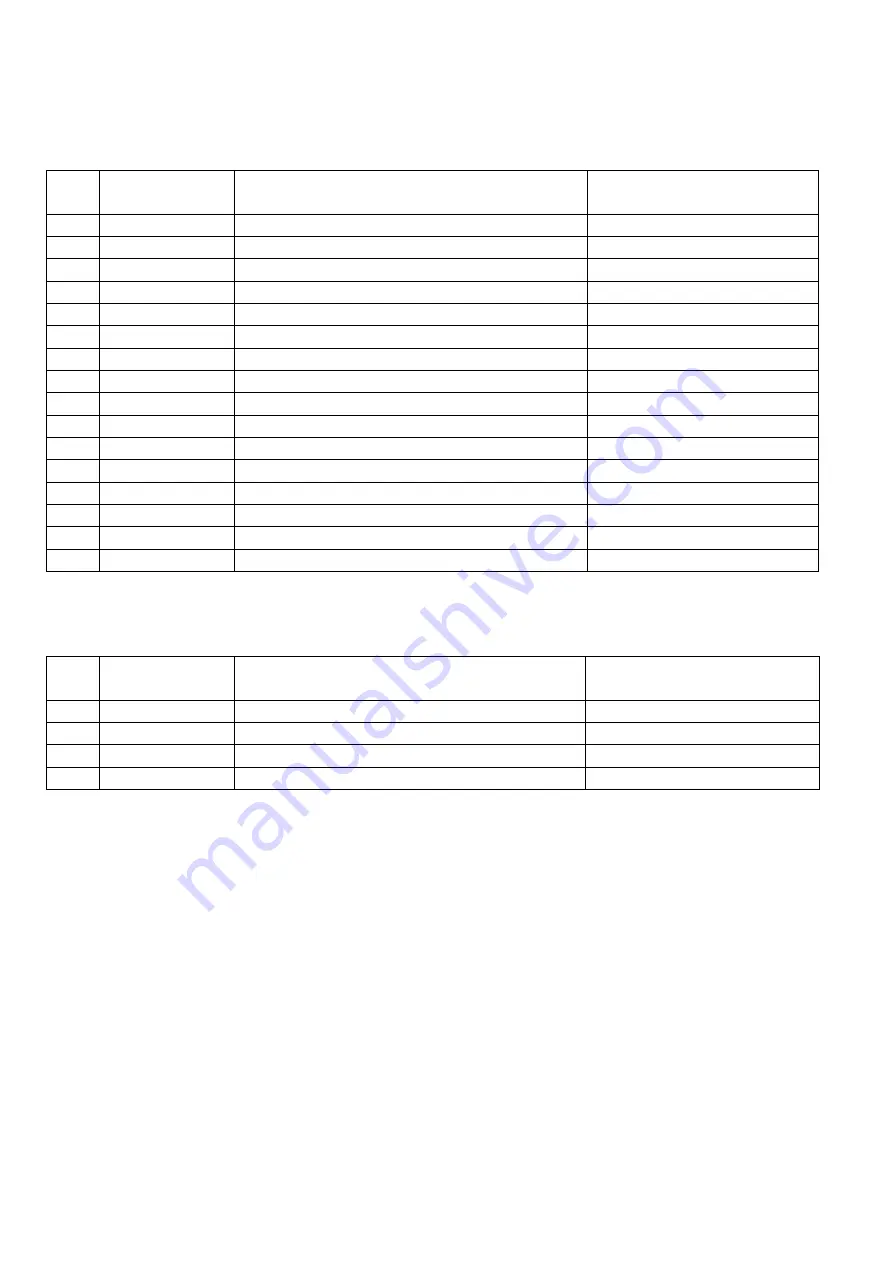
26
Spare part list
Options:
Nr. BWT Ordre
number
Discribtion
Change frequency
1
454100085
Service kit Dos pump
2
701993035
Eletrolyse Cell
3
701993030
Valveblock
4
750000980
PLC
5
120948250
Current sensor
6
405213250
Fitting R20
7
421801015
Brine pump.
8
321413000
Prefilter Cartrigde
1 year
9
251260004
Watermeter
10
By request
Static mixer
11
200729006
Nonretunr valve
12
101110006
Dosings hose
13
200746004
Drain valve
14
200721020
Test valve
15
101110006
Nethox hoses
16
454100074
Injection Nippel
Nr.
BWT Order
number
Description
Change frequency
17
200725006
Controllable checkvalve
18
321448802
BWT B-SAFE FILTER
If used.
19
By request
Option 1 – By-pass
20
321408510
Option 2 – E1 filter
1 year
Summary of Contents for Disinfecton
Page 8: ...8 Type Key...
Page 9: ...9 Product overview Electrical cabinet Hydraulic cabinet...
Page 27: ...27 Spare part drawings...
Page 28: ...28 PI diagram...
Page 29: ...29 Arrangement drawing...
Page 32: ...32 Declaration of Conformity...