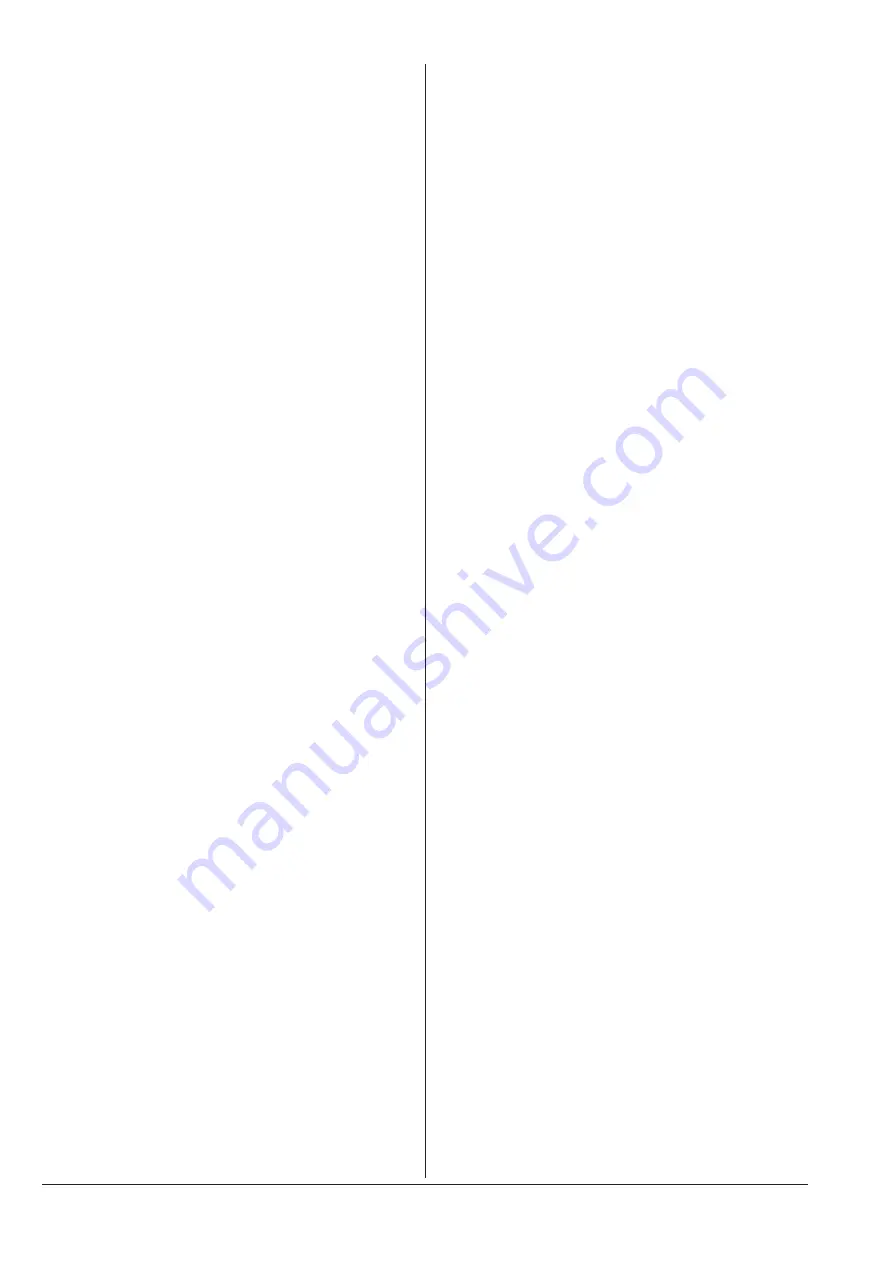
(k) or a partially clogged or obstructed discharge line.
Note
: Action of the safety valve will route (potentially explosive)
process gas into the environment of the pump! Furthermore the
safety valve is not designed for permanent action.
It is therefore necessary to check the safety valve every day: a
growing oil film on and/or around the safety valve must be taken
as an indication of too frequent operation of the safety valve, in
which case remedial action must be taken immediately. If a daily
inspection cannot be guaranteed, the safety valve must be re-
placed by a switch that will measure the pressure inside the bottom
chamber of the oil separator in order to issue a warning at
550 barg and to shut down the vacuum pump at 600 barg (pres-
sure monitoring equipment does not form part of the Busch scope
of delivery).
–
The drive motor and other electrical equipment must be selected
such that it will be sufficiently qualified for use in potentially explo-
sive atmosphere (in the responsibility of the manufacturer of the
superordinate machinery).
2. Avoidance of hazards to persons and goods from the effects of an
explosion that might happen inside the vacuum pump despite the
mentioned safety precautions.
–
Pressure proof design of the vacuum pump, capable of resisting a
pressure up to 18 barg without bursting.
–
The suction connection, the gas discharge and the safety valve fea-
ture flame arrestors (i) (k) (d), preventing flashbacks into the suc-
tion side, the discharge side and the environment of the system.
–
Flame arrestor (i) on the suction side of the vacuum pump with
slip-stream interruption.
Operational Options / Use of
Optionally Available Equipment
Operation with gas ballast, e.g. in order to avoid condensates, is
permitted.
The return of separated oil from the oil separator into the suction con-
nection (optional; required for continuous operation at intake pressures
higher than 300 hPa/mbar abs) is permitted.
Keeping the oil sump warm (optional heater), required for low ambient
temperatures (
Ú
Principle of Operation
The vacuum pump works on the rotating vane principle.
A circular rotor is positioned centrically on the shaft of the vacuum
pump. The shaft of the vacuum pump is driven by the drive motor
shaft by means of a flexible coupling.
The rotor rotates in an also circular, fixed cylinder, the centreline of
which is offset from the centreline of the rotor such that the rotor and
the inner wall of the cylinder almost touch along a line. Vanes (i), slid-
ing in slots in the rotor, separate the space between the rotor and the
cylinder into chambers. At any time gas is sucked in and at almost any
time ejected. Therefore the vacuum pump works almost pulsation free.
In order to avoid reverse rotation after switching off, the vacuum
pump is equipped with a non-return valve.
Note
: This valve shall not be used as a non-return valve or shut-off
valve to the vacuum system and is no reliable means to prevent suction
of oil into the vacuum system while the vacuum pump is shut down.
In case the vacuum pump is equipped with a gas ballast (optional):
Through the gas ballast a small amount of ambient air is sucked into
the pump chamber and compressed together with the process gas. This
counteracts the accumulation of condensates from the process gas in-
side the vacuum pump (
Ú
page 9: Conveying Condensable Vapours).
The gas ballast line is equipped with a sinter metal filter.
In order to improve the operating characteristics the outlet of the
pump chamber is equipped with a spring loaded valve.
Oil Circulation
The vacuum pump requires oil to seal the gaps, to lubricate the vanes
(i) and to carry away compression heat.
The oil reservoir is located on the pressure side of the vacuum pump
(i.e. high pressure) at the bottom of the bottom chamber of the oil
separator (j).
The feed openings are located on the suction side of the vacuum pump
(i.e. low pressure).
Forced by the pressure difference between pressure side and suction
side oil is being drawn from the oil separator (j) through the oil supply
lines and injected on the suction side.
Together with the sucked gas the injected oil gets conveyed through
the vacuum pump and ejected into the oil separator (j) as oil mist. Oil
that separates before the exhaust filter accumulates at the bottom of
the bottom chamber of the oil separator (j).
Oil that is separated by the exhaust filter accumulates at the bottom of
the upper chamber of the oil separator (j).
The flow resistance of the exhaust filters causes the inside of the ex-
haust filters (which is connected to the bottom chamber of the oil sep-
arator) to be on a higher pressure level than the outside of the exhaust
filters (i.e. the upper chamber of the oil separator). Because of the
higher pressure in the bottom chamber it is not possible to let oil that
drips off the exhaust filters simply flow down to the bottom chamber.
Version with oil return line to the suction connection:
Therefore the oil that accumulates in the upper chamber is sucked
through the oil return line right to the suction connection (i).
Version with oil return line to the B-cover:
Therefore the oil that accumulates in the upper chamber is sucked
through the oil return line right to the cylinder chamber.
Cooling
The vacuum pump is cooled by
–
radiation of heat from the surface of the vacuum pump incl. oil
separator (j)
–
the air flow from the fan wheel of the drive motor
–
the process gas
–
the air flow from the fan wheel (m) on the shaft of the vacuum
pump
Start Controls
The vacuum pump comes without start controls. The control of the
vacuum pump is to be provided in the course of installation.
Safety
Intended Use
Definition
: For the purpose of these instructions, “handling” the
vacuum pump means the transport, storage, installation, commission-
ing, influence on operating conditions, maintenance, troubleshooting
and overhaul of the vacuum pump.
The vacuum pump is intended for industrial use. It shall be handled
only by qualified personnel.
The allowed media and operational limits (
Ú
page 3: Product De-
scription) and the installation prerequisites (
Ú
page 6: Installation
Prerequisites) of the vacuum pump shall be observed both by the
manufacturer of the machinery into which the vacuum pump is to be
incorporated and by the operator.
The maintenance instructions shall be observed.
Prior to handling the vacuum pump these installation and operating
instructions shall be read and understood. If anything remains to be
clarified please contact your Busch representative!
Safety
RE 0016 B / RE 0040 B / RE 0063 B with safety valve, without motor
page 4
0870142823
Summary of Contents for R5 RE 0016 B
Page 21: ...blank page RE 0016 B RE 0040 B RE 0063 B with safety valve without motor 0870142823 page 21 ...
Page 22: ...blank page RE 0016 B RE 0040 B RE 0063 B with safety valve without motor page 22 0870142823 ...
Page 23: ...blank page RE 0016 B RE 0040 B RE 0063 B with safety valve without motor 0870142823 page 23 ...